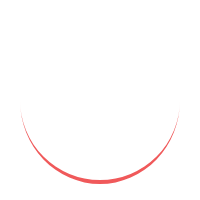
Sheet metal work involves the fabrication and manipulation of various types of metal sheets. It requires the use of specialized tools and machinery to shape, cut, and join metal sheets accurately. While modern technology has introduced automated machines, hand tools and manually operated machines continue to play a crucial role in sheet metal work. In this article, we will explore the importance of hand tools and manually operated machines, their function
Importance of Hand Tools in Sheet Metal Work
Hand tools are indispensable in sheet metal work, allowing workers to perform precise tasks and achieve desired outcomes. These tools are typically handheld, easy to operate, and provide excellent control over the material being worked on. Let's take a closer look at some of the common hand tools used by sheet metal workers.
Stud Welding Overview of Hand Tools
Hand tools are mechanical devices designed to be operated by hand, offering versatility and flexibility in sheet metal work. They are typically made from durable materials such as hardened steel or high-quality alloys, ensuring longevity and reliability.
Common Hand Tools Used by Sheet Metal Workers
Tin Snips: These handheld cutting tools are used to cut straight, curved, or irregular shapes in thin metal sheets.
Aviation Snips: Ideal for cutting through aluminum or sheet metal, aviation snips come in various types, including straight, left-cut, and right-cut.
Seamers: Used for bending or folding metal sheets, seamers are available in different designs, such as straight, offset, or duckbill.
Hammers: Sheet metal workers use hammers for shaping and forming metal, with ball-peen and cross-peen hammers being commonly used.
Files: Files help in smoothing rough edges and removing burrs from cut metal sheets, ensuring a clean finish.
Hand Seamers: These tools are used to create straight, uniform bends in metal sheets, providing accurate and consistent results.
Awls: Awls are used for marking or piercing metal sheets, helping sheet metal workers create precise reference points.
Scribers: Scribers are useful for marking lines on metal sheets, enabling accurate cutting and shaping.
Functions and Applications of Hand Tools in Sheet Metal Work
Hand tools serve various functions in sheet metal work, depending on their design and capabilities. Let's explore some of the primary functions and applications of hand tools in this field.
Cutting and Shaping Tools
Cutting and shaping tools enable sheet metal workers to create desired shapes and sizes. Tin snips and aviation snips, for example, allow for accurate cutting of metal sheets. Seamers and hand seamers aid in bending and folding metal, while hammers and mallets help shape and form the material.
Stud Welding Joining and Fastening Tools
Joining and fastening tools are essential for securely connecting metal sheets. Riveting tools and screws are commonly used for fastening metal parts together, while welding tools enable the fusion of metal pieces through heat and pressure. Clamps and vices provide stability during the joining process.
Stud Welding Measuring and Marking Tools
Measuring and marking tools play a crucial role in achieving precision and accuracy in sheet metal work. Instruments such as rulers, calipers, and protractors ensure proper measurements, while awls and scribers help in marking reference points and lines on metal sheets.
Manually Operated Machines in Sheet Metal Work
In addition to hand tools, sheet metal workers also utilize manually operated machines to perform various tasks. These machines provide increased efficiency and consistency in sheet metal work. Let's explore the different types of manually operated machines used in this field.
Stud Welding Types of Manually Operated Machines
Manual Shears: These machines are used for straight or curved cuts in metal sheets and come in different sizes to accommodate various sheet thicknesses.
Manual Brakes: Manual brakes are used for bending and folding metal sheets accurately, allowing for precise angles and shapes.
Manual Slip Rolls: Slip rolls are used for rolling metal sheets into cylindrical or conical shapes, commonly used in ductwork fabrication.
Bead Rollers: Bead rollers help create decorative or strengthening beads in metal sheets, enhancing their rigidity and appearance.
Manual Punch Press: Punch presses are used for punching holes in metal sheets, providing the capability to create precise patterns or perforations.
