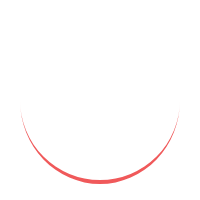
MIG welding is a welding technique that employs a consumable wire electrode and a shielding gas to create an electric arc between the electrode and the workpiece. The shielding gas, typically a mixture of argon, carbon dioxide, and other gases, prevents atmospheric contamination during the welding process. The wire electrode serves as both the heat source and filler material, melting and fusing the base metals together.
Advantages of MIG Welding
MIG welding offers several advantages that make it a popular choice in various industries. Firstly, it allows for high welding speeds and increased productivity due to its continuous wire feed mechanism. Secondly, MIG welding provides excellent control over the weld, resulting in high-quality and aesthetically pleasing welds. Additionally, it can be used on a wide range of metals, including carbon steel, stainless steel, aluminum, and more. MIG welding also requires minimal post-weld cleaning and produces little to no slag.
Equipment and Materials for MIG Welding
To perform MIG welding, several key pieces of equipment and materials are required. These include a welding power supply, a MIG welding gun, a wire feeder, a shielding gas cylinder, a welding table or workbench, safety gear such as gloves and a welding helmet, and the consumable wire electrode. The choice of electrode and shielding gas depends on the type of metal being welded and the desired welding characteristics.
Metal Inert Gas Welding The MIG Welding Process
MIG welding involves several steps to create a strong and durable weld. Firstly, the welding machine is set up and adjusted according to the metal type and thickness. The workpiece is prepared by cleaning any contaminants or rust. The welding gun is positioned at the desired starting point, and the arc is initiated by pulling the trigger. The welder then manipulates the welding gun along the joint, ensuring proper wire feed and shielding gas flow. Once the welding is complete, the weld bead is inspected for quality.
Common Applications of MIG Welding
MIG welding finds applications in various industries and projects. It is commonly used in automotive manufacturing and repair, fabrication of structural steel, pipe welding, aerospace industry, shipbuilding, and general metal fabrication. The versatility of MIG welding makes it a go-to choice for both industrial and DIY welding projects.
Safety Measures for MIG Welding
Safety is paramount when engaging in any welding activity, including MIG welding. Adequate ventilation, proper eye protection, and suitable protective clothing are essential. It is crucial to be aware of electrical hazards, fire risks, and the potential dangers of inhaling welding fumes. Adhering to safety guidelines and receiving proper training significantly reduces the risks associated with MIG welding.
Troubleshooting in MIG Welding
Like any welding process, MIG welding can encounter various issues that may affect the quality of the weld. Some common troubleshooting areas include wire feed problems, insufficient gas coverage, porosity, and spatter. Understanding these issues and their solutions can help welders overcome challenges and achieve better results.
Maintenance and Care for MIG Welding Equipment
Regular maintenance and care of MIG welding equipment are crucial for optimal performance and longevity. This includes cleaning and inspecting the welding gun, replacing worn-out parts, checking the gas supply, and ensuring proper wire storage. By maintaining the equipment in good condition, welders can avoid unnecessary downtime and ensure consistent weld quality.
Comparing MIG Welding with Other Welding Methods
MIG welding offers distinct advantages and disadvantages compared to other welding methods. When compared to Stick welding, MIG welding provides faster deposition rates and cleaner welds but may require a higher skill level. In contrast, TIG welding offers superior precision and control but is generally slower and more intricate. Understanding the strengths and limitations of each welding method helps in choosing the most suitable technique for specific applications.
Tips for Successful MIG Welding
To achieve successful MIG welding results, several tips can be followed. Ensuring proper grounding, maintaining the right gun angle and travel speed, selecting the appropriate wire diameter, and adjusting voltage and wire feed settings are some key considerations. Additionally, practicing on scrap pieces, experimenting with different techniques, and seeking guidance from experienced welders can contribute to improving MIG welding skills.
Environmental Impact of MIG Welding
While MIG welding is an efficient and versatile welding method, it is essential to consider its environmental impact. The process generates emissions, including welding fumes and greenhouse gases from shielding gases. Employing proper ventilation systems, utilizing efficient gas mixtures, and practicing responsible waste management can help mitigate the environmental footprint of MIG welding.
Future Trends in MIG Welding
As technology continues to advance, the field of welding is constantly evolving. Some future trends in MIG welding include the development of more advanced welding machines with enhanced automation features, the use of alternative shielding gases for improved environmental performance, and the integration of artificial intelligence for real-time welding process monitoring and control. These advancements aim to further streamline the welding process, enhance productivity, and improve overall weld quality.
Metal Inert Gas Welding FAQs
Q1. Is MIG welding suitable for aluminum?
Yes, MIG welding is commonly used for aluminum welding. However, it requires the use of a specialized aluminum wire and an appropriate shielding gas, such as pure argon or an argon-helium mix.
Q2. Can MIG welding be used outdoors?
MIG welding can be performed outdoors, but certain precautions need to be taken. Wind can affect the shielding gas coverage, so it's important to position the weld in a sheltered area or use windshields to protect the weld from gusts.
Q3. What is the difference between MIG welding and Flux-Cored Arc Welding (FCAW)?
While both MIG welding and Flux-Cored Arc Welding (FCAW) use similar equipment, the key difference lies in the electrode. MIG welding utilizes a solid wire electrode, whereas FCAW employs a tubular wire electrode filled with flux, which provides its own shielding.
Q4. Can MIG welding be used for thin metals?
Yes, MIG welding can be used for thin metals. By adjusting the settings, such as reducing wire feed speed and voltage, and using a smaller diameter wire, welders can achieve successful welds on thin materials.
Q5. How do I choose the right shielding gas for MIG welding?
The choice of shielding gas depends on the metal being welded. Generally, a mixture of argon and carbon dioxide is suitable for carbon steel, while pure argon or an argon-helium mix is preferred for aluminum welding. Consulting with welding suppliers or experts can help in selecting the appropriate shielding gas for specific applications.