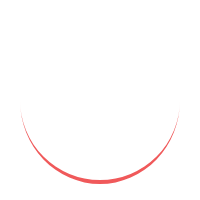
s play a crucial role in various manufacturing industries, ensuring that electronic components and other products are properly protected and cured for optimal performance and durability. In this article, we will explore the responsibilities, skills, challenges, best practices, and career opportunities associated with being a potting and curing operator.
Introduction
The field of manufacturing relies heavily on the expertise of potting and curing operators. These professionals are responsible for applying potting compounds and overseeing the curing process to create a protective barrier around delicate electronic components, circuit boards, and other products. By doing so, they enhance the performance, reliability, and lifespan of these items, making them suitable for use in a wide range of industries.
What is a Potting and Curing Operator?
A potting and curing operator is an individual trained to apply potting compounds or resins onto electronic components or products, such as circuit boards, sensors, or motors. The primary objective is to protect these items from environmental factors like moisture, dust, heat, and vibrations, which could otherwise lead to malfunctions or premature failure. The potting material acts as a barrier, encapsulating the component and providing insulation, mechanical support, and enhanced thermal management.
Responsibilities of a Potting and Curing Operator
Potting and curing operators have diverse responsibilities, including:
Preparing Workstations: They set up the necessary tools, equipment, and materials required for potting and curing processes.
Mixing and Preparing Potting Compounds: They accurately measure and mix the potting compounds or resins according to specified formulations or instructions.
Applying Potting Compounds: They carefully apply the potting material to electronic components, ensuring complete coverage and proper encapsulation.
Curing and Drying: They monitor and control the curing process, which involves subjecting the potting material to specific temperature, humidity, and time conditions for it to solidify or cure properly.
Quality Control: They perform visual inspections and conduct tests to ensure that the potting process meets quality standards and specifications.
Documentation: They maintain accurate records of potting procedures, including batch numbers, material usage, and any deviations from standard operating procedures.
Equipment Maintenance: They clean and maintain potting equipment to ensure optimal performance and longevity.
Potting and Curing Operator Skills and Qualifications
To excel as a potting and curing operator, certain skills and qualifications are essential:
Attention to Detail: A keen eye for detail is crucial to ensure accurate measurement and precise application of potting compounds.
Technical Aptitude: Familiarity with potting equipment, tools, and operating procedures is necessary to perform the job efficiently.
Problem-Solving Skills: Potting and curing operators should be able to identify and address issues or deviations during the potting process.
Teamwork and Communication: Effective communication and collaboration with team members and supervisors are vital in a manufacturing environment.
Manual Dexterity: The ability to handle small components and perform intricate tasks with essential for potting and curing operators.
Potting and Curing Operator Training and Certification
Potting and curing operators often receive on-the-job training from experienced professionals or undergo specialized training programs offered by manufacturing companies or vocational institutions. These training programs cover various aspects, including:
Potting Techniques: Operators learn different potting techniques, such as glob top, dam and fill, or complete encapsulation, to suit different product requirements.
Material Handling and Mixing: Training includes proper handling and mixing of potting compounds, understanding their properties, and following safety guidelines.
Curing Process Control: Operators are trained to monitor and control curing parameters, such as temperature, humidity, and time, to achieve optimal results.
Quality Assurance: Training emphasizes quality control procedures, visual inspections, and testing techniques to ensure adherence to quality standards.
Safety Procedures: Operators are educated about the potential hazards associated with potting materials and equipment, and learn safety protocols to mitigate risks.
Certification programs, such as IPC-A-610 or IPC/WHMA-A-620, are also available to validate the competence and knowledge of potting and curing operators. These certifications demonstrate the operator's proficiency in handling potting processes and compliance with industry standards.
Importance of Potting and Curing in Manufacturing
Potting and curing play a crucial role in manufacturing processes, offering several benefits:
Protection: Potting compounds provide a protective barrier, safeguarding electronic components from moisture, dust, chemicals, and mechanical stress.
Enhanced Performance: Potting materials improve thermal conductivity and dissipation, preventing overheating and ensuring optimal component performance.
Reliability and Durability: Proper potting and curing techniques increase product reliability, lifespan, and resistance to environmental factors and vibrations.
Electrical Insulation: Potting materials act as electrical insulators, reducing the risk of short circuits and electrical failures in sensitive electronic components.
Design Flexibility: Potting compounds offer design flexibility, allowing for custom-shaped encapsulation, secure bonding, and integration of multiple components into a single module.
By incorporating potting and curing processes, manufacturers can enhance the quality, reliability, and longevity of their products, meeting the demanding requirements of various industries.
Common Challenges Faced by Potting and Curing Operators
Potting and curing operations come with their fair share of challenges. Some common challenges include:
Material Selection: Choosing the right potting material with suitable properties, such as viscosity, cure time, and temperature resistance, can be challenging due to the wide range of available options.
Adhering to Specifications: Meeting strict specifications and standards for potting processes requires precise measurements, accurate mixing, and adherence to cure profiles.
Batch Consistency: Achieving consistent results across different batches while accounting for variations in environmental conditions and equipment settings can be a challenge.
Air Bubble Formation: Entrapped air bubbles during potting can affect the quality and reliability of the encapsulated components, requiring careful degassing techniques.
Complex Component Geometry: Potting intricate and complex component geometries necessitates specialized techniques to ensure complete encapsulation and coverage.
Best Practices for Potting and Curing Operators
To overcome challenges and ensure high-quality potting and curing, operators should follow these best practices:
Thorough Preparation: Properly prepare workstations, tools, and materials before starting the potting process to ensure efficiency and accuracy.
Material Testing: Conduct material compatibility tests, viscosity checks, and cure profile verifications to ensure the suitability of the potting material for the specific application.
Precise Mixing: Follow precise mixing ratios and techniques to ensure consistent material properties and reliable curing.
Potting and Curing Operator Degassing Techniques: Utilize
degassing techniques, such as vacuum chambers or centrifugal casting, to eliminate air bubbles and ensure proper encapsulation.
5. Temperature and Humidity Control: Maintain optimal temperature and humidity conditions during the curing process to achieve the desired material properties.
Quality Inspections: Perform visual inspections and conduct quality tests at various stages of the potting process to detect any defects or deviations.
Documentation and Record-Keeping: Maintain detailed records of potting procedures, including material batches, curing parameters, and any deviations from standard protocols.
Continuous Learning: Stay updated with advancements in potting technologies, materials, and best practices through continuous learning and professional development opportunities.
JOB DESCRIPTION
The tasks a Potting and Curing Operator is expected to perform include:
Understanding work requirement
Preparing potting compound
Potting the electronic assembly
Curing the potted assembly
Undertaking preventive maintenance of equipment
Achieving productivity and quality standards
WORK ENVIRONMENT
It is not a desk job
Need to handle a team of helpers
Local traveling is part of this job role
Part-time work and contractual jobs are available in some cities
Work from home option may be available
Working hours
Organizations usually work 5/6 days a week and 8/9 hours every day. This may vary from organization to organization
Shift system may be available
Overtime may be required
Being self-employed is also an option. In this case, the working hours and days will be flexible​