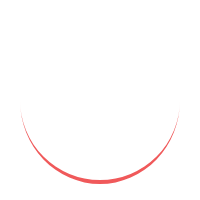
In today's fast-paced business environment, efficient material coordination is crucial for the smooth functioning of any organization. A Material Coordination Manager plays a pivotal role in managing the flow of materials and ensuring their timely availability. In this article, we will explore the responsibilities, skills required, challenges faced, and strategies employed by Material Coordination Managers to optimize material coordination processes.
Introduction to the role of a Material Coordination Manager
The role of a Material Coordination Manager is to oversee and manage the entire lifecycle of materials, from procurement to delivery. They are responsible for maintaining an optimal inventory level, coordinating with suppliers, and ensuring the timely availability of materials required for production or operations. A Material Coordination Manager acts as a bridge between various departments, suppliers, and vendors, ensuring a seamless flow of materials throughout the supply chain.
Responsibilities of a Material Coordination Manager
One of the primary responsibilities of a Material Coordination Manager is to manage inventory levels effectively. This includes analyzing demand patterns, forecasting future requirements, and maintaining a balance between carrying costs and stock availability. They work closely with procurement teams to ensure timely procurement of materials based on the organization's needs.
Coordinating with suppliers and vendors
Material Coordination Managers act as the main point of contact for suppliers and vendors. They establish and maintain strong relationships to ensure the timely delivery of materials as per the agreed-upon terms. Effective communication and negotiation skills are essential for managing contracts, resolving issues, and optimizing supplier performance.
Ensuring timely delivery of materials
Meeting production schedules and customer demands requires Material Coordination Managers to ensure the timely delivery of materials. They track shipments, monitor transportation logistics, and collaborate with logistics teams to minimize delays and disruptions. Timely material availability helps organizations avoid production bottlenecks and maintain high customer satisfaction levels.
Optimizing inventory levels
Maintaining optimal inventory levels is crucial for cost control and efficient operations. Material Coordination Managers analyze demand trends, consumption patterns, and lead times to optimize inventory levels. They implement strategies such as just-in-time inventory management, safety stock calculations, and reorder point optimization to strike a balance between inventory carrying costs and operational efficiency.
Implementing cost-saving measures
Material Coordination Managers continuously look for opportunities to reduce costs and improve efficiency. They identify areas for cost savings through negotiation with suppliers, bulk purchasing, process improvements, and value engineering. Their goal is to streamline material coordination processes while maintaining quality and ensuring timely availability.
Skills and qualifications required for the role
To excel as a Material Coordination Manager, certain skills and qualifications are essential. These include:
Strong organizational and multitasking abilities: Material Coordination Managers need to juggle multiple tasks, prioritize effectively, and handle complex logistics. Excellent organizational and multitasking skills are vital for success in this role.
Excellent communication and negotiation skills: Effective communication with suppliers, vendors, and internal stakeholders is crucial. Material Coordination Managers must be able to articulate requirements, resolve conflicts, and negotiate favorable terms.
Knowledge of supply chain management: A solid understanding of supply chain management principles, including demand forecasting, procurement, logistics, and inventory management, is necessary to optimize material coordination processes.
Proficiency in inventory management software: Material Coordination Managers should be proficient in using inventory management software to track inventory levels, analyze data, and generate reports for informed decision-making.
Importance of effective material coordination in business operations
Efficient material coordination plays a vital role in ensuring smooth business operations. Let's explore the key reasons why effective material coordination is essential:
Minimizing disruptions in production
Timely availability of materials is critical to meeting production schedules. Effective material coordination ensures that the right materials are available at the right time, minimizing production disruptions and reducing the risk of idle machinery or delayed deliveries.
Reducing inventory carrying costs
Optimizing inventory levels is key to minimizing carrying costs. Efficient material coordination helps strike a balance between inventory availability and costs associated with holding excess stock. By avoiding overstocking and reducing obsolete inventory, organizations can free up capital for other critical investments.
Ensuring customer satisfaction
Delivering products or services on time is crucial for maintaining customer satisfaction. Effective material coordination ensures that customer orders can be fulfilled promptly, meeting their expectations and building long-term relationships. Satisfied customers are more likely to become loyal and provide positive referrals.
Enhancing overall operational efficiency
Efficient material coordination streamlines business operations, leading to improved overall efficiency. By optimizing inventory levels, reducing lead times, and minimizing disruptions, organizations can enhance their productivity, reduce waste, and achieve cost savings. This ultimately contributes to their competitive advantage in the market.
Challenges faced by Material Coordination Managers
Material Coordination Managers encounter several challenges in their role. Let's explore some common challenges and how they can be addressed:
Dealing with supply chain disruptions
Unforeseen events such as natural disasters, transportation disruptions, or supplier issues can cause supply chain disruptions. Material Coordination Managers must have contingency plans in place to mitigate such risks, identify alternative suppliers, and maintain buffer stocks to minimize the impact of disruptions.
