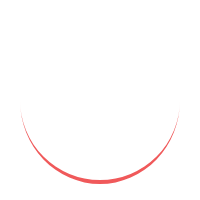
An electrical assembly operator plays a crucial role in the manufacturing and assembly of control panels for various electrical systems. Control panels serve as the nerve center of electrical setups, enabling efficient and safe operation. In this article, we will delve into the responsibilities, skills, and procedures involved in the role of an electrical assembly operator in control panel manufacturing.
Electrical assembly operators are skilled professionals who specialize in the assembly, installation, and maintenance of control panels used in electrical systems. These control panels house a range of components, including switches, relays, circuit breakers, and indicators, allowing operators to control and monitor the electrical system.
The primary role of an electrical assembly operator is to assemble, wire, and test control panels based on engineering specifications and electrical diagrams. They work closely with electrical engineers and technicians to ensure the panels meet the required standards and functionality. Additionally, electrical assembly operators may also be involved in troubleshooting and repairing control panels.
Control panels are vital in electrical systems as they provide a centralized interface for monitoring and controlling electrical equipment. These panels help regulate power distribution, manage various electrical functions, and ensure the safety of the system and its users. Without control panels, managing complex electrical systems would be impractical and unsafe.
As an electrical assembly operator, there are several key responsibilities to fulfill. These include interpreting electrical schematics and diagrams, selecting and installing appropriate components, wiring the control panel, performing quality checks, and adhering to safety protocols. Operators must also ensure the final product meets industry standards and customer requirements.
To excel as an electrical assembly operator, certain skills and qualifications are essential. These include a solid understanding of electrical systems and components, proficiency in reading electrical diagrams and blueprints, knowledge of wiring techniques, and familiarity with industry regulations and safety standards. Attention to detail, manual dexterity, and problem-solving skills are also crucial in this role.
Safety is paramount in the field of electrical assembly. Operators must follow strict safety measures and protocols to prevent accidents and injuries. These include wearing appropriate personal protective equipment (PPE), ensuring proper grounding and insulation, using lockout/tagout procedures, and being mindful of electrical hazards. Regular safety training and staying updated with industry standards are essential for all electrical assembly operators.
Control panel assembly requires the use of various tools and equipment. These may include wire strippers, crimping tools, screwdrivers, pliers, multimeters, and wire labeling devices. Additionally, power drills, saws, and other equipment may be necessary for panel enclosure assembly. Familiarity with these tools and their proper usage is vital for efficient and accurate control panel assembly.
To assemble a control panel, follow these step-by-step guidelines:
Step 1: Gather Materials and Components
Ensure you have all the necessary materials and components required for the control panel assembly. This includes the panel enclosure, electrical components, wires, labels, and any specific tools or equipment.
Step 2: Review Electrical Diagrams and Specifications
Carefully study the electrical diagrams and specifications provided. Understand the layout, connections, and functionality of the control panel based on these documents.
Step 3: Mount Components in the Panel Enclosure
Begin by mounting the components inside the panel enclosure according to the electrical diagrams. Secure them in their designated positions using appropriate screws or fasteners.
Step 4: Wire the Control Panel
Start the wiring process by routing the necessary wires from the components to their respective terminal points. Ensure proper labeling of wires for easy identification. Use wire strippers to remove insulation and connect wires securely.
Step 5: Follow Wiring Standards and Codes
Adhere to wiring standards and codes specific to your industry and location. Pay attention to proper wire sizing, color coding, grounding, and isolation to ensure a safe and compliant assembly.
Step 6: Perform Quality Checks
After completing the wiring, perform thorough quality checks. Inspect each connection, verify wire routing accuracy, and ensure all components are securely mounted. Use a multimeter to test for continuity, voltage, and resistance where necessary.
Step 7: Test Control Panel Functionality
Connect the control panel to a power source and test its functionality. Verify that switches, relays, indicators, and other components are working as intended. Test control panel responses to different input signals or scenarios.
Step 8: Document and Label the Control Panel
Properly document the assembly process, including wiring diagrams, component lists, and any modifications made. Label all wires, components, and terminal points clearly for ease of maintenance and troubleshooting.
Step 9: Final Inspection and Approval
Once the control panel assembly passes all quality and functionality tests, it is ready for a final inspection. Ensure compliance with industry standards, customer specifications, and safety regulations before seeking approval for the finished panel.
