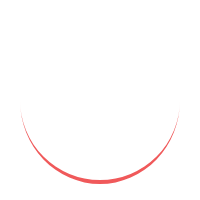
Gas Metal Arc Welding (GMAW), also known as Metal Inert Gas (MIG) welding or Metal Active Gas (MAG) welding, is a widely used welding process that provides high productivity and versatility. In this article, we will explore the working principles, advantages, applications, equipment, safety precautions, techniques, troubleshooting, and future trends of GMAW. So, let's dive into the world of GMAW and understand why it has become one of the most popular welding techniques today.
GMAW, or Gas Metal Arc Welding, is a welding process that uses a continuously fed consumable electrode wire and a shielding gas to create an electric arc between the electrode and the workpiece. The electric arc generates intense heat, melting the electrode wire and the base metal, resulting in a weld joint. GMAW is commonly performed with the help of a welding machine, a power source, a wire feeder, a welding gun, and a shielding gas supply.
3. How does a GMAW work?
GMAW works by establishing a circuit between the welding machine, the electrode wire, and the workpiece. When the welding machine is turned on, a high amperage current flows through the circuit, creating an electric arc between the electrode wire and the workpiece. The electric arc generates the necessary heat to melt the electrode wire and the base metal, creating a weld pool. The consumable electrode wire is continuously fed into the weld pool, providing the necessary filler material.
4. Advantages of GMAW
GMAW offers several advantages that contribute to its popularity in the welding industry. Some of the key advantages include:
a) High welding speed: GMAW allows for faster welding compared to other processes, making it ideal for projects that require high productivity.
b) Versatility: GMAW can be used to weld various metals, including carbon steel, stainless steel, aluminum, and copper alloys, making it a versatile welding process.
c) Less post-weld cleanup: The use of shielding gas in GMAWhelps to create a clean and controlled welding environment, reducing the need for extensive post-weld cleanup.
d) Reduced weld defects: GMAW produces high-quality welds with minimal defects, ensuring stronger and more reliable weld joints.
e) Easy automation: GMAW can be easily automated, allowing for efficient and precise welding in large-scale manufacturing processes.
5. Applications of GMAW
GMAW finds extensive applications across various industries due to its versatility and efficiency. Some common applications of GMAW include:
a) Automotive industry: GMAW is widely used in the automotive industry for manufacturing and repairing vehicle components, such as body panels, frames, and exhaust systems.
b) Construction sector: GMAW is employed in the construction sector for fabricating structural steel, pipelines, and architectural metalwork.
c) Manufacturing industry: GMAW plays a crucial role in the manufacturing industry for welding metal components, machinery, and equipment.
d) Aerospace industry: GMAW is utilized in the aerospace industry to join intricate and critical components, ensuring the integrity and safety of aircraft structures.
6. Types of GMAW processes
GMAW encompasses various processes, each suited for specific applications and requirements. The three primary types of GMAW processes are:
a) Short-circuiting transfer
Short-circuiting transfer, also known as short arc GMAW, involves the wire electrode making momentary contact with the weld pool, creating a short circuit. This process is ideal for welding thin materials and produces low heat input, minimal spatter, and good control over the weld puddle.
b) Globular transfer
Globular transfer involves the electrode wire forming large droplets that detach and transfer across the arc to the weld pool. This process is typically used for welding thicker materials and provides good penetration and deposition rates, although it may result in more spatter.
c) Spray transfer
Spray transfer is characterized by the electrode wire forming a fine spray of molten droplets that are propelled across the arc into the weld pool. This process is suitable for welding thick materials at high deposition rates, offering excellent penetration and high-quality welds.
7. Equipment required for GMAW
To perform GMAW effectively, certain equipment is necessary. The key equipment includes:
a) Power source: The power source supplies the electrical current required to create the arc. It can be a constant voltage (CV) or constant current (CC) machine, depending on the application.
b) Wire feeder: The wire feeder is responsible for feeding the consumable electrode wire at a consistent rate into the weld pool. It ensures a steady supply of filler material.
c) Electrode: The electrode, also known as the welding wire, is a consumable wire that melts and becomes part of the weld joint. It comes in various diameters and compositions based on the materials being welded.
d) Shielding gas: The shielding gas protects the weld pool from atmospheric contamination during the welding process. Common shielding gases include argon, carbon dioxide, or a mixture of both.
e) Welding gun: The welding gun holds the electrode wire and provides the means to control the welding process. It includes a trigger for wire feeding, gas flow control, and sometimes additional features like a nozzle or contact tip.
8. Safety precautions for GMAW
While working with GMAW, it is crucial to prioritize safety. Some important safety precautions include:
a) Personal protective equipment: Welders should wear appropriate personal protective equipment (PPE) such as welding helmets, safety glasses, gloves, and flame-resistant clothing to protect themselves from sparks, UV radiation, and potential hazards.
b) Ventilation: Adequate ventilation is necessary to prevent the accumulation of harmful fumes and gases generated during the welding process. Working in well-ventilated areas or using local exhaust ventilation systems is recommended.
c) Fire safety measures: Welding can pose a fire hazard, so it's important to have fire safety measures in place. This includes keeping a fire extinguisher nearby, removing flammable materials from the work area, and following proper fire safety protocols.
