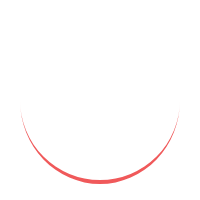
Rubbing operator is a type of machine used in the manufacturing industry to smooth and refine materials, such as metals, wood, and plastics. The process involves using an abrasive material, such as sandpaper or polishing pads, to grind away imperfections and create a smooth surface. Rubbing operator is an essential tool in many industries, including automotive, aerospace, and construction.
In this article, we will discuss the working of rubbing operator, the factors affecting its efficiency, the benefits of using it, and its common applications.
A rubbing operator consists of a rotating wheel or drum, which is coated with an abrasive material, and a surface that needs to be refined. The operator applies pressure to the surface while it moves against the abrasive material, which removes imperfections and creates a smooth finish.
Materials Used in Rubbing Operator
The abrasive material used in rubbing operator can vary depending on the material being refined. For example, metalworking often uses sandpaper or grinding wheels, while woodworking may use sanding belts or pads. Polishing pads are commonly used for plastics and other softer materials.
The process of rubbing operator involves several steps, including selecting the appropriate abrasive material, adjusting the machine settings, and applying pressure to the surface being refined. The operator may need to make several passes over the surface to achieve the desired level of smoothness.
Several factors can affect the efficiency of rubbing operator, including machine settings, material type and quality, and operator skills.
The machine settings, such as the speed of the drum and the pressure applied to the surface, can greatly affect the efficiency and effectiveness of the rubbing operator. Proper adjustment of the machine settings can result in a smoother finish and a faster process.
The type and quality of the material being refined can also affect the efficiency of rubbing operator. Harder materials may require more abrasive force, while softer materials may require a gentler touch. Poor quality materials can result in more imperfections and a longer refining process.
The skills and experience of the operator can greatly affect the efficiency of rubbing operator. An experienced operator can quickly identify the appropriate machine settings and apply the right amount of pressure to achieve a high-quality finish.
There are several benefits to using a rubbing operator in the manufacturing industry, including high-quality output,
Rubbing operator can save time and money by reducing the amount of manual labor required to refine materials. Automated rubbing operators can also operate continuously, increasing efficiency and reducing downtime.
Using a rubbing operator can increase safety in the manufacturing process by reducing the risk of injury from manual labor. Automated machines also have safety features that prevent accidents, such as emergency stop buttons and safety guards.
There are two main types of rubbing operator: manual and automatic.
Manual rubbing operator requires a human operator to guide the surface being refined against the abrasive material. While manual machines may require more skill and experience, they are often more versatile and can handle a wider variety of materials.
Automatic rubbing operator is fully automated and does not require human intervention. These machines can operate continuously and often have advanced features that increase efficiency and reduce downtime.
Rubbing operator is used in many industries for a variety of applications, including:
Rubbing operator is commonly used in metalworking to refine surfaces and remove imperfections. It can be used to create a smooth finish on metals such as aluminum, steel, and titanium.
Rubbing operator is also used in woodworking to refine surfaces and remove imperfections. It can be used to create a smooth finish on wood, such as furniture and cabinetry.
Rubbing operator is also used in the plastics industry to refine surfaces and remove imperfections. It can be used to create a smooth finish on plastic materials, such as automotive parts and electronic components.
Proper maintenance and troubleshooting of rubbing operator are essential to ensure optimal performance and longevity. Here are some tips for maintaining and troubleshooting your rubbing operator:
Regular cleaning and lubrication of rubbing operator can help prevent damage and increase efficiency. Clean the machine regularly and lubricate moving parts to reduce friction and wear.
Perform routine inspections and maintenance on your rubbing operator to identify and address any issues before they become bigger problems. This can include checking belts and bearings, adjusting machine settings, and replacing worn or damaged parts.
Common issues with rubbing operator include machine jams, uneven finishes, and abrasive material buildup. These issues can often be resolved by adjusting machine settings, replacing worn or damaged parts, or changing the abrasive material.
Advancements in technology and growing demand for automated machines are driving the future of rubbing operator in the manufacturing industry. Automated rubbing operators with advanced features, such as artificial intelligence and machine learning, are becoming more prevalent and can greatly increase efficiency and productivity.
Can rubbing operator be used on all materials?
Rubbing operator can be used on a variety of materials, but the type and quality of the abrasive material may vary depending on the material being refined.
Is manual rubbing operator better than automatic?
It depends on your specific needs and the materials being refined. Manual rubbing operator requires more skill and experience but can handle a wider variety of materials, while automatic rubbing operator is fully automated and can increase efficiency and reduce downtime.
How often should I perform maintenance on my rubbing operator?
Routine maintenance and inspections should be performed regularly to identify and address any issues before they become bigger problems. This can include checking belts and bearings, adjusting machine settings,
replacing worn or damaged parts, and cleaning and lubricating the machine.
What safety measures should be taken when using rubbing operator?
When using rubbing operator, safety measures such as wearing protective gear, following machine instructions, and using emergency stop buttons should be taken to prevent accidents and injury.
How can rubbing operator increase efficiency and productivity in manufacturing?
Rubbing operator can increase efficiency and productivity in manufacturing by reducing the amount of manual labor required, operating continuously, and incorporating advanced features such as artificial intelligence and machine learning.
About Us
The Fitter and Rubbing Operator is responsible for creating wooden frame through various stages of woodcutting, polishing, joining and assembling which is subsequently embellished with artistic handiworks of paper Mache. The fitter is thus expected to be skilled carpenter well aware of configuration and size of the frame so as to be suitable for Subsequent work of paper Mache over them.He is responsible for making suitable solution out of various ingredients in defined proportions and applying the same to Sakhta prepared by Sakhta Saaz and the subsequent process of polishing to impart a smoother look to the surface.
Rubbing Operator
Aliases: Saktha Finisher
Industry/Sector(s): Handicrafts and Carpets
JOB DESCRIPTION
The tasks a Rubbing Operator is expected to perform include:
Making a suitable solutions of ingredients in a defined proportion
Applying the solution to sakhta prepared by sakhta saaz
Processing the polishing to impart a smoother look to the surface
WORK ENVIRONMENT
It is not a desk job
Need not handle a team
Local traveling is not a part of this job profile
Part-time work and contractual jobs may be available
Work from home option is not available