9. Testing and Quality Assurance Procedures
Testing and quality assurance are integral to the control panel assembly process. Here are some common procedures:
Functional Testing: Verify the functionality of each component and the control panel as a whole. Test switches, relays, indicators, and other devices to ensure they respond correctly to input signals.
Continuity Testing: Use a multimeter to check for proper continuity of wiring connections. This ensures that electrical signals can flow freely without interruption.
Voltage Testing: Measure voltage levels at different points in the control panel to ensure they are within the specified range. This helps identify any voltage irregularities or potential issues.
Insulation Resistance Testing: Test the insulation resistance of the control panel to ensure electrical safety. Insulation resistance measurements help detect any leaks or faults in the insulation materials.
Environmental Testing: Subject the control panel to environmental conditions it may encounter during operation, such as temperature, humidity, and vibration. This testing ensures the panel can withstand and function reliably in various environments.
Documentation and Traceability: Document all test results and quality assurance procedures for future reference. Maintain a traceable record of the testing process and any modifications made during assembly.
10. Troubleshooting Common Issues in Control Panels
Even with careful assembly and testing, control panels may encounter issues. Here are some common problems and troubleshooting steps:
Faulty Connections: Check for loose or poorly connected wires, terminals, or connectors. Ensure all connections are secure and properly tightened.
Short Circuits: Inspect for any wire insulation damage or components in close proximity that may be causing a short circuit. Isolate and repair the affected area to prevent further issues.
Component Failure: If a specific component is not functioning as expected, verify its connections and wiring. If the component is found to be defective, replace it with a new one and ensure proper installation.
Overheating: Monitor the temperature inside the control panel. Excessive heat can indicate overloaded circuits or inadequate ventilation. Ensure proper airflow and consider redistributing loads or upgrading components if necessary.
Tripped Circuit Breakers: If a circuit breaker trips repeatedly, investigate the cause. Check for overloaded circuits, short circuits, or faulty equipment that may be causing the excessive current. Rectify the issue and reset the breaker.
Inconsistent or Erratic Behavior: If the control panel exhibits inconsistent or erratic behavior, review the wiring, connections, and programming. Look for any loose or damaged wires, faulty sensors, or incorrect programming settings.
Faulty Indicators or Displays: If indicators or displays are not functioning correctly, check their connections and power supply. Replace faulty indicators or displays as needed.
Intermittent Issues: Intermittent issues can be challenging to diagnose. Carefully inspect all connections and wiring for any signs of damage or loose connections. Conduct thorough testing to reproduce the issue and narrow down the root cause.
Remember, if you encounter complex or persistent issues with a control panel, consult with experienced technicians or engineers to ensure proper troubleshooting and resolution.
1. What qualifications are required to become an electrical assembly operator for control panels?
To become an electrical assembly operator for control panels, a high school diploma or equivalent is typically required. Additional vocational training or certification in electrical systems or panel assembly can be beneficial. Strong knowledge of electrical components, wiring techniques, and safety regulations is essential.
2. Are there any specific skills needed for this role?
Yes, some essential skills for an electrical assembly operator include a good understanding of electrical systems, the ability to read and interpret electrical diagrams, proficiency in wiring and assembling components, attention to detail, problem-solving skills, and adherence to safety protocols. Manual dexterity and the ability to use various tools and equipment are also important.
3. What safety precautions should electrical assembly operators follow?
Electrical assembly operators must prioritize safety. They should wear appropriate personal protective equipment (PPE) such as gloves, safety glasses, and protective clothing. Adhering to proper grounding and insulation techniques, following lockout/tagout procedures, and staying updated with safety training are crucial. Operators should also be aware of electrical hazards and follow industry safety standards.
4. How can I troubleshoot common issues in control panels?
When troubleshooting control panels, start by checking for loose or faulty connections, damaged wires, and short circuits. Verify proper insulation, component functionality, and programming settings. Utilize testing equipment like multimeters to measure continuity, voltage, and resistance. If complex issues persist, consult experienced technicians or engineers for assistance.
5. What are the career prospects for electrical assembly operators in the control panel industry?
Electrical assembly operators are in demand in industries such as manufacturing, automation, energy, and construction. With advancements in technology and increased emphasis on efficient electrical systems, the demand for skilled operators is expected to grow. Career advancement opportunities may include supervisory roles, specialization in specific control panel types, or transitioning into engineering or project management positions.