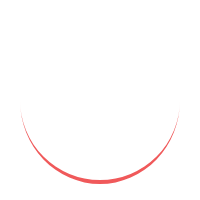
Shot blasting and grit blasting are two common methods used in industrial processes for surface preparation and cleaning. These techniques are widely employed in various industries such as automotive, construction, and aerospace. In this article, we will explore the fundamentals of shot blasting and grit blasting, their applications, benefits, and safety considerations.
Definition
Shot blasting is a surface treatment process that involves propelling abrasive particles, called shot, onto a surface at high velocities. The impact of the shot removes impurities, scales, rust, and old coatings, resulting in a clean and roughened surface.
Process
Shot blasting is performed using specialized equipment, typically consisting of a blast wheel that propels the shot and a chamber or cabinet where the blasting occurs. The blast wheel directs the abrasive particles towards the surface, creating a powerful cleaning and texturing action.
Equipment Used
Shot blasting machines can vary in size and complexity, ranging from small handheld units for localized applications to large automated systems for industrial-scale projects. The equipment may utilize different types of abrasive media, such as steel shot, grit, or cut wire shot, depending on the desired surface finish and the material being treated.
3. Benefits of Shot Blasting
Shot blasting offers several benefits in surface preparation and cleaning processes. Here are some key advantages:
Surface Preparation
Shot blasting effectively removes contaminants, old coatings, and surface impurities, creating a clean and roughened surface. This prepares the substrate for subsequent treatments, such as coating adhesion or bonding.
Coating Adhesion
By roughening the surface, shot blasting enhances the adhesion of coatings, paints, and adhesives. The increased surface area allows for better mechanical interlocking, resulting in improved durability and longevity of the applied coatings.
Rust and Corrosion Removal
Shot blasting efficiently removes rust, corrosion, and scale from metal surfaces. This helps to extend the lifespan of the treated materials and prevent further degradation.
4. Types of Shot Blasting Machines
There are different types of shot blasting machines available, each designed for specific applications and surface conditions. The main types include:
Wheel Blast Machines
Wheel blast machines are commonly used in large-scale industrial applications. They utilize a centrifugal wheel to propel the shot, providing high-speed impact and thorough cleaning of surfaces.
Air Blast Machines
Air blast machines use compressed air to propel the abrasive particles. They are versatile and suitable for various surface sizes and shapes. These machines are often used in smaller-scale operations and on-site projects.
Wet Blast Machines
Wet blast machines combine the use of abrasive media with water to provide a controlled and environmentally friendly cleaning process. They are particularly useful when dust suppression and precision surface cleaning are required.
5. Applications of Shot Blasting
Shot blasting finds applications in diverse industries. Some notable applications include:
Automotive Industry
In the automotive sector, shot blasting is employed for surface preparation of automotive parts, such as engine blocks, chassis components, and suspension parts. It helps to remove rust, scale, and old coatings, preparing the surfaces for painting or further treatment.
Construction Industry
Shot blasting is widely used in the construction industry for preparing concrete surfaces, such as floors and bridges. It removes contaminants, laitance, and weak concrete to provide a clean and roughened surface for effective bonding of coatings or overlays.
Aerospace Industry
In the aerospace industry, shot blasting is utilized for surface treatment of aircraft components, such as turbine blades, landing gears, and structural parts. It helps to remove corrosion, coatings, and imperfections, ensuring optimal performance and longevity.
6. Safety Measures in Shot Blasting
Safety is of utmost importance when performing shot blasting operations. Here are some key safety measures to consider:
Personal Protective Equipment (PPE)
Operators must wear appropriate PPE, including protective clothing, gloves, safety glasses, and respiratory protection, to safeguard against potential hazards, such as airborne abrasives and dust.
Ventilation and Dust Control
Proper ventilation and dust control systems should be in place to minimize the exposure to airborne particles and maintain a safe working environment. Local exhaust ventilation systems can effectively remove contaminants and maintain air quality.
Training and Education
Operators should receive comprehensive training on shot blasting techniques, equipment operation, and safety procedures. Regular updates and refresher training sessions are essential to ensure operators stay informed about the latest safety guidelines.
