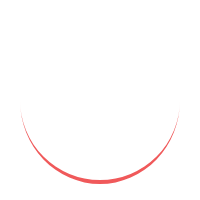
In the world of construction, creating robust and long-lasting structures is paramount. One method that has revolutionized the industry is prestressed concrete. A crucial component in the creation of prestressed concrete is the role of a technician - prestress. In this article, we will explore the responsibilities, qualifications, and skills required for a technician - prestress. Additionally, we will delve into the techniques of prestressing, safety measures, challenges faced, and the promising career opportunities in this field.
Prestressed concrete plays a vital role in enhancing the structural integrity of various construction projects. It is known for its ability to withstand high tension and compression forces, making it exceptionally strong and durable. By introducing compressive stress through prestressing, concrete can resist the tensile forces it may encounter, resulting in reduced cracking and improved load-bearing capacity. This technique has found extensive applications in bridges, high-rise buildings, parking structures, and more.
A technician - prestress plays a critical role in the successful implementation of prestressed concrete projects. They are responsible for ensuring that the prestressing operations are carried out efficiently and according to established standards and specifications. Technicians work closely with engineers, designers, and construction teams to ensure the structural integrity and safety of the project.
Becoming a technician - prestress requires a combination of educational qualifications and practical skills. Typically, a high school diploma or equivalent is the minimum educational requirement, although some employers may prefer candidates with an associate degree or relevant certification. Additionally, having a background in construction, engineering, or a related field is advantageous.
In terms of skills, a technician - prestress should possess a strong understanding of concrete materials, construction methods, and industry regulations. Proficiency in reading blueprints, using relevant software and tools, and performing calculations related to stress and load distribution is essential. Excellent communication, problem-solving, and teamwork skills are also vital for collaborating effectively with various stakeholders involved in the project.
The responsibilities of a technician - prestress can vary depending on the project and organizational structure. However, some common tasks include:
Preparation and Set-up: Technicians assist in preparing the work area, ensuring all necessary tools, equipment, and materials are available.
Installation and Tensioning: They perform the installation and tensioning of prestressing tendons according to design specifications, using specialized equipment and techniques.
Quality Control: Technicians conduct regular inspections to verify compliance with project requirements, including measurements, alignments, and safety standards.
Documentation: They maintain accurate records of all activities, including material usage, equipment maintenance, and test results.
Troubleshooting: Technicians identify and resolve any issues or challenges that arise during the prestressing process, ensuring the project progresses smoothly.
Collaboration: They work closely with engineers, architects, and construction teams, providing technical support and assisting in problem-solving.
There are two primary techniques used in prestressing: post-tensioning and pre-tensioning. Both methods offer unique advantages and find application in different construction scenarios.
Post-tensioning involves tensioning the tendons after the concrete has hardened. This technique offers greater flexibility in design and construction. The process can be summarized in the following steps:
Materials and Equipment Used
Post-tensioning requires specialized materials such as high-strength steel tendons, anchorage systems, and grouting materials. Additionally, hydraulic jacks and stressing equipment are utilized for applying tension to the tendons.
Installation Process
The technician installs ducts or sheaths in the formwork or within the concrete member before pouring.
After the concrete has cured, the tendons are inserted into the ducts, leaving the ends accessible.
Hydraulic jacks are used to apply the desired tension to the tendons.
The tendons are then anchored and secured using specialized anchorage systems.
Finally, grouting material is injected into the ducts to protect the tendons from corrosion and to transfer the tension to the surrounding concrete.
Benefits and Applications
Post-tensioning offers several advantages, including:
Increased structural strength and load-carrying capacity
Enhanced architectural freedom due to thinner and lighter structures
Reduced cracking and improved durability
Efficient construction process with faster installation and reduced labor costs
This technique finds applications in various structures like bridges, parking garages, slabs, and beams.
Pre-tensioning involves tensioning the tendons before the concrete is cast. This technique requires a pre-tensioning bed or casting bed, where the tendons are initially tensioned. The process can be summarized in the following steps:
Materials and Equipment Used
Pre-tensioning utilizes high-strength steel tendons, stressing equipment, and a pre-tensioning bed or casting bed.
Manufacturing Process
The tendons are tensioned on the pre-tensioning bed to the desired force.
Precast concrete elements, such as beams or panels, are cast around the tensioned tendons.
The concrete is allowed to cure and gain sufficient strength.
After the concrete has cured, the tendons are released from the pre-tensioning bed, transferring the compressive force to the concrete.
Benefits and Applications
Pre-tensioning offers several benefits, including:
Precise control over the amount of prestressing force applied
Reduction in material consumption due to optimized designs
High production efficiency in a controlled environment
Wide range of applications such as bridges, beams, and railway sleepers
Safety is of utmost importance in any construction project, and prestressing operations are no exception. Technicians - prestress must adhere to strict safety protocols to protect themselves and others involved in the project. This includes wearing appropriate personal protective equipment (PPE), conducting regular safety inspections, and following established safety guidelines.
Additionally, quality control measures play a crucial role in ensuring the integrity and longevity of prestressed concrete structures. Technicians are responsible for conducting quality checks at various stages, including material testing, tensioning force verification, and proper grouting procedures. Adhering to industry standards and specifications is paramount to deliver safe and durable structures.
While the role of a technician - prestress offers exciting opportunities, it also comes with its share of challenges. Some common challenges faced by technicians include:
Complexity: Prestressing techniques require a deep understanding of engineering principles and construction methods.
Precision: Achieving the desired level of tension and alignment requires meticulous attention to detail.
Time Management: Prestressing operations must be carefully coordinated with other construction activities to avoid delays.
Environmental Factors: Technicians must consider temperature, humidity, and other environmental factors that can impact the prestressing process.
Overcoming these challenges requires continuous learning, problem-solving skills, and effective communication within the project team.
The field of prestressed concrete offers promising career opportunities for technicians - prestress. As infrastructure development continues to rise, the demand for skilled professionals in this field is expected to grow. Technicians can find employment with construction companies, engineering firms, precast manufacturers, and specialized prestressing contractors.
With experience and additional certifications, technicians can progress to supervisory or management roles, overseeing prestressing operations on larger and more complex projects. Continuous professional development and staying updated with industry advancements are crucial for career growth in this dynamic field.
1. What is the difference between post-tensioning and pre-tensioning?
Post-tensioning involves tensioning the tendons after the concrete has hardened, while pre-tensioning involves tensioning the tendons before the concrete is cast. Both techniques offer unique advantages and find applications in different construction scenarios.
2. What qualifications are required to become a technician - prestress?
Typically, a high school diploma or equivalent is the minimum educational requirement, although some employers may prefer candidates with an associate degree or relevant certification. Additionally, having a background in construction, engineering, or a related field is advantageous.
3. What are the benefits of using prestressed concrete?
Prestressed concrete offers increased structural strength, improved load-carrying capacity, reduced cracking, and enhanced durability. It also allows for architectural freedom and offers faster construction processes with reduced labor costs.
4. What safety measures should technicians - prestress follow?
Technicians must adhere to strict safety protocols, including wearing appropriate PPE, conducting regular safety inspections, and following established safety guidelines. Safety should be a top priority throughout the prestressing operations.
5. Are there opportunities for career growth in the field of prestressed concrete?
Yes, there are promising career opportunities for technicians - prestress in the field of prestressed concrete. With experience and additional certifications, technicians can progress to supervisory or management roles, overseeing larger and more complex projects.