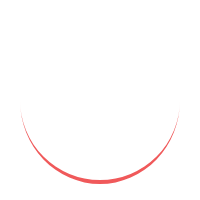
Quality inspection refers to the systematic examination and assessment of products or components to ensure they meet predetermined quality standards. It involves the inspection of various parameters such as dimensions, material composition, surface finish, mechanical properties, and more. Quality inspectors are responsible for detecting any flaws, defects, or non-conformities in the components and taking appropriate corrective measures.
Importance of Quality Inspection in Manufacturing
The importance of quality inspection in manufacturing cannot be overstated. It helps in maintaining product consistency, meeting customer expectations, complying with industry regulations, and reducing the risk of product failures or recalls. Quality inspection also enhances the reputation of manufacturers by ensuring that their products are reliable, durable, and of high quality.
Quality Inspection of Forged Components
Forged components are manufactured by subjecting metal to extreme heat and pressure, resulting in improved strength and durability. However, even forged components can have quality issues that need to be addressed through effective inspection techniques. Some common quality issues in forged components include cracks, voids, inclusions, dimensional deviations, and improper grain flow.
To ensure the quality of forged components, various inspection techniques are employed. These include visual inspection, non-destructive testing (NDT) methods such as magnetic particle inspection (MPI) and ultrasonic testing (UT), hardness testing, and dimensional inspection using precision measuring tools. By employing these techniques, quality inspectors can identify defects and deviations and make informed decisions regarding the acceptance or rejection of the components.
Quality Inspection of Casted Components
Casted components are manufactured by pouring molten metal into a mold, allowing it to solidify and take the desired shape. While the casting process offers versatility and cost-effectiveness, it can also introduce certain quality challenges. Common quality issues in casted components include porosity, shrinkage defects, surface irregularities, and dimensional variations.
Quality inspection techniques for casted components include visual inspection, radiographic testing (RT), liquid penetrant testing (PT), and pressure testing. These techniques enable inspectors to detect defects, cracks, or voids that may compromise the structural integrity or functionality of the casted components.
uality Inspection of Machined Components
Machined components are manufactured by removing material from a workpiece using various machining processes such as milling, turning, drilling, or grinding. While machining provides precise control over component dimensions and surface finish, it is essential to inspect these components for any deviations or defects.
Key quality inspection techniques for machined components include visual inspection, coordinate measuring machines (CMM), surface roughness measurement, hardness testing, and functional testing. These techniques help in verifying dimensional accuracy, surface finish, and other critical parameters required for the proper functioning of the machined components.
Comparative Analysis of Quality Inspection Methods
While each type of component has its own specific quality inspection techniques, it is essential to compare and evaluate the effectiveness of these methods. Factors such as cost, time efficiency, accuracy, reliability, and ease of implementation should be considered when selecting the appropriate inspection methods for different types of components.
Best Practices for Quality Inspection
To ensure effective quality inspection, manufacturers should adhere to certain best practices. These include having well-defined inspection procedures, utilizing appropriate inspection tools and equipment, training and certifying quality inspectors, conducting regular audits, and continuously improving the inspection process based on feedback and data analysis.
Quality Inspector-Forged, Casted or Machined Components FAQs
1. What is the role of a quality inspector in manufacturing?
A quality inspector is responsible for examining and assessing products or components to ensure they meet predetermined quality standards. They detect any flaws, defects, or non-conformities and take corrective measures to maintain product quality.
2. What are the common quality issues in forged components?
Common quality issues in forged components include cracks, voids, inclusions, dimensional deviations, and improper grain flow. These issues can affect the strength, durability, and functionality of the components.
3. What are some quality inspection techniques for casted components?
Quality inspection techniques for casted components include visual inspection, radiographic testing, liquid penetrant testing, and pressure testing. These techniques help in detecting defects and ensuring the structural integrity of the components.
4. How are machined components inspected for quality?
Machined components are inspected for quality through techniques such as visual inspection, coordinate measuring machines, surface roughness measurement, hardness testing, and functional testing. These methods verify dimensional accuracy, surface finish, and other critical parameters.
5. What are the best practices for effective quality inspection?
Best practices for quality inspection include having well-defined procedures, utilizing appropriate tools and equipment, training and certifying inspectors, conducting regular audits, and continuously improving the inspection process based on feedback and data analysis.