7. What is Grit Blasting?
Definition
Grit blasting, also known as abrasive blasting or sandblasting, is a surface treatment process that involves propelling abrasive particles, known as grit, onto a surface using compressed air. The impact of the grit removes surface contaminants, coatings, and imperfections.
Process
Grit blasting typically involves a blasting nozzle that directs the flow of compressed air and abrasive particles towards the surface being treated. The forceful impact of the particles results in the removal of unwanted materials and the creation of a clean and textured surface.
Abrasive Media Used
Various types of abrasive media can be used in grit blasting, including silica sand, aluminum oxide, glass beads, and steel grit. The selection of the abrasive media depends on the specific requirements of the application, such as desired surface finish and material compatibility.
8. Comparison between Shot Blasting and Grit Blasting
While shot blasting and grit blasting share similarities, they have distinct characteristics that make them suitable for different applications. Let's explore some key differences:
Differences in Abrasive Media
Shot blasting uses spherical or angular metallic particles, whereas grit blasting employs various abrasive materials, such as sand, aluminum oxide, or glass beads. The choice of abrasive media influences the surface finish and material removal capabilities.
Surface Finish
Shot blasting generally provides a rougher surface finish compared to grit blasting. The impact of the metallic shot particles creates deeper surface profiles, making it suitable for applications that require enhanced coating adhesion.
Material Removal
Grit blasting tends to have higher material removal rates compared to shot blasting. The harder and more aggressive abrasive media used in grit blasting can effectively remove thick coatings, stubborn rust, or heavy surface contaminants.
9. Common Applications of Grit Blasting
Grit blasting is widely used in various industries for surface preparation and cleaning. Some common applications include:
Surface Preparation for Coating
Grit blasting is employed to remove old coatings, rust, and surface contaminants before applying new coatings or protective layers. It ensures proper adhesion and longevity of the coatings.
Deburring and Deflashing
In manufacturing processes, grit blasting is used to remove burrs and flash from metal or plastic components. It helps to achieve precise and clean part surfaces for improved functionality and aesthetics.
Mold Cleaning
Grit blasting is utilized in mold cleaning processes to remove residues, release agents, and imperfections from molds. It ensures the production of high-quality and defect-free molded products.
10. Safety Considerations in Grit Blasting
Similar to shot blasting, grit blasting operations require adherence to safety measures to protect operators and ensure a safe working environment. Here are some key considerations:
PPE and Respiratory Protection
Operators must wear appropriate PPE, including protective clothing, gloves, safety glasses, and respiratory protection, to prevent inhalation of abrasive particles and protect against potential injuries.
Noise and Vibration Control
Grit blasting can generate significant noise and vibrations. Adequate measures, such as noise barriers and anti-vibration pads, should be implemented to minimize the impact on operators and surrounding areas.
Hazardous Waste Management
Proper management of the generated waste, including used abrasive media and removed contaminants, is essential. Strict adherence to waste disposal regulations and recycling practices helps minimize environmental impact.
12. Operator Shot Blasting and Grit Blasting FAQs
Q: Can shot blasting be used on delicate surfaces?
A: Shot blasting may not be suitable for delicate surfaces, as it can cause damage due to its abrasive nature. Alternative methods like wet blasting or specialized techniques should be considered.
Q: Is shot blasting a noisy process?
A: Shot blasting can generate significant noise levels. Proper hearing protection and noise control measures should be implemented to protect operators and maintain a safe work environment.
Q: What types of coatings can be applied after shot blasting?
A: Shot blasting prepares surfaces for a wide range of coatings, including paints, powder coatings, zinc-rich primers, and epoxy coatings, among others.
: How often should shot blasting equipment be maintained?
A: Regular maintenance is essential to ensure the proper functioning and longevity of shot blasting equipment. The frequency of maintenance depends on the usage and manufacturer's recommendations.
Q: Is grit blasting suitable for all materials?
A: Grit blasting can be used on various materials, including metals, concrete, stone, and composites. However, the choice of abrasive media should be compatible with the material being treated to avoid damage.