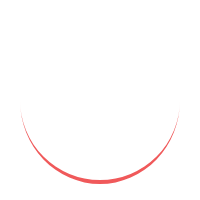
Metal testing is a crucial aspect of various industries where the quality, integrity, and safety of metal components and structures are of paramount importance. From manufacturing to construction, aerospace to automotive, and beyond, metal testing plays a vital role in ensuring the reliability and performance of metallic materials. In this article, we will explore the world of metal testing, the role of a lab technician, the techniques involved, and the career opportunities in this field.
What is Metal Testing?
Metal testing, as the name suggests, is the process of evaluating and analyzing the properties, composition, and behavior of metals. It involves a comprehensive assessment of metallic materials to determine their suitability for specific applications. The testing procedures are designed to identify any defects, weaknesses, or deviations from desired standards. By conducting various tests and examinations, lab technicians can provide valuable insights into the quality, performance, and safety aspects of metals.
Importance of Metal Testing
Metal testing holds immense significance across different industries due to the following reasons:
Ensuring Quality and Safety
Metal components are often subjected to extreme conditions, such as high temperatures, pressure, and mechanical stress. Quality testing ensures that the metals used in critical applications meet the required standards and can withstand these challenging environments. It helps prevent potential failures, malfunctions, and accidents.
Compliance with Standards and Regulations
Various international and industry-specific standards govern the use of metals in different applications. Metal testing ensures that the materials meet these standards and comply with relevant regulations. Compliance is crucial to maintain the integrity of structures, promote safety, and meet legal requirements.
Preventing Failures and Accidents
Failure of metal components can have severe consequences, leading to financial losses, injuries, and even loss of life. By conducting rigorous tests, technicians can identify potential weaknesses, flaws, or manufacturing defects in metals, enabling timely intervention and preventing catastrophic failures.
Types of Metal Testing
Metal testing encompasses a range of techniques and methods. Some common types of metal testing include:
Chemical Analysis
Chemical analysis involves determining the elemental composition and impurity levels in metals. Techniques like spectroscopy and mass spectrometry are used to identify and quantify the elements present in a sample. This analysis helps ensure the desired composition and purity of the metal.
Mechanical Testing
Mechanical testing evaluates the mechanical properties of metals, such as strength, hardness, ductility, and toughness. Tensile testing, compression testing, and impact testing are some commonly employed techniques to assess these properties. This information is crucial for designing and manufacturing metal components.
Non-Destructive Testing
Non-destructive testing (NDT) methods are used to evaluate the integrity and quality of metals without causing any damage to the tested samples. Techniques like ultrasonic testing, radiography, eddy current testing, and magnetic particle testing are employed to detect flaws, cracks, or hidden defects in the metal.
Corrosion Testing
Corrosion testing is performed to assess the susceptibility of metals to corrosion. It helps determine the corrosion resistance, pitting potential, and overall durability of metal structures. Various accelerated corrosion tests and electrochemical methods are utilized for this purpose.
Microstructure Analysis
Microstructure analysis involves examining the microscopic structure and grain boundaries of metals. Metallography, microscopy, and electron microscopy techniques are utilized to understand the material's microstructural features. This analysis provides insights into the metal's properties, such as grain size, phase distribution, and crystallographic defects.
Laboratory Equipment and Techniques
Metal testing requires specialized equipment and techniques to carry out accurate assessments. Some commonly used laboratory equipment and techniques include:
Spectroscopy
Spectroscopy techniques, such as optical emission spectroscopy (OES) and X-ray fluorescence (XRF), are employed for chemical analysis. These methods use the characteristic spectral lines emitted by elements to determine their presence and concentration in the metal.
Tensile Testing
Tensile testing measures the resistance of a metal sample to a stretching force. It helps determine the yield strength, ultimate tensile strength, and elongation properties of the metal. This information is crucial for assessing the material's mechanical behavior and suitability for specific applications.
Ultrasonic Testing
Ultrasonic testing uses high-frequency sound waves to detect internal flaws, cracks, or defects in metals. The technique relies on the principle of sound wave reflection and attenuation to generate images of the metal's internal structure. It is widely used for flaw detection, thickness measurement, and weld inspection.
Hardness Testing
Hardness testing assesses a metal's resistance to indentation or scratching. Different hardness testing methods, such as Brinell, Rockwell, and Vickers, are employed to measure the metal's hardness properties. Hardness testing helps evaluate material strength and wear resistance.
Metallography
Metallography involves preparing metal samples, grinding, polishing, and etching them to reveal their microstructure under a microscope. This technique helps identify various structural features, including grain boundaries, phases, inclusions, and defects. Metallography aids in understanding the material's properties and identifying any manufacturing or processing issues.
