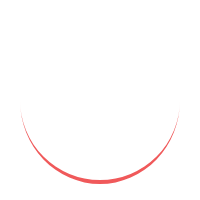
Broaching machines are essential tools in the manufacturing industry, widely used for shaping and finishing metal parts. Among the various types of broaching machines available, the operator - broaching machine stands out as a versatile and efficient option. In this article, we will explore the features, benefits, applications, and considerations associated with operator - broaching machines.
An operator - broaching machine is a mechanical device designed to perform broaching operations with the assistance of an operator. It combines the precision and power of a broaching machine with the control and flexibility provided by human intervention. Operator - broaching machines come in various configurations and can be adapted to different manufacturing requirements.
Types of Broaching Machines
There are several types of broaching machines available, each suitable for specific applications. The three main types are horizontal, vertical, and surface broaching machines.
Horizontal Broaching Machines
Horizontal broaching machines have a horizontal orientation, making them suitable for long workpieces that require linear cuts. They are commonly used in industries such as automotive and heavy machinery manufacturing.
Vertical Broaching Machines
Vertical broaching machines have a vertical orientation and are ideal for producing internal or external shapes. They are often used for creating keyways, splines, and gears in components like engine cylinders and turbine shafts.
Surface Broaching Machines
Surface broaching machines are specialized for surface finishing operations. They are capable of producing a high-quality surface finish on flat or contoured workpieces, making them valuable in industries where aesthetics and precision are crucial.
How Does an Operator - Broaching Machine Work?
Operating an operator - broaching machine involves several key steps, including setup, preparation, and the actual broaching process.
Setup and Preparation
Before starting the broaching process, the operator needs to ensure that the machine is properly set up. This involves selecting the appropriate broach, mounting it securely, and aligning the workpiece to achieve the desired cutting position.
Broaching Process
Once the setup is complete, the operator initiates the broaching process. The machine is activated, and the broach is guided through the workpiece while cutting progressively deeper with each pass. The operator controls the speed, feed rate, and depth of cut to achieve the desired results.
Tooling and Fixturing
Tooling and fixturing play a crucial role in the performance and accuracy of operator - broaching machines. The operator must ensure that the broach is sharp and in good condition, and that the workpiece is securely held in place during the cutting operation.
Advantages of Using an Operator - Broaching Machine
Operator - broaching machines offer several advantages over other machining methods, making them a popular choice in many industries.
High Precision
Operator - broaching machines deliver exceptional precision and accuracy, allowing for tight tolerances and complex shapes. The controlled operation and design of the broach ensure consistent results with minimal variation.
Efficiency and Productivity
With their efficient cutting action, operator - broaching machines can remove material quickly and effectively. This results in increased productivity and reduced production time compared to traditional machining methods.
Versatility
Operator - broaching machines are versatile tools that can handle a wide range of materials, including metals, plastics, and composites. They can be used for various applications, from creating internal keyways to shaping intricate contours.
Applications of Operator - Broaching Machines
Operator - broaching machines find applications in diverse industries due to their versatility and precision. Some common areas where these machines are employed include:
Automotive Industry
The automotive industry extensively utilizes operator - broaching machines for manufacturing engine components, gears, and transmission parts. The ability to create precise shapes and splines ensures the optimal performance and durability of these critical automotive parts.
Aerospace Industry
In the aerospace industry, operator - broaching machines are employed in the production of turbine blades, aircraft engine components, and landing gear parts. The high precision and strength of broached surfaces contribute to the reliable and safe operation of aerospace equipment.
Medical Industry
Operator - broaching machines play a vital role in the medical industry for manufacturing surgical instruments, implants, and medical devices. The machines' ability to create intricate shapes and profiles with high precision ensures the quality and functionality of these critical medical components.
Factors to Consider when Choosing an Operator - Broaching Machine
When selecting an operator - broaching machine, several factors should be taken into account to ensure the best fit for the intended application.
