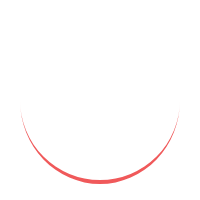
Operators in conventional surface grinding machines are skilled professionals responsible for the setup, operation, and maintenance of these machines. They work in close collaboration with other team members, such as machinists and engineers, to ensure the quality and precision of the finished products. An operator's primary objective is to effectively utilize the machine's capabilities to achieve the desired surface finish and dimensional accuracy.
Skills and Qualifications Required for an Operator
Becoming a proficient operator in surface grinding machines requires a combination of technical skills, knowledge, and experience. Here are some essential skills and qualifications for an operator:
1. Mechanical Aptitude: Operators must possess a solid understanding of the machine's mechanical components, including the grinding wheel, workpiece holding devices, and coolant systems.
2. Knowledge of Grinding Principles: Familiarity with grinding principles, such as the selection of grinding wheel grit, wheel dressing techniques, and material removal rates, is essential.
3. Blueprint Reading: The ability to read and interpret engineering drawings is crucial for understanding workpiece specifications and grinding requirements accurately.
4. Hand-eye Coordination: Operators should have excellent hand-eye coordination to precisely control the grinding process and achieve the desired surface finish.
5. Problem-solving Skills: Surface grinding may present challenges and issues during operation. Operators must possess problem-solving skills to troubleshoot and rectify any problems that may arise.
6. Safety Awareness: Operators must prioritize safety at all times. They should be well-versed in safety procedures, including the proper use of personal protective equipment (PPE) and handling of hazardous materials.
Safety Precautions for Operating Surface Grinding Machines
Operating surface grinding machines involves inherent risks, and operators must adhere to strict safety protocols. Here are some essential safety precautions to follow:
1. Use Appropriate PPE: Operators should wear safety goggles, gloves, ear protection, and respiratory masks when necessary to protect themselves from flying debris, noise, and airborne particles.
2. Machine Inspection: Before starting the machine, operators must inspect it for any damages or abnormalities. Check the wheel guard, grinding wheel, and coolant system for proper functioning.
3. Secure Workpieces: Ensure that workpieces are securely clamped or held in place using appropriate fixtures or magnetic chucks to prevent movement during grinding.
4. Set Up Proper Ventilation: Adequate ventilation is crucial to maintain a clean and safe working environment. Ensure that the grinding area is well-ventilated or use local exhaust ventilation systems.
5. Follow Lockout/Tagout Procedures: Before performing any maintenance or cleaning tasks, operators must follow lockout/tagout procedures to isolate the machine from its power source and prevent accidental startup.
Setting up the Machine
The initial setup of a surface grinding machine is critical to ensure accurate and consistent results. Here are the key steps involved in setting up the machine:
1. Machine Positioning: Position the machine on a level and stable surface. Ensure that it is properly aligned and anchored to prevent vibrations during operation.
2. Grinding Wheel Mounting: Install the appropriate grinding wheel on the machine's spindle, ensuring it is securely tightened and aligned with the workpiece.
3. Workpiece Preparation: Clean the workpiece surface and ensure it is free from any contaminants or burrs. Measure and mark the areas to be ground accurately.
4. Workholding Devices: Select and install the appropriate workholding devices, such as magnetic chucks or vices, to securely hold the workpiece in place during grinding.
Grinding Wheel Selection and Dressing
The selection of the grinding wheel and proper dressing techniques significantly impact the grinding process. Consider the following factors when selecting a grinding wheel:
1. Wheel Material: Choose the wheel material based on the type of workpiece material. Common wheel materials include aluminum oxide, silicon carbide, and cubic boron nitride (CBN).
2. Wheel Grit and Grade: The grit size determines the surface finish, while the wheel grade affects the wheel's hardness and self-sharpening properties. Select the appropriate grit and grade for the desired application.
3. Wheel Dressing: Regular dressing of the grinding wheel is necessary to maintain its sharpness and expose fresh abrasive particles. Dressing methods include single-point diamond dressing tools, rotary diamond dressers, and dressing sticks.
Operating Procedures for Surface Grinding
Once the machine is set up and the grinding wheel is properly dressed, operators can proceed with the grinding operation. Follow these steps for effective surface grinding:
1. Machine Warm-up: Allow the machine to warm up for a few minutes to reach its operating temper
2. Wheel Positioning: Position the grinding wheel slightly above the workpiece surface without making contact. Gradually bring the wheel into contact with the workpiece.
