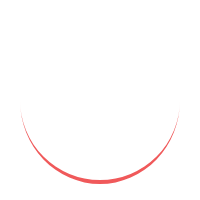
Electric Discharge Machining (EDM) has revolutionized the manufacturing industry, enabling precise and intricate machining of various materials. One of the notable advancements in this field is the Operator, a non-conventional electric discharge machine that utilizes spark erosion for precise material removal. In this article, we will explore the features, advantages, and applications of Operator, shedding light on its spark erosion process and how it compares to traditional EDM machines.
Understanding Electric Discharge Machining
Electric Discharge Machining has a rich history that dates back to the late 1940s. Originally developed for the purpose of removing broken drills and taps, EDM has undergone significant advancements over the years. These developments have led to the emergence of the Operator as a cutting-edge solution in the realm of spark erosion.
Basic Principles
EDM operates on the principle of spark erosion, where controlled electrical discharges are used to remove material from a workpiece. A dielectric fluid, typically deionized water, acts as a medium to facilitate the electrical discharge and cooling of the workpiece. This process allows for the precise erosion of conductive materials, including hardened steels, exotic alloys, and even electrically non-conductive ceramics.
Types of Electric Discharge Machines
Various types of EDM machines exist in the market today, each catering to specific machining requirements. These include Wire EDM, Sinker EDM, and the non-conventional Operator. While Wire and Sinker EDMs are well-established, Operator stands out as an innovative solution that utilizes spark erosion for material removal.
Exploring Non-conventional Electric Discharge Machines
The Operator represents a new era of electric discharge machining. By employing spark erosion, it offers distinct advantages over traditional EDM machines. The precision and efficiency of the Operator make it ideal for applications that demand intricate detailing and fine finishes.
Advantages of Operator
The Operator boasts several advantages that set it apart from conventional EDM machines. Firstly, its spark erosion process enables the machining of highly intricate shapes with exceptional accuracy. Additionally, it offers enhanced surface finishes, reducing the need for subsequent polishing or grinding operations. The Operator also excels in machining electrically non-conductive materials, expanding its versatility.
Applications of Operator
The versatility of the Operator opens up a wide range of applications across various industries. In aerospace and defense, it is employed to manufacture turbine blades, engine components, and intricate molds. The automotive sector utilizes the Operator for producing complex parts, such as gears and fuel injection systems. Furthermore, the medical and dental fields benefit from the Operator's ability to create intricate surgical instruments and dental prosthetics.
Spark Erosion Process in Operator
The spark erosion process in the Operator involves the controlled generation of electrical discharges between the workpiece and the electrode. As the sparks occur, localized melting and vaporization take place, eroding the material from the workpiece. The spark gap, pulse duration, and discharge energy are carefully controlled to achieve the desired material removal while minimizing surface damage.
Factors Affecting Spark Erosion
Several factors influence the spark erosion process in the Operator. The choice of dielectric fluid, electrode material, and spark parameters play a crucial role in determining the material removal rate, surface finish, and overall machining efficiency. Additionally, the conductivity and composition of the workpiece material impact the erosion process.
Features and Components of Operator
The Operator comprises several essential features and components that contribute to its exceptional performance. The machine structure is designed for stability and precision, ensuring consistent and accurate machining. A robust power supply and generator deliver the necessary electrical energy to facilitate spark erosion. The electrode and dielectric system enable efficient material removal and cooling, respectively.
Operating the Operator
Operating the Operator requires careful preparation and setup. The workpiece is securely clamped, and the electrode is aligned with the machining area. The dielectric fluid is circulated to ensure proper cooling and efficient debris flushing. The operator then selects the appropriate spark parameters based on the material and desired machining outcomes.
Controlling the Machining Process
Once the setup is complete, the machining process begins. The Operator allows for precise control of spark parameters, such as spark gap, pulse duration, and frequency. These parameters are adjusted based on the material, geometry, and desired surface finish. The operator monitors the machining process to ensure optimal performance and intervenes if necessary.
Advancements and Innovations in Operator
Advancements in the Operator have focused on improving precision and efficiency. Cutting-edge technologies enable finer control over spark parameters, resulting in more accurate material removal. The integration of advanced sensors and feedback systems ensures real-time monitoring and adjustment of machining conditions, further enhancing precision and efficiency.
Automation and CNC Integration
Operator machines are increasingly equipped with automation features and seamlessly integrate with Computer Numerical Control (CNC) systems. This integration enables automated toolpath generation, reducing human intervention and enhancing productivity. CNC integration also facilitates the machining of complex geometries and repetitive tasks with ease.
Comparing Operator with Traditional EDM Machines
Compared to traditional EDM machines, the Operator offers improved flexibility and accuracy. Its spark erosion process enables the machining of intricate shapes and contours that would be challenging to achieve with conventional methods. Moreover, the Operator delivers higher precision, resulting in tighter tolerances and reduced rework.
Enhanced Surface Finish
Another notable advantage of the Operator is its ability to produce superior surface finishes. The spark erosion process minimizes surface roughness, reducing the need for additional finishing operations. This saves time and resources while maintaining the desired quality of the machined parts.
Industry Applications of Operator
In the aerospace and defense industry, the Operator finds extensive use in manufacturing turbine blades, complex engine components, and intricate molds for aerospace structures. Its ability to achieve high precision and intricate detailing makes it indispensable in this sector.
Automotive
The automotive industry benefits from the Operator's capabilities in producing complex parts, such as gears, fuel injection systems, and engine components. The Operator's precision and efficiency contribute to improved performance and reliability of automotive components.
Medical and Dental
In the medical and dental fields, the Operator plays a crucial role in manufacturing intricate surgical instruments, dental implants, and prosthetics. Its ability to create complex shapes and precise geometries meets the stringent requirements of these industries.
Future Potential of Operator
As technology continues to advance, the Operator holds significant potential for further innovation and development. The integration of artificial intelligence and machine learning algorithms could enhance process control, predictive maintenance, and optimization of spark erosion parameters. Additionally, advancements in electrode materials and dielectric fluids could unlock new possibilities for the Operator in terms of machining capabilities and material compatibility.
Operator - Non-conventional Electric Discharge Machine Spark Erosion FAQs
Q1: Is the Operator suitable for machining non-conductive materials?
Yes, the Operator excels in machining non-conductive materials, such as ceramics. Its spark erosion process enables the removal of material from both conductive and non-conductive workpieces.
Q2: Can the Operator achieve high precision and tight tolerances?
Absolutely! The Operator is renowned for its ability to achieve exceptional precision and tight tolerances. Its spark erosion process allows for intricate detailing and precise material removal.
Q3: Does the Operator require extensive training to operate?
While familiarity with EDM principles is beneficial, modern Operator machines are designed with user-friendly interfaces and intuitive controls. With proper training and guidance, operators can quickly learn to operate the machine effectively.
Q4: Can the Operator be integrated with CNC systems?
Yes, the Operator can seamlessly integrate with CNC systems, offering automated toolpath generation and precise control over the machining process. This integration enhances productivity and expands the machine's capabilities.
Q5: What are the maintenance requirements for the Operator?
Regular maintenance, including cleaning and calibration, is necessary to ensure optimal performance of the Operator. Additionally, periodic checks and replacements of consumables, such as electrodes, may be required based on usage and wear.