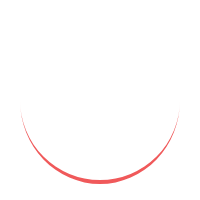
In today's dynamic and highly regulated manufacturing industry, ensuring product quality and compliance with regulatory standards is of paramount importance. Process validation plays a crucial role in achieving these objectives, and process validation executives are key professionals responsible for overseeing and executing this critical process. In this article, we will explore the role of a process validation executive, the steps involved in process validation, regulatory requirements, challenges, best practices, and future trends in this field.
Introduction
Process validation is a systematic approach used to establish documentary evidence that a manufacturing process consistently produces a product of desired quality. It involves a series of activities to demonstrate that a manufacturing process is capable of consistently meeting predetermined specifications and quality attributes. A process validation executive plays a vital role in this process, ensuring that the manufacturing operations are in compliance with regulatory guidelines and industry standards.
What is Process Validation?
Process validation is the documented evidence that a process consistently produces a product meeting predetermined specifications and quality attributes. It involves evaluating and controlling various parameters to ensure the manufacturing process consistently produces high-quality products that meet customer expectations. By validating the process, manufacturers gain confidence in their ability to consistently produce safe and effective products.
Importance of Process Validation
Process validation is crucial for several reasons. Firstly, it helps to ensure patient safety by minimizing the risks associated with product variability and potential defects. By validating the manufacturing process, companies can identify and mitigate any potential sources of variability or failure. Secondly, process validation helps to maintain product quality and consistency throughout the manufacturing lifecycle, which is vital for building customer trust and satisfaction. Finally, regulatory authorities require process validation as a means to ensure compliance with industry standards and regulations.
Roles and Responsibilities of a Process Validation Executive
As a process validation executive, one has a multifaceted role in the manufacturing organization. Some of the key responsibilities include:
Development of Validation Strategies: Collaborating with cross-functional teams to develop comprehensive strategies for process validation, ensuring alignment with regulatory requirements and company objectives.
Execution of Validation Protocols: Overseeing the execution of validation protocols and ensuring compliance with predefined acceptance criteria. This involves coordinating with various departments, conducting experiments, analyzing data, and generating reports.
Risk Assessment and Mitigation: Identifying potential risks associated with the manufacturing process and implementing appropriate risk mitigation strategies. This includes performing risk assessments, developing risk control plans, and monitoring their effectiveness.
Continuous Improvement: Continuously monitoring and evaluating the manufacturing process to identify areas for improvement. This involves analyzing process data, conducting root cause analysis, and implementing corrective and preventive actions.
Process Validation Executive Key Skills Required
To excel as a process validation executive, certain key skills are essential. These include:
Strong Analytical Skills: The ability to analyze complex data sets, identify trends, and draw meaningful conclusions is crucial for process validation professionals. Strong analytical skills enable them to make data-driven decisions and drive process improvements.
Regulatory Knowledge: In-depth knowledge of relevant regulatory requirements and guidelines is necessary to ensure compliance during the validation process. Process validation executives must stay updated with the latest regulatory developments in their respective industries.
Attention to Detail: Process validation involves meticulous attention to detail to ensure accuracy and completeness in documentation, data analysis, and execution of validation protocols. Small errors or oversights can have significant consequences, so a keen eye for detail is crucial.
Collaboration and Communication: Process validation executives work closely with cross-functional teams, regulatory agencies, and other stakeholders. Strong collaboration and communication skills are essential for effective coordination and achieving validation objectives.
Steps Involved in Process Validation
Process validation typically consists of three stages:
Stage 1: Process Design
In this stage, the process validation team defines the manufacturing process based on product requirements, quality attributes, and regulatory guidelines. The key activities include:
Process Characterization: Understanding the critical process parameters and their impact on product quality.
Process Development: Developing and optimizing the manufacturing process to meet the desired quality attributes.
Stage 2: Process Qualification
During this stage, the process validation team demonstrates that the manufacturing process is capable of consistently producing products within specified quality limits. The activities include:
Installation Qualification (IQ): Verifying that all equipment, utilities, and infrastructure are properly installed and meet the required specifications.
Operational Qualification (OQ): Ensuring that the manufacturing process performs as intended under normal operating conditions.