Capacity and Size
The capacity and size of the machine should align with the workpiece dimensions and production requirements. It is essential to consider the maximum length, width, and weight that the machine can accommodate.
Cutting Speed and Power
The cutting speed and power of the operator - broaching machine should match the material properties and desired production rate. Higher cutting speeds and power can lead to increased efficiency and reduced cycle times.
Automation and Controls
Depending on the level of automation required, operators may choose between manual, semi-automatic, or fully automated broaching machines. The selection should consider the desired production volume and the need for process control.
Maintenance and Support
Considering the long-term performance of the machine, availability of spare parts, and after-sales support is crucial. Regular maintenance, service, and technical assistance ensure the smooth operation and longevity of the operator - broaching machine.
Safety Considerations when Operating an Operator - Broaching Machine
Operating a broaching machine comes with certain safety risks, and adherence to safety guidelines is paramount to protect the operator and maintain a safe working environment.
Personal Protective Equipment (PPE)
Operators must wear appropriate personal protective equipment, including safety glasses, gloves, and protective clothing, to prevent injuries from flying chips, sharp tools, and other hazards.
Machine Guarding
Broaching machines should be equipped with safety guards and interlocks to prevent access to moving parts during operation. These guards provide a physical barrier to protect the operator from potential accidents.
Proper Training and Certification
Operators should receive proper training on the operation and safety procedures of the specific operator - broaching machine they are using. Certification programs ensure that operators have the necessary knowledge and skills to operate the machine safely and efficiently.
Maintenance and Care for Operator - Broaching Machines
To maintain optimal performance and extend the lifespan of an operator - broaching machine, regular maintenance and care are essential.
Regular Inspection and Lubrication
Operators should conduct routine inspections to identify any signs of wear or damage. Lubrication of moving parts is crucial to ensure smooth operation and prevent excessive friction and premature component failure.
Tool Maintenance
Proper maintenance of broaching tools is essential for maintaining cutting performance and accuracy. Regular sharpening, reconditioning, and replacement of worn-out tools are necessary to achieve consistent results.
Cleaning and Storage
Operators should clean the machine after use to remove any debris or chips that could affect its performance. Proper storage in a clean and dry environment helps prevent corrosion and damage to the machine and its components.
Future Trends in Operator - Broaching Machines
The field of operator - broaching machines continues to evolve, driven by technological advancements and industry demands. Some future trends to watch for include:
Advanced Automation and Robotics
Automation and robotics are being increasingly integrated into operator - broaching machines to enhance productivity, precision, and process control. Robotic loading and unloading systems, as well as advanced control algorithms, are becoming more prevalent.
Integration with Industry 4.0
Operator - broaching machines are being connected to the Internet of Things (IoT) and integrated into the digital manufacturing landscape. Real-time monitoring, data analytics, and predictive maintenance capabilities are being implemented to optimize machine performance and minimize downtime.
Operator - Broaching Machine Frequently Asked Questions
What is the difference between a horizontal and vertical broaching machine?
Horizontal broaching machines have a horizontal orientation and are suitable for long workpieces, while vertical broaching machines have a vertical orientation and are used for internal or external shapes.
Can operator - broaching machines handle complex shapes?
Yes, operator - broaching machines are capable of handling complex shapes with high precision, making them ideal for intricate machining requirements.
How often should an operator - broaching machine be inspected?
Regular inspections should be conducted on an operator - broaching machine to identify any signs of wear, damage, or maintenance requirements. The frequency of inspections may vary based on the machine's usage and operating conditions.
Is special training required to operate a broaching machine?
Yes, operators should receive proper training on the operation and safety procedures specific to the operator - broaching machine they are using. Certification programs are available to ensure operators have the necessary skills and knowledge.
Are there any environmental considerations when using broaching machines?
Environmental considerations may include proper waste management and disposal of cutting fluids, chips, and other byproducts generated during the broaching process. Operators should adhere to applicable environmental regulations and guidelines.