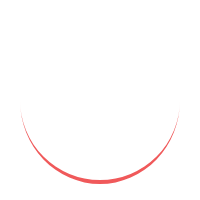
An assembly supervisor plays a crucial role in the manufacturing industry by overseeing the operations of the assembly line and ensuring the smooth production of goods. This article will explore the responsibilities of an assembly supervisor, the skills and qualifications required for the role, the steps to become an assembly supervisor, the challenges they face, and the future prospects and trends in this field.
Managing assembly line operations
One of the primary responsibilities of an assembly supervisor is to manage the day-to-day operations of the assembly line. This includes coordinating with various departments, scheduling tasks, and ensuring that production targets are met within the given time frame. The assembly supervisor must have a comprehensive understanding of the assembly process and be able to optimize it for maximum efficiency.
Ensuring quality control
Maintaining quality control is crucial in the manufacturing industry, and the assembly supervisor plays a key role in this aspect. They are responsible for implementing quality assurance measures, conducting regular inspections, and ensuring that all products meet the required standards. This involves monitoring the assembly line closely, identifying any defects or issues, and taking appropriate actions to rectify them.
Training and supervising assembly line workers
Another important aspect of the assembly supervisor's role is to train and supervise the assembly line workers. They are responsible for ensuring that the workers have the necessary skills and knowledge to perform their tasks effectively. This includes providing training sessions, offering guidance and support, and addressing any concerns or queries raised by the workers.
Monitoring productivity and efficiency
The assembly supervisor needs to monitor the productivity and efficiency of the assembly line to identify any bottlenecks or areas for improvement. They analyze production data, track key performance indicators, and implement strategies to enhance productivity. This may involve making process modifications, optimizing workflow, or introducing new techniques or technologies to streamline operations.
Implementing safety measures
Safety is paramount in any manufacturing setting, and the assembly supervisor is responsible for implementing and enforcing safety measures. They conduct regular safety inspections, ensure that all workers follow safety protocols, and address any potential hazards or risks. The assembly supervisor plays a critical role in creating a safe working environment for the assembly line workers.
Resolving issues and conflicts
Inevitably, issues and conflicts may arise within the assembly line environment. The assembly supervisor is responsible for addressing these problems promptly and effectively. They act as a mediator between workers, resolve conflicts, and find appropriate solutions to ensure a harmonious working environment.
To be an effective assembly supervisor, certain skills and qualifications are essential. These include:
Strong leadership and communication skills
An assembly supervisor must possess strong leadership qualities to guide and motivate the assembly line workers. They need to communicate effectively with their team, delegate tasks, and provide clear instructions. Additionally, good interpersonal skills are crucial for building rapport with team members and addressing any concerns or conflicts that may arise.
Technical knowledge and expertise
Having a strong technical background is important for an assembly supervisor. They need to understand the assembly process, machinery, and equipment used in the manufacturing industry. This knowledge allows them to identify issues, troubleshoot problems, and make informed decisions to optimize production.
Problem-solving and decision-making abilities
Assembly supervisors often encounter complex problems that require quick thinking and effective decision-making. They must possess excellent problem-solving skills to identify root causes, evaluate options, and implement appropriate solutions. The ability to think analytically and critically is highly valuable in this role.
Attention to detail and organizational skills
Attention to detail is crucial for an assembly supervisor, as they must ensure that products meet the required quality standards. They need to pay close attention to every aspect of the assembly process, identify any defects or deviations, and take corrective actions. Organizational skills are also essential to manage tasks, schedules, and resources efficiently.
Time management and multitasking abilities
Assembly supervisors often have multiple responsibilities and tasks to handle simultaneously. They must effectively manage their time, prioritize tasks, and multitask efficiently to meet production targets and deadlines. Strong time management skills help ensure smooth operations and avoid unnecessary delays.
Becoming an assembly supervisor requires a combination of education, experience, and personal development. Here are the steps to follow:
Gain relevant education and experience
Obtaining a relevant educational background is beneficial for aspiring assembly supervisors. A degree or diploma in manufacturing, engineering, or a related field provides a solid foundation of knowledge. Additionally, gaining practical experience through internships or entry-level positions in manufacturing companies can help develop a deeper understanding of assembly line operations.