Performance Qualification (PQ): Validating the process using production-scale equipment and actual production materials to demonstrate consistent product quality.
Stage 3: Continued Process Verification
This stage involves ongoing monitoring and control of the manufacturing process to ensure its continued suitability for producing high-quality products. The activities include:
Process Monitoring: Collecting and analyzing process data to detect any trends, variations, or potential issues.
Statistical Process Control (SPC): Implementing statistical techniques to monitor and control process performance.
Change Control: Evaluating and managing changes to the validated process, ensuring that they do not adversely affect product quality or compliance.
Regulatory Requirements for Process Validation
Regulatory agencies such as the FDA (Food and Drug Administration) and EMA (European Medicines Agency) have specific requirements for process validation in industries such as pharmaceuticals, medical devices, and food manufacturing. These requirements aim to ensure product safety, efficacy, and quality. Compliance with regulatory guidelines is essential for market approval and maintaining a robust quality management system.
Documentation and Recordkeeping
Thorough documentation and recordkeeping are critical aspects of process validation. Key documents include validation protocols, standard operating procedures (SOPs), validation reports, and data analysis summaries. These documents provide a comprehensive record of the validation activities and serve as evidence of compliance with regulatory requirements.
Challenges in Process Validation
Process validation presents several challenges that process validation executives must address. These challenges include:
Complexity and Variability: Manufacturing processes can be complex, involving multiple variables and potential sources of variability. Capturing and controlling these variables can be challenging.
Interdisciplinary Collaboration: Process validation requires close collaboration between various departments, including manufacturing, quality assurance, regulatory affairs, and research and development. Effective communication and coordination among these departments can be a challenge.
Changing Regulatory Landscape: Regulatory requirements and guidelines are subject to change. Staying updated and ensuring compliance with evolving regulations can be demanding.
Resource Constraints: Process validation activities require dedicated resources, including personnel, equipment, and time. Resource constraints can impact the execution and timelines of validation projects.
Best Practices for Process Validation
To ensure successful process validation, consider the following best practices:
Early Engagement: Involve process validation experts and relevant stakeholders early in the product development lifecycle to ensure alignment with regulatory requirements.
Risk-Based Approach: Prioritize validation activities based on risk assessment, focusing on critical process parameters and quality attributes.
Documentation and Data Integrity: Establish robust documentation and data integrity practices, ensuring accurate and complete records of the validation process.
Continuous Monitoring and Improvement: Implement a robust process monitoring system to detect and address process variations promptly. Continuously seek opportunities for process improvement.
Future Trends in Process Validation
As technology advances and industries evolve, process validation is also undergoing changes. Some emerging trends in process validation include:
Data Analytics and AI: Leveraging advanced analytics and artificial intelligence to gain deeper insights from process data and improve process control.
Real-Time Monitoring: Implementing real-time monitoring systems to capture and analyze process data, enabling proactive identification and resolution of process deviations.
Process Validation Automation: Utilizing automation tools and technologies to streamline validation activities, improve efficiency, and reduce the validation lifecycle.
Process Analytical Technology (PAT): Integrating PAT tools and techniques to monitor and control critical process parameters in real-time, facilitating continuous process verification.
Process Validation Executive FAQs
1. What qualifications are required to become a process validation executive?
To become a process validation executive, a strong educational background in engineering or a relevant scientific discipline is typically required. Additionally, relevant industry experience, knowledge of regulatory guidelines, and strong analytical skills are beneficial.
2. What industries require process validation?
Process validation is essential in industries such as pharmaceuticals, medical devices, biotechnology, food and beverages, cosmetics, and chemical manufacturing. Any industry where product quality and regulatory compliance are critical can benefit from process validation.
3. How long does the process validation process typically take?
The duration of process validation can vary depending on factors such as the complexity of the manufacturing process, the number of validation stages, and the availability of resources. It can range from several weeks to several months or even longer.
4. What are some common challenges faced during process validation?
Common challenges include managing process variability, coordinating interdisciplinary teams, staying updated with changing regulatory requirements, and addressing resource constraints.
5. How does process validation contribute to patient safety?
Process validation ensures that manufacturing processes consistently produce products of desired quality. By minimizing variability and potential defects, process validation contributes to the safety and efficacy of products, thereby enhancing patient safety.