3. Grinding Parameters: Adjust the machine controls to set the desired grinding parameters, such as wheel speed, feed rate, and depth of cut. Follow the grinding sequence specified in the work instructions.
4. Coolant Application: Apply coolant to the grinding zone to control heat generation and flush away grinding swarf. Use the appropriate coolant type recommended for the specific application.
5. Grinding Process Monitoring: Continuously monitor the grinding process to ensure the desired surface finish and dimensional accuracy are achieved. Make any necessary adjustments as required.
Troubleshooting Common Issues
Surface grinding machines may encounter various issues during operation. Here are some common problems and troubleshooting tips:
1. Wheel Loading: If the grinding wheel becomes clogged with workpiece material, dress the wheel to expose fresh abrasive particles or increase the coolant flow to prevent wheel loading.
2. Wheel Glazing: Wheel glazing occurs when the abrasive grains become dull and ineffective. Dress the wheel or use a coarser-grit wheel to remove the glazing and regain cutting efficiency.
3. Chatter Marks: Chatter marks on the workpiece surface may result from machine vibrations or improper wheel balancing. Check and balance the grinding wheel or adjust machine settings to eliminate chatter.
Maintenance and Cleaning of Surface Grinding Machines
Regular maintenance and cleaning are crucial to keep surface grinding machines in optimal working condition. Follow these maintenance tips:
1. Daily Inspections: Conduct daily inspections of the machine, checking for any loose components, abnormal noises, or signs of wear. Address any issues promptly.
2. Lubrication: Ensure proper lubrication of the machine's moving parts, such as slideways and spindle bearings, according to the manufacturer's recommendations.
3. Grinding Wheel Maintenance: Periodically dress and true the grinding wheel to maintain its shape and cutting performance. Replace the wheel when it reaches its usable life.
4. Cleaning: Clean the machine thoroughly after each use, removing grinding swarf, coolant residues, and debris. Use appropriate cleaning agents and ensure the machine is dry before storage.
Advantages and Limitations of Conventional Surface Grinding Machines
Conventional surface grinding machines offer several advantages and limitations, which are important to consider:
Advantages:
Versatility: Surface grinding machines can process a wide range of materials and workpiece sizes, making them suitable for various industries.
Precision: These machines can achieve high levels of dimensional accuracy and surface finish, meeting tight tolerance requirements.
Cost-effective: Conventional surface grinding machines are often more affordable compared to automated alternatives, making them accessible to small and medium-sized businesses.
Limitations:
Manual Operation: Surface grinding machines require skilled operators to ensure optimal results, which can limit productivity and increase labor costs.
Setup Time: The initial setup and workpiece alignment can be time-consuming, especially for complex parts or frequent changeovers.
Limited Automation: Compared to automated grinding systems, conventional machines may have limited automation capabilities, leading to slower cycle times.
Emerging Trends in Surface Grinding Technology
Surface grinding technology is constantly evolving, incorporating new advancements to improve efficiency and productivity. Some emerging trends in surface grinding include:
CNC Integration: Increasing integration of computer numerical control (CNC) technology in surface grinding machines for enhanced precision and automation.
Advanced Grinding Wheels: Development of new abrasive materials and bonding technologies to improve cutting performance, reduce wheel wear, and enhance surface quality.
In-process Monitoring: Integration of sensor systems and real-time monitoring to optimize grinding parameters, detect anomalies, and ensure consistent quality.
Operator - Conventional Surface Grinding Machines FAQs
Q1: What are the primary responsibilities of an operator in surface grinding machines?
An operator's responsibilities include machine setup, operation, maintenance, troubleshooting, and ensuring the quality of finished products.
Q2: Can anyone become a surface grinding machine operator?
Becoming a proficient operator requires a combination of skills, knowledge, and experience. Training programs and apprenticeships can help individuals develop the necessary expertise.
Q3: How important is safety in surface grinding operations?
Safety is paramount in surface grinding operations. Operators must follow safety protocols, use appropriate personal protective equipment, and be aware of potential hazards.
Q4: What are some common issues faced during surface grinding?
Common issues include wheel loading, wheel glazing, and chatter marks. Troubleshooting techniques involve wheel dressing, adjustment of machine settings, and proper maintenance.
Q5: Are there any automated alternatives to conventional surface grinding machines?
Yes, automated grinding systems, such as CNC surface grinders, offer increased automation and precision. However, they may be costlier and require programming expertise.