Role of a Lab Technician in Metal Testing
Lab technicians play a crucial role in metal testing. They are responsible for performing tests, conducting analyses, and interpreting the results. A lab technician follows established procedures and protocols to ensure accurate and reliable testing. They operate and maintain laboratory equipment, prepare samples, record data, and collaborate with engineers and scientists to deliver comprehensive testing reports.
Skills and Qualifications Required
To excel as a lab technician in metal testing, certain skills and qualifications are essential:
Strong knowledge of metallurgy and materials science
Proficiency in using laboratory equipment and techniques
Attention to detail and ability to follow protocols
Analytical and problem-solving skills
Good communication and teamwork abilities
Understanding of safety procedures and regulations
Familiarity with relevant testing standards and methods
Continuous learning and staying updated with advancements in the field
Steps Involved in Metal Testing
Metal testing typically involves several steps to ensure accurate results:
Sample Preparation
The first step is to collect representative samples from the metal components or structures. These samples need proper preparation, including cutting, grinding, polishing, and cleaning, to remove any contaminants or surface layers that may affect the test results.
Test Execution
Once the samples are prepared, the lab technician performs the desired tests according to the testing requirements. This may involve chemical analysis, mechanical testing, NDT methods, or microstructure analysis, depending on the specific objectives of the testing process.
Data Analysis and Interpretation
After conducting the tests, the lab technician analyzes the obtained data, compares it with the applicable standards or specifications, and interprets the results. This interpretation helps assess the quality, integrity, and suitability of the tested metal.
Challenges in Metal Testing
Metal testing can present several challenges that need to be addressed to ensure accurate and reliable results:
Contamination
Contamination of samples or testing equipment can introduce errors or inaccuracies in the test results. Proper precautions and cleaning procedures must be followed to minimize contamination risks during sample preparation and testing.
Sample Size and Representation
The size and representativeness of the sample can significantly impact the accuracy and reliability of the test results. Care must be taken to select appropriate sample sizes and ensure they adequately represent the overall characteristics of the metal.
Interpretation of Results
Interpreting test results requires expertise and knowledge of the specific testing methods and standards. Different factors, such as variability, tolerances, and permissible limits, need to be considered while interpreting the results accurately.
Future Trends in Metal Testing
Metal testing is a dynamic field that continues to evolve with technological advancements. Some future trends shaping the industry include:
Advancements in Technology
New technologies and instruments are being developed to enhance the accuracy, speed, and efficiency of metal testing. These include portable and handheld devices, advanced spectroscopy techniques, and automated testing systems.
Automation and Robotics
Automation is being increasingly adopted in metal testing laboratories to streamline processes, reduce human errors, and improve productivity. Robotic systems can perform repetitive tasks, sample handling, and even execute complex testing procedures.
Integration of AI and Machine Learning
AI and machine learning algorithms are being integrated into metal testing to analyze vast amounts of data, identify patterns, and predict material behavior. This enables quicker decision-making and enhances the understanding of material properties.
Career Opportunities in Metal Testing
A career in metal testing offers diverse opportunities in different industries. Some common job roles include:
Quality Control Technician
Quality control technicians ensure that metals and metal components meet the required standards and specifications. They perform various tests, inspections, and evaluations to assess the quality and integrity of the materials.
Materials Engineer
Materials engineers specialize in developing and testing new metal alloys, improving material properties, and ensuring optimal performance in specific applications. They work closely with lab technicians to conduct experiments and analyze data.
Research and Development Scientist
Research and development scientists explore innovative testing techniques, develop new testing methods, and conduct research to improve the understanding of metal behavior and properties.
Lab Technician - Metal Testing Frequently Asked Questions
What industries require metal testing?
Metal testing is essential in industries such as manufacturing, construction, automotive, aerospace, energy, and many more, where the quality and reliability of metal components are crucial.
How long does it take to become a lab technician?
The duration to become a lab technician in metal testing varies depending on the educational path chosen. It typically takes around two to four years to obtain a relevant degree or certification.
Can metal testing detect defects and flaws?
Yes, metal testing techniques like non-destructive testing can detect defects, flaws, and hidden imperfections in metals without causing any damage to the tested samples.
What are the potential risks in metal testing?
Potential risks in metal testing include exposure to hazardous materials, contamination of samples, and the incorrect interpretation of test results. Following safety protocols and quality assurance measures helps mitigate these risks.
How can I pursue a career in metal testing?
To pursue a career in metal testing, you can consider obtaining a degree or certification in metallurgy, materials science, or a related field. Gaining practical experience through internships or entry-level positions in testing laboratories can also be beneficial.