Develop leadership and management skills
Building leadership and management skills is crucial for aspiring assembly supervisors. Taking courses or attending workshops on leadership, team management, and communication can enhance these skills. Developing the ability to inspire and motivate others, delegate tasks effectively, and resolve conflicts is essential for success in this role.
Acquire technical knowledge
To become an assembly supervisor, it is important to acquire technical knowledge related to the manufacturing industry. This includes understanding assembly processes, machinery, quality control measures, and safety regulations. Continuous learning and staying updated with the latest advancements in the industry are key to becoming a competent assembly supervisor.
Seek opportunities for professional development
Continual professional development is vital for growth as an assembly supervisor. Participating in workshops, seminars, and industry conferences provides opportunities to learn new techniques, gain insights from experts, and stay updated with industry trends. Seeking certifications or joining professional organizations related to manufacturing can also enhance credibility and career prospects.
Network and build connections in the industry
Building a strong professional network is beneficial for career advancement. Attending industry events, joining online forums or social media groups, and connecting with professionals in the manufacturing field can open doors to new opportunities. Networking allows for knowledge sharing, collaboration, and potential mentorship, which can greatly contribute to becoming a successful assembly supervisor.
Being an assembly supervisor comes with its share of challenges. Some common challenges include:
Meeting production targets
Assembly supervisors face the constant pressure to meet production targets and deadlines. They must find ways to optimize efficiency, streamline processes, and overcome any obstacles that may hinder productivity.
Dealing with personnel issues
Managing a team of assembly line workers can be challenging, as personnel issues may arise. This can include conflicts among team members, absenteeism, or lack of motivation. Assembly supervisors must address these issues promptly and maintain a positive work environment.
Handling unexpected disruptions
Unexpected disruptions, such as machinery breakdowns or supply chain disruptions, can impact production schedules. Assembly supervisors must be able to adapt quickly, find alternative solutions, and minimize the impact of these disruptions on the overall assembly process.
Managing time constraints
Assembly supervisors often work under strict time constraints. They must efficiently allocate resources, manage schedules, and make timely decisions to ensure that production targets are met within the given time frame.
Maintaining quality standards
Maintaining high-quality standards is crucial in the manufacturing industry. Assembly supervisors must constantly monitor the quality of products, identify any deviations or defects, and implement corrective actions to ensure that the final products meet the required standards.
The role of assembly supervisors is constantly evolving, driven by advancements in technology and changing industry demands. Here are some future prospects and trends in this field:
Advancements in automation and technology
Automation and technology continue to revolutionize the manufacturing industry. Assembly supervisors must adapt to new technologies, such as robotics and artificial intelligence, to optimize production processes and improve efficiency.
Importance of continuous improvement
Continuous improvement is becoming increasingly important in the manufacturing industry. Assembly supervisors need to embrace lean manufacturing principles, implement process improvement methodologies, and foster a culture of continuous learning and innovation within their teams.
Emphasis on sustainability and eco-friendly practices
Sustainability and environmental consciousness are gaining prominence in the manufacturing industry. Assembly supervisors must consider eco-friendly practices, such as waste reduction, energy conservation, and the use of sustainable materials, in their operations.
Increased focus on employee well-being
The well-being of assembly line workers is receiving more attention. Assembly supervisors must prioritize employee safety, provide a conducive work environment, and promote employee engagement and satisfaction. This can lead to higher productivity and lower turnover rates.
What is the role of an Assembly Supervisor?
An assembly supervisor is responsible for managing assembly line operations, ensuring quality control, training and supervising assembly line workers, monitoring productivity, implementing safety measures, and resolving issues and conflicts.
What skills are required to be an effective Assembly Supervisor?
Strong leadership and communication skills, technical knowledge, problem-solving abilities, attention to detail, organizational skills, and time management abilities are essential for an assembly supervisor.
How can one become an Assembly Supervisor?
To become an assembly supervisor, one can gain relevant education and experience, develop leadership and management skills, acquire technical knowledge, seek professional development opportunities, and build connections in the industry.
What are the main challenges faced by Assembly Supervisors?
Assembly supervisors face challenges such as meeting production targets, dealing with personnel issues, handling unexpected disruptions, managing time constraints, and maintaining quality standards.
What can we expect for the future of Assembly Supervisors?
The future of assembly supervisors includes advancements in automation and technology, a focus on continuous improvement, emphasis on sustainability and eco-friendly practices, and increased attention to employee well-being.