Stud Welding Uses and Advantages of Manually Operated Machines
Manually operated machines offer sheet metal workers several advantages. They provide greater control over the fabrication process, allowing for precise adjustments and customization. Additionally, these machines are often more affordable than their automated counterparts, making them accessible to small-scale fabricators and individual craftsmen.
Stud Welding Safety Considerations in Sheet Metal Work
Safety is paramount in sheet metal work due to the inherent risks associated with working with sharp tools, heavy materials, and potentially hazardous substances. It is crucial for sheet metal workers to follow proper safety guidelines to mitigate accidents and ensure a safe working environment.
Importance of Safety in Sheet Metal Work
Safety precautions help prevent injuries, accidents, and long-term health issues for sheet metal workers. By implementing safety measures, such as wearing personal protective equipment (PPE), maintaining a clean workspace, and using tools correctly, workers can minimize the risks associated with their profession.
Safety Measures for Hand Tools and Manually Operated Machines
Wear appropriate PPE, including safety glasses, gloves, and ear protection, to protect against hazards such as sharp edges, flying debris, and loud noises.
Inspect hand tools and manually operated machines regularly to ensure they are in good working condition, free from defects or damage.
Use tools for their intended purposes and follow proper techniques to avoid accidents caused by misuse or inappropriate handling.
Securely fasten metal sheets in place to prevent movement or slippage during cutting, shaping, or joining operations.
Maintain a clean and organized work area to minimize the risk of tripping or falling and to prevent potential injuries from misplaced tools or materials.
Follow manufacturer's instructions and recommended safety procedures when operating manually operated machines, including proper installation and adjustment.
Skills and Training for Sheet Metal Workers
Becoming a skilled sheet metal worker requires a combination of technical knowledge and hands-on experience. Let's explore the essential skills and training opportunities for aspiring sheet metal workers.
Essential Skills for Sheet Metal Work
Blueprint Reading: The ability to interpret and understand technical drawings and blueprints is crucial for accurately fabricating metal components.
Metalworking Techniques: Sheet metal workers must be proficient in various metalworking techniques, including cutting, bending, folding, and joining.
Math Skills: Basic mathematical skills are necessary for measuring and calculating dimensions, angles, and material quantities accurately.
Problem Solving: Sheet metal workers often encounter challenges during fabrication, and the ability to troubleshoot and find creative solutions is essential.
Attention to Detail: Precision and accuracy are critical in sheet metal work, and having a keen eye for detail helps ensure high-quality results.
Training and Certification for Sheet Metal Workers
Sheet metal workers typically receive training through apprenticeship programs or vocational schools. These programs provide a combination of classroom instruction and hands-on experience, allowing individuals to learn the necessary skills and techniques. Upon completing their training, aspiring sheet metal workers can pursue certification through organizations such as the Sheet Metal Workers' International Association (SMWIA).
Stud Welding FAQs
Q1: What are some common hand tools used by sheet metal workers?
A1: Some common hand tools used by sheet metal workers include tin snips, aviation snips, seamers, hammers, files, hand seamers, awls, and scribers.
Q2: Are there any safety guidelines to follow when using hand tools in sheet metal work?
A2: Yes, it is important to wear appropriate PPE, inspect tools regularly, use tools for their intended purposes, securely fasten metal sheets, and maintain a clean workspace.
Q3: What types of manually operated machines are used in sheet metal work?
A3: Some commonly used manually operated machines in sheet metal work include manual shears, manual brakes, manual slip rolls, bead rollers, and manual punch presses.
Q4: How long does it take to become a certified sheet metal worker?
A4: The duration to become a certified sheet metal worker varies depending on the training program or apprenticeship, typically ranging from three to five years.
Q5: Where can I find more information about sheet metal work and training opportunities?
A5: For more information about sheet metal work and training opportunities, you can visit the website of organizations such as the Sheet Metal Workers' International Association (SMWIA) or contact local vocational schools and apprenticeship programs.