9. Setting up a GMAW machine
To set up a GMAW machine, follow these general steps:
a) Power connection: Ensure the welding machine is properly connected to a reliable power source.
b) Gas supply: Connect the shielding gas supply to the machine, ensuring the appropriate flow rate for the specific welding process and materials.
c) Wire feeding: Load the appropriate electrode wire onto the wire feeder, ensuring proper alignment and tension. Adjust the wire feed speed based on the welding parameters.
d) Ground connection: Connect the workpiece to the welding machine using a proper grounding clamp to establish a reliable electrical circuit.
e) Welding parameters: Set the welding parameters such as voltage, current, and wire feed speed based on the material thickness, joint configuration, and desired welding characteristics.
10. GMAW techniques and tips
To achieve optimal results with GMAW, consider the following techniques and tips:
a) Proper joint preparation: Ensure the joint edges are clean, free from contaminants, and properly prepared to promote good weld penetration and strength.
b) Maintain consistent travel speed: Maintain a consistent travel speed while welding to achieve even bead appearance and proper fusion between the base metal and filler material.
c) Electrode extension: Maintain an appropriate electrode extension (stick-out) to control the heat input and the welding arc length. The recommended extension may vary based on the specific welding process and application.
d) Angle and gun movement: Maintain the proper gun angle and movement to control the weld pool, achieve good fusion, and minimize spatter.
11. Common troubleshooting in GMAW
While performing GMAW, welders may encounter certain issues. Here are some common troubleshooting tips:
a) Excessive spatter: Excessive spatter can occur due to high welding currents, incorrect shielding gas flow, or improper electrode stick-out. Adjusting these parameters can help reduce spatter.
b) Inadequate penetration: Inadequate penetration can result from low welding currents, insufficient electrode stick-out, or improper travel speed. Adjusting these parameters can improve penetration.
c) Porosity: Porosity, or the presence of gas pockets in the weld, can occur due to contaminated base metal, inadequate shielding gas coverage, or improper welding technique. Ensuring clean base metal and proper shielding gas flow can help minimize porosity.
12. Maintaining and cleaning GMAW equipment
Proper maintenance and cleaning of GMAW equipment are essential for its longevity and optimal performance. Some important maintenance tasks include:
a) Regular inspections: Inspect the welding machine, wire feeder, welding gun, and other components regularly to identify any signs of wear, damage, or malfunction.
b) Cleaning: Clean the welding gun, contact tip, and nozzle regularly to remove spatter, debris, and contamination. This ensures smooth wire feeding and proper shielding gas flow.
c) Wire and gas management: Properly store and handle the electrode wire and shielding gas cylinders to prevent damage and contamination. Follow manufacturer guidelines for handling and storage.
13. Comparing GMAW with other welding processes
GMAW has its own strengths and limitations when compared to other welding processes. Here are a few comparisons:
a) GMAW vs. SMAW: GMAW offers higher productivity, cleaner welds, and easier automation compared to Shielded Metal Arc Welding (SMAW), which is slower and requires manual electrode change.
b) GMAW vs. TIG welding: GMAW provides higher welding speed and easier operation compared to Tungsten Inert Gas (TIG) welding, which offers better control, higher precision, and cleaner welds.
c) GMAW vs. Flux-cored arc welding: GMAW is cleaner, produces less spatter, and offers higher welding speeds compared to Flux-cored Arc Welding (FCAW), which provides better penetration and higher deposition rates in certain applications.
14. Future trends and innovations in GMAW
The field of GMAW continues to evolve with advancements in technology and welding techniques. Some future trends and innovations include:
a) Digitalization and automation: The integration of digital technologies and automation systems is expected to further enhance productivity, precision, and control in GMAW processes.
b) Welding process optimization: Ongoing research aims to optimize GMAW parameters, electrode wire compositions, and shielding gases for improved efficiency, reduced environmental impact, and enhanced weld quality.
c) Augmented reality (AR) and virtual reality (VR): AR and VR technologies may be utilized to provide real-time guidance and training for welders, improving their skills and overall performance.
5. Applications of GMAW FAQs
1. Is GMAW suitable for welding aluminum?
Yes, GMAW is commonly used for welding aluminum. However, it requires specific equipment, such as a spool gun or push-pull system, and the use of appropriate shielding gases, such as pure argon or argon-helium mixtures.
2. Can GMAW be used for welding thick materials?
Yes, GMAW can be used to weld thick materials. The spray transfer process, in particular, provides high deposition rates and deep penetration, making it suitable for welding thicker sections.
3. What is the difference between MIG and MAG welding?
MIG stands for Metal Inert Gas welding, which uses inert gases like argon or helium for shielding. MAG stands for Metal Active Gas welding, which uses active gases like carbon dioxide or oxygen for shielding. The choice between MIG and MAG depends on the specific application and the material being welded.
4. How important is proper ventilation during GMAW?
Proper ventilation is crucial during GMAW to remove welding fumes and gases from the work area. Inadequate ventilation can lead to the accumulation of hazardous substances, posing health risks to the welder and others in the vicinity.
5. Can GMAW be used for outdoor welding?
Yes, GMAW can be used for outdoor welding. However, wind and air movement can affect shielding gas coverage, so additional measures like windbreaks or flux-cored wires may be necessary to ensure proper protection and weld quality.