Managing demand fluctuations
Fluctuating customer demands can pose challenges for material coordination. Material Coordination Managers should closely monitor demand patterns, collaborate with sales and production teams to forecast accurately, and establish flexible supply agreements to accommodate demand fluctuations effectively.
Balancing cost and quality considerations
Material Coordination Managers often face the challenge of balancing cost and quality considerations. While cost optimization is important, compromising on quality can lead to customer dissatisfaction or production issues. Striking the right balance involves evaluating supplier performance, conducting quality audits, and maintaining clear quality standards.
Handling cross-functional coordination
Material coordination involves collaboration with multiple departments, including procurement, production, logistics, and quality assurance. Material Coordination Managers need to foster effective cross-functional communication, establish clear processes, and build strong relationships to ensure seamless coordination across different functions.
Strategies for effective material coordination
To overcome the challenges and optimize material coordination, Material Coordination Managers can employ the following strategies:
Forecasting and demand planning
Accurate demand forecasting is essential for effective material coordination. Material Coordination Managers should analyze historical data, market trends, and customer insights to forecast demand accurately. This helps in aligning procurement and inventory levels with expected requirements, reducing the risk of excess or insufficient inventory.
Building strong supplier relationships
Strong relationships with suppliers are crucial for ensuring timely and reliable material deliveries. Material Coordination Managers should establish open lines of communication, negotiate mutually beneficial contracts, and collaborate closely with suppliers to understand their capabilities and constraints. This helps in building trust, resolving issues promptly, and maintaining a reliable supply chain.
Implementing lean inventory management techniques
Applying lean principles to inventory management can improve material coordination efficiency. Material Coordination Managers should focus on reducing waste, implementing just-in-time practices, and optimizing reorder points based on demand patterns. By eliminating excess inventory, organizations can minimize carrying costs and enhance operational efficiency.
Utilizing technology for automation
Leveraging technology can significantly enhance material coordination processes. Material Coordination Managers should explore inventory management software, supply chain analytics tools, and automation solutions. These technologies can streamline data analysis, provide real-time visibility into inventory levels, and automate routine tasks, enabling Material Coordination Managers to focus on strategic decision-making.
Case studies and examples highlighting successful material coordination practices
To understand the practical application of effective material coordination, let's explore a few case studies and examples:
Company X: By implementing demand planning software and collaborating closely with key suppliers, Company X reduced their inventory carrying costs by 20% while ensuring timely availability of materials, leading to improved customer satisfaction.
Company Y: By adopting lean inventory management techniques and establishing strategic partnerships with suppliers, Company Y achieved a 30% reduction in lead times, resulting in streamlined operations and increased productivity.
Company Z: Through the integration of advanced analytics and AI-driven demand forecasting, Company Z accurately predicted demand fluctuations and optimized their inventory levels. This allowed them to achieve a 15% reduction in inventory costs while meeting customer demands consistently.
Future trends in material coordination
The field of material coordination is continuously evolving. Here are some future trends that Material Coordination Managers should watch out for:
Integration of AI and machine learning
Artificial intelligence (AI) and machine learning (ML) technologies have the potential to revolutionize material coordination. AI-powered demand forecasting models, predictive analytics, and intelligent automation can enhance accuracy, optimize inventory levels, and enable proactive decision-making.
Sustainable sourcing and green supply chain initiatives
As sustainability becomes a top priority for businesses, Material Coordination Managers will play a crucial role in implementing sustainable sourcing practices and green supply chain initiatives. This includes identifying eco-friendly suppliers, reducing waste generation, and promoting recycling and reuse of materials.
Digital transformation in inventory management
Digital transformation will continue to reshape inventory management practices. Cloud-based inventory management systems, IoT-enabled sensors for real-time tracking, and blockchain-based supply chain platforms will provide enhanced visibility, transparency, and efficiency in material coordination processes.
Material Coordination Manager FAQs
Q: What qualifications are required to become a Material Coordination Manager?
A: A bachelor's degree in supply chain management, logistics, or a related field is often preferred. Additionally, relevant work experience and certifications in inventory management or supply chain are beneficial.
Q: How can Material Coordination Managers handle disruptions in the supply chain?
A: Material Coordination Managers should have contingency plans, alternative suppliers, and buffer stocks in place to mitigate the impact of disruptions. Effective communication and proactive monitoring of supply chain risks are key.
Q: What role does technology play in material coordination?
A: Technology, such as inventory management software and supply chain analytics tools, helps Material Coordination Managers streamline processes, gain real-time visibility, and make data-driven decisions for efficient material coordination.
Q: How can Material Coordination Managers balance cost and quality considerations?
A: By closely monitoring supplier performance, conducting quality audits, and maintaining clear quality standards, Material Coordination Managers can strike a balance between cost optimization and ensuring high-quality materials.
Q: What are some best practices for lean inventory management?
A: Best practices include implementing just-in-time practices, optimizing reorder points based on demand patterns, and eliminating waste through continuous process improvement efforts.