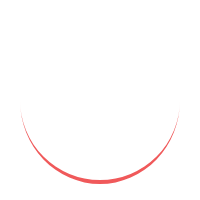
Introduction
In the world of printed circuit board (PCB) manufacturing, the role of a solder masking and legend printing operator is crucial. Solder masking is a process that involves applying a protective layer to the PCB surface, while legend printing adds essential information and markings to the board. This article explores the significance of solder masking and legend printing, the various materials and techniques involved, as well as the challenges faced by operators in ensuring high-quality results.
What is Solder Masking?
Solder masking, also known as solder resist or solder stop mask, is a process in which a layer of material is applied to the PCB surface, leaving only the desired areas exposed for soldering. The primary purpose of solder masking is to protect the underlying copper traces and pads from unintentional solder bridges and short circuits during the assembly process.
Importance of Solder Masking in PCB Manufacturing
Solder masking plays a crucial role in ensuring the reliability and functionality of PCBs. Here are a few key reasons why it is important:
Protection against short circuits and solder bridges: By covering the areas where solder should not be applied, solder masking prevents accidental connections between adjacent traces or pads, reducing the risk of short circuits.
Prevention of solder wicking: Solder wicking can occur when solder travels along exposed copper traces, leading to weak or unreliable connections. Solder mask prevents the solder from spreading beyond the designated areas, ensuring proper solder joint formation.
Enhancing solder joint reliability: Solder masking improves the overall solder joint reliability by reducing the likelihood of oxidation and contamination on exposed copper surfaces. It also helps to protect the PCB from environmental factors such as moisture and dust.
Types of Solder Masking Materials
There are different types of solder masking materials available, each with its own characteristics and application methods. Some common types include:
Liquid Photoimageable (LPI) Solder Mask: LPI solder mask is a liquid material that is typically applied using a screen printing process. It is then exposed to UV light through a photomask, which defines the desired pattern. LPI solder mask offers excellent coverage and resolution.
Dry Film Solder Mask: Dry film solder mask is a solid, photosensitive material that comes in the form of a thin sheet. It is laminated onto the PCB surface and then exposed to UV light through a photomask to define the solder mask pattern. Dry film solder mask is known for its high resolution and durability.
Thermal Cure Solder Mask: Thermal cure solder mask is a liquid material that is applied to the PCB surface and then cured at an elevated temperature. It provides good adhesion and chemical resistance, making it suitable for more demanding applications.
Solder Masking Process
The solder masking process involves several steps to ensure proper application and quality control:
Surface preparation: Before applying the solder mask, the PCB surface needs to be thoroughly cleaned and prepared. Any residues, oils, or contaminants should be removed to ensure good adhesion of the solder mask material.
Application of solder mask: The solder mask material is applied to the PCB surface using the chosen method, such as screen printing or lamination. The solder mask is applied in the desired pattern, leaving exposed areas for soldering.
Curing and drying: Once the solder mask is applied, it needs to be cured or dried according to the manufacturer's instructions. This step helps the solder mask material to solidify and form a protective layer.
Inspection and quality control: After curing, the solder mask undergoes thorough inspection to check for any defects, such as pinholes, uneven coverage, or improper thickness. Quality control measures ensure that the solder mask meets the required specifications.
Challenges and Best Practices in Solder Masking
Solder masking can pose certain challenges for operators. Here are some common challenges and best practices to overcome them:
Ensuring proper thickness and coverage: Achieving consistent solder mask thickness and complete coverage over the desired areas is crucial for its effectiveness. Operators should carefully control the application process and use appropriate tools to ensure uniformity.
Avoiding trapped air and bubbles: Air entrapment and the formation of bubbles can lead to defects in the solder mask layer. Operators should pay attention to proper material flow, use deaeration techniques, and apply the solder mask evenly to prevent such issues.
Handling fine pitch components: Fine pitch components with closely spaced pads present a challenge for solder masking. Operators need to use techniques like stencil printing or specialized equipment to ensure accurate application without smearing or misalignment.
Solder Masking & Legend Printing Operator Introduction to Legend Printing
Legend printing is the process of adding markings, text, symbols, and component designations to the PCB surface. These legends provide crucial information for PCB assembly, testing, and troubleshooting. The legend printing process typically follows the solder masking process.
Solder Masking & Legend Printing Operator Purpose of Legend Printing
The primary purpose of legend printing is to convey important information about the PCB and its components. Some common elements included in legends are:
Component designators: These are alphanumeric codes or labels that identify individual components on the PCB.
Reference designators: These labels indicate the location of components on the PCB, helping with assembly and troubleshooting.
Part numbers: Legends may include part numbers for easy identification and inventory management.
Logos and trademarks: Legends may include logos, trademarks, or branding elements to represent the manufacturer or designer.
Solder Masking & Legend Printing Operator Legend Printing Techniques
There are different techniques used for legend printing, each offering unique advantages:
Screen Printing: Screen printing is a common technique where ink is pushed through a fine mesh screen onto the PCB surface. The screen acts as a stencil, allowing precise placement of the legends. Screen printing provides good durability and legibility.
Inkjet Printing: Inkjet printing uses specialized printers to directly deposit ink onto the PCB surface. It offers flexibility in terms of design
and can easily accommodate changes in legend content. Inkjet printing is known for its high resolution and the ability to print intricate details.
Challenges and Best Practices in Legend Printing
Legend printing requires attention to detail to ensure legibility and accuracy. Here are some challenges faced by operators and best practices to address them:
Ensuring legibility and accuracy: Legends should be clear and easily readable, even on small components. Operators should use appropriate font sizes, consider contrast between the legend and PCB surface, and ensure proper ink adhesion for longevity.
Selection of appropriate inks and materials: Different inks and materials may be suitable for different PCB types and requirements. Operators should choose inks that provide good adhesion, durability, and resistance to environmental factors such as moisture, chemicals, and temperature variations.
Solder Masking & Legend Printing Operator FAQs
What is the purpose of solder masking in PCB manufacturing?
Solder masking is applied to PCBs to protect the underlying copper traces and pads from accidental short circuits and solder bridges during the assembly process. It also prevents solder wicking and enhances solder joint reliability.
How does solder masking protect against short circuits?
Solder masking covers the areas where solder should not be applied, preventing unintended connections between adjacent traces or pads, thus reducing the risk of short circuits.
What are the different types of solder masking materials?
Some common types of solder masking materials include liquid photoimageable (LPI) solder mask, dry film solder mask, and thermal cure solder mask.
What is the significance of legend printing on PCBs?
Legend printing provides essential information such as component designators, reference designators, part numbers, and logos. It helps with PCB assembly, testing, and troubleshooting.
Which legend printing technique is more commonly used?
Screen printing and inkjet printing are both popular legend printing techniques. Screen printing offers durability, while inkjet printing provides high resolution and flexibility in design.
About Us
The individual in this job prints an epoxy-ink-based solder mask using hand tools or coating machines and apply a white letter marking to indicate the component placed on each side of the PCB.