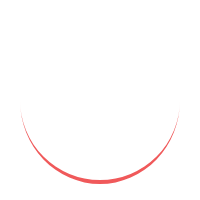
A quality supervisor is responsible for ensuring that products or services meet the required quality standards. They oversee the quality assurance processes, create quality standards and procedures, and ensure compliance with regulations. A quality supervisor plays a crucial role in improving product quality, increasing customer satisfaction, and reducing costs and risks. In this article, we will discuss the roles and responsibilities of a quality supervisor, the skills required to be one, the education and certification requirements, the benefits of hiring one, and the challenges they face.
A quality supervisor is responsible for monitoring and evaluating the quality assurance processes, including testing, inspection, and auditing. They ensure that all processes are conducted according to the established procedures and standards. They also identify any issues or areas that need improvement and implement corrective actions.
A quality supervisor is responsible for creating and maintaining quality standards and procedures. They develop processes to ensure that products or services meet the required quality standards. They also review and update existing procedures to improve quality and efficiency.
A quality supervisor is responsible for ensuring that the company complies with all relevant regulations and standards. They keep up-to-date with changes in regulations and make sure that the company meets all the requirements. They also ensure that the company's products or services meet all the safety and quality standards.
A quality supervisor should have excellent communication skills, both written and verbal. They should be able to communicate with different stakeholders effectively, including employees, management, and customers. They should be able to explain technical information in a clear and concise manner.
A quality supervisor should be able to analyze data and identify patterns and trends. They should be able to use critical thinking to solve problems and make decisions. They should also be able to think creatively and come up with innovative solutions.
A quality supervisor should have strong leadership skills and be able to motivate and inspire their team. They should be able to delegate tasks effectively and manage their team's performance. They should also have excellent interpersonal skills and be able to build strong relationships with their team members and other stakeholders.
A quality supervisor should have a bachelor's degree in a relevant field, such as engineering, quality management, or business administration. They should also have relevant work experience in quality assurance or a related field.
Some certifications that can be helpful for quality supervisors include Certified Quality Engineer (CQE), Certified Quality Auditor (CQA), and Six Sigma Green Belt.
One of the main benefits of hiring a quality supervisor is improving the quality of the products or services. A quality supervisor ensures that the products or services meet the required quality standards and that the customers' needs and expectations are met. This results in increased customer satisfaction and loyalty.
A quality supervisor plays a crucial role in ensuring customer satisfaction. They ensure that the products or services meet the required quality standards and that the customers' needs and expectations are met. This results in increased customer satisfaction and loyalty, which can lead to increased revenue and profitability.
A quality supervisor helps to reduce costs and risks associated with poor quality products or services. They identify areas that need improvement and implement corrective actions, which can result in cost savings. They also ensure that the company complies with all relevant regulations and standards, which can help to reduce the risk of fines and legal issues.
One of the challenges of being a quality supervisor is dealing with resistance to change. Employees may be resistant to changes in procedures or standards, which can make it difficult to implement improvements. A quality supervisor should be able to communicate the benefits of the changes effectively and address any concerns or issues that arise.
Another challenge of being a quality supervisor is managing time and resources effectively. They may have to balance competing priorities and ensure that all tasks are completed on time and within budget. They should be able to delegate tasks effectively and manage their team's performance to ensure that all tasks are completed efficiently.
A quality supervisor may have to balance competing priorities, such as quality, cost, and schedule. They should be able to identify areas that need improvement and implement corrective actions while ensuring that the company's products or services meet all the required quality standards. They should also be able to manage their team's performance and delegate tasks effectively to ensure that all priorities are addressed.
What is a quality supervisor?
A quality supervisor is responsible for ensuring that products or services meet the required quality standards. They oversee the quality assurance processes, create quality standards and procedures, and ensure compliance with regulations.
What skills are required to be a quality supervisor?
A quality supervisor should have excellent communication, analytical, and leadership skills. They should also be able to think critically and creatively, analyze data, and identify patterns and trends.
What education and certification requirements are needed to be a quality supervisor?
A quality supervisor should have a bachelor's degree in a relevant field and relevant work experience. Some certifications that can be helpful include Certified Quality Engineer (CQE), Certified Quality Auditor (CQA), and Six Sigma Green Belt.
What are the benefits of hiring a quality supervisor?
Hiring a quality supervisor can result in improved product quality, increased customer satisfaction, and reduced costs and risks associated with poor quality products or services.
What are the challenges of being a quality supervisor?
Being a quality supervisor can be challenging, and they may have to deal with managing resistance to change, balancing competing priorities, and managing time and resources effectively. However, with the right skills and experience, a quality supervisor can help a company improve its products or services and achieve greater success.
How can a quality supervisor ensure compliance with regulations?
A quality supervisor can ensure compliance with regulations by staying up-to-date with the latest regulations and standards, creating and implementing quality standards and procedures, and monitoring and reporting on compliance.
What are some examples of quality assurance processes a quality supervisor may oversee?
Some examples of quality assurance processes a quality supervisor may oversee include product inspections, testing, audits, and process improvements.
What is the role of a quality supervisor in improving customer satisfaction?
A quality supervisor plays a crucial role in improving customer satisfaction by ensuring that products or services meet the required quality standards and that the customers' needs and expectations are met. This can lead to increased customer loyalty and profitability for the company.
What is the difference between a quality supervisor and a quality control inspector?
A quality supervisor is responsible for overseeing the quality assurance processes and ensuring compliance with regulations, while a quality control inspector is responsible for inspecting and testing products or services to ensure that they meet the required quality standards.
What are some best practices for managing resistance to change as a quality supervisor?
Some best practices for managing resistance to change as a quality supervisor include communicating the benefits of the changes effectively, addressing any concerns or issues that arise, involving employees in the process, and providing training and support for the new procedures or standards.
About Us
Rubber Product-Quality Assurance Supervisor is responsible for inspecting/ controlling/assuring the quality of raw materials and their storage and issue, the plant processing and the intermediate products produced at different stages of the production process such as rubber compounds, semi-finished and finished products. They are responsible for ensuring conformity of quality standards. They are also responsible for final product inspection, segregation of non-conforming products and packaging.