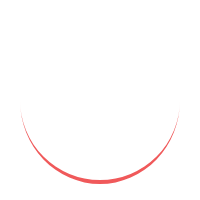
Quality assurance is a critical aspect of any business operation. It ensures that products and services meet or exceed customer expectations, comply with industry standards, and adhere to regulatory requirements. At the heart of effective quality assurance lies the role of a Quality Assurance Manager, a professional responsible for managing and improving the quality of processes, products, and services within an organization.
Introduction to Quality Assurance Manager
Quality Assurance Managers play a vital role in organizations across various industries, ranging from manufacturing and healthcare to software development and hospitality. They are responsible for designing and implementing quality control procedures, overseeing the entire quality management process, and ensuring that products and services meet the highest standards of quality.
Role and Responsibilities of a Quality Assurance Manager
As a Quality Assurance Manager, you have multifaceted responsibilities. Your primary goal is to ensure that the organization consistently delivers high-quality products and services to its customers. Some of the key responsibilities of a Quality Assurance Manager include:
Developing and implementing quality assurance policies and procedures.
Designing and conducting quality audits and inspections.
Creating and maintaining quality documentation, such as standard operating procedures and work instructions.
Identifying areas for process improvement and implementing corrective actions.
Collaborating with cross-functional teams to ensure quality goals are met.
Training and educating employees on quality standards and best practices.
Monitoring and analyzing quality metrics to drive continuous improvement.
Managing customer feedback and resolving quality-related issues promptly.
Importance of Quality Assurance in Business
Quality assurance is crucial for business success. It helps build customer trust, enhances brand reputation, reduces costs, and drives customer satisfaction. By ensuring that products and services meet or exceed quality expectations, businesses can differentiate themselves in a competitive market and foster long-term customer loyalty.
Skills and Qualifications Required for a Quality Assurance Manager
To excel as a Quality Assurance Manager, certain skills and qualifications are essential. These include:
Strong knowledge of quality assurance principles, methodologies, and best practices.
Excellent problem-solving and analytical skills.
Attention to detail and a meticulous approach to work.
Effective communication and interpersonal skills.
Leadership and team management abilities.
Proficiency in quality management tools and software.
Understanding of relevant industry regulations and compliance requirements.
Continuous learning and adaptability to stay updated with industry trends.
Steps to Become a Quality Assurance Manager
Becoming a Quality Assurance Manager requires a combination of education, experience, and personal development. Here are the steps you can take to pursue a career in quality assurance management:
Obtain a bachelor's degree in a relevant field such as quality management, engineering, or business administration.
Gain experience in quality assurance through internships or entry-level positions.
Pursue professional certifications such as Certified Manager of Quality/Organizational Excellence (CMQ/OE) or Certified Quality Auditor (CQA).
Continuously learn and update your knowledge in quality management methodologies and tools
Steps to Become a Quality Assurance Manager (continued)
Seek opportunities for professional development, such as attending workshops, conferences, and training programs related to quality assurance.
Develop a strong understanding of industry-specific regulations and standards.
Gain practical experience by working on quality assurance projects and initiatives.
Build a network of professionals in the field of quality assurance to exchange knowledge and insights.
By following these steps and continuously honing your skills and knowledge, you can pave the way towards a successful career as a Quality Assurance Manager.
Challenges Faced by Quality Assurance Managers
Quality Assurance Managers encounter various challenges in their roles. Some common challenges include:
Balancing quality objectives with business goals and constraints.
Navigating complex regulatory environments and compliance requirements.
Managing expectations and aligning stakeholders on quality standards.
Driving cultural change and ensuring buy-in from employees at all levels.
Addressing resource constraints and budget limitations.
Handling unforeseen quality issues and crises promptly.
Adapting to rapidly evolving technologies and industry trends.
Overcoming these challenges requires strong leadership, effective communication, and a proactive approach to problem-solving.
Strategies for Effective Quality Assurance Management
To excel as a Quality Assurance Manager, it is important to adopt effective strategies for quality assurance management. Some key strategies include:
Developing a comprehensive quality management system tailored to the organization's specific needs.
Establishing clear quality objectives and communicating them across the organization.
Implementing robust quality control processes, including inspections, tests, and audits.
Encouraging a culture of continuous improvement and employee involvement in quality initiatives.
Emphasizing training and development programs to enhance employee skills and knowledge.
Implementing quality performance metrics to measure progress and identify areas for improvement.
Regularly reviewing and updating quality documentation and procedures to reflect best practices.
By implementing these strategies, Quality Assurance Managers can effectively drive quality improvements and ensure the organization's long-term success.
Tools and Technologies Used in Quality Assurance
The field of quality assurance has witnessed significant advancements in tools and technologies that facilitate efficient quality management. Some commonly used tools include:
Statistical Process Control (SPC) software for real-time monitoring and analysis of quality data.
Test management software for organizing and executing software testing processes.
Quality management systems (QMS) that streamline documentation, audits, and compliance.
Automated testing tools for executing repetitive and time-consuming tests.
Data analysis and visualization tools for identifying trends and patterns in quality data.
Risk management software for assessing and mitigating potential quality risks.
Document control systems for managing and versioning quality documentation.
Adopting the right tools and technologies can significantly enhance the efficiency and effectiveness of quality assurance processes.
Best Practices for Quality Assurance Managers
Quality Assurance Managers can follow certain best practices to ensure successful quality management within their organizations. Some key best practices include:
Promoting a culture of quality throughout the organization, starting from top management.
Implementing a robust training and certification program for employees involved in quality-related activities.
Conducting regular internal audits to identify gaps and areas for improvement.
Encouraging cross-functional collaboration and knowledge sharing to leverage diverse expertise.
Embracing a data-driven approach by leveraging analytics to monitor and improve quality.
Fostering a proactive approach to problem-solving and addressing quality issues promptly.
Regularly reviewing and updating quality policies, procedures, and documentation.
By implementing these best practices, Quality Assurance Managers can establish a strong foundation for sustainable quality assurance and continuous improvement.
Quality Assurance Metrics and Key Performance Indicators (KPIs)
Measuring and tracking quality
Apologies for the interruption. Let's continue.
Quality Assurance Metrics and Key Performance Indicators (KPIs)
Measuring and tracking quality assurance performance is essential for evaluating the effectiveness of quality management processes. Quality Assurance Managers rely on various metrics and key performance indicators (KPIs) to assess the performance and identify areas for improvement. Some commonly used metrics and KPIs include:
Defect rate: The percentage of defective products or services identified during inspections or customer feedback.
Customer satisfaction score (CSAT): A measure of customer satisfaction with the quality of products or services.
First-pass yield (FPY): The percentage of products or services that meet quality standards on the first attempt without requiring rework or corrections.
Cycle time: The time taken to complete a quality control process, such as product testing or software validation.
Escaped defects: The number of defects that reach customers or end-users despite quality control measures.
On-time delivery: The percentage of products or services delivered to customers within the agreed-upon timeframe.
Cost of quality: The total cost incurred for quality assurance activities, including prevention, appraisal, and failure costs.
Defect density: The number of defects identified per unit of product or service.
By regularly monitoring these metrics and KPIs, Quality Assurance Managers can identify trends, measure progress, and take proactive measures to improve quality.
Quality Assurance Manager in Different Industries
The role of a Quality Assurance Manager is not limited to a specific industry. Quality assurance principles and practices are applicable across various sectors. Here's a glimpse of how Quality Assurance Managers contribute to different industries:
Manufacturing: Quality Assurance Managers in manufacturing ensure that production processes adhere to quality standards, monitor product quality at different stages, and implement corrective actions to maintain high-quality outputs.
Healthcare: Quality Assurance Managers in healthcare focus on ensuring patient safety, regulatory compliance, and continuous quality improvement in areas such as clinical processes, medical equipment, and patient care.
Software Development: Quality Assurance Managers in software development oversee the testing and quality control processes, ensuring that software applications and systems meet functional requirements, usability standards, and performance expectations.
Food and Beverage: Quality Assurance Managers in the food and beverage industry implement quality control procedures to ensure the safety, freshness, and compliance of food products, including monitoring ingredients, production processes, and packaging.
Construction: Quality Assurance Managers in construction oversee quality control procedures throughout the construction process, ensuring that building materials, workmanship, and safety standards meet regulatory requirements and customer expectations.
These examples demonstrate the diverse applications of quality assurance management and the critical role Quality Assurance Managers play in ensuring excellence in different industries.
Future Trends in Quality Assurance Management
The field of quality assurance is constantly evolving, driven by technological advancements and changing customer expectations. Some emerging trends that Quality Assurance Managers should be aware of include:
Artificial Intelligence (AI) and Machine Learning (ML): AI and ML technologies are being leveraged to automate quality control processes, analyze vast amounts of data for insights, and enable predictive maintenance to prevent quality issues.
Internet of Things (IoT): IoT devices are increasingly used in quality assurance to monitor and collect real-time data from production processes, enabling proactive quality management and minimizing defects.
Agile and DevOps Practices: Agile methodologies and DevOps practices are revolutionizing software development and quality assurance, emphasizing collaboration, continuous integration, and automated testing for faster and more reliable releases.
Risk-based Quality Management: Quality Assurance Managers are adopting risk-based approaches to prioritize quality control efforts based on the potential impact of defects on customer satisfaction, regulatory compliance, and business objectives.
Data Analytics and Business Intelligence: Advanced data analytics tools and business intelligence solutions are being used to extract actionable insights from quality data,
About Us
The Quality Assurance (QA) Manager will oversee the activity of the quality assurance department and staff, developing, implementing, and maintaining a system of quality and reliability testing for the organization's products and/or development processes.
Supervisory Responsibilities:
Hires and trains quality assurance staff.
Oversees the daily workflow and schedules of the department.
Conducts performance evaluations that are timely and constructive.
Handles discipline and termination of employees in accordance with company policy.
Duties/Responsibilities:
Develops, implements, and manages processes to ensure that products meet required specifications for quality, function, and reliability prior to delivery.
Identifies and sets appropriate quality standards and parameters for products.
Communicates quality standards and parameters to QA team, product development team, and other appropriate staff.
Coordinates product testing processes.
Participates in product testing.
Identifies and analyzes issues, bugs, defects, and other problems, particularly when problems recur in multiple products; recommends and facilitates solutions to these issues.
Reviews client, customer, and user feedback.
Maintains compliance with federal, state, local, and organizational laws, regulations, guidelines, and policies.
Performs other duties as assigned.
Required Skills/Abilities:
Excellent verbal and written communication skills.
Excellent interpersonal and customer service skills.
Excellent organizational skills and attention to detail.
Excellent time management skills with a proven ability to meet deadlines.
Strong analytical and problem-solving skills.
Strong supervisory and leadership skills.
Proficient with Microsoft Office Suite or related software.
Education and Experience:
Bachelor's degree in Business, Engineering, or field related to the products being developed required.
Three to five years of experience in a related field is required with supervisory experience a plus.
Physical Requirements:
Prolonged periods of sitting at a desk and working on a computer.
Must be able to lift up to 15 pounds at times.