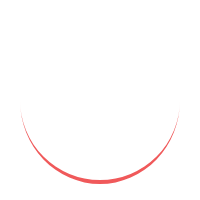
Have you ever wondered how electronic devices are meticulously assembled? Behind every perfectly functioning electronic module lies the craftsmanship of a skilled module soldering operator. In this article, we will explore the world of module soldering, its importance, the required skills and qualifications, tools and equipment, a step-by-step guide, common mistakes to avoid, best practices, troubleshooting tips, safety precautions, and future trends. So, grab your soldering iron and let's dive in!
Module Soldering Operator Introduction
Module soldering is the process of joining electronic components to a printed circuit board (PCB) using solder. It plays a vital role in the manufacturing of various electronic devices such as smartphones, computers, automotive systems, and medical equipment. The precision and quality of soldering directly impact the functionality and reliability of these devices.
What is Module Soldering?
Module soldering involves creating a strong, conductive bond between electronic components and the PCB to establish electrical connections. It requires the operator to carefully melt solder onto the joint, allowing it to cool and solidify, forming a secure connection. This process demands both technical expertise and attention to detail.
Importance of Module Soldering
Accurate module soldering is crucial for several reasons. Firstly, it ensures reliable electrical connections between components, preventing signal loss, intermittent failures, or complete device malfunction. Additionally, proper soldering guarantees mechanical stability, preventing loose connections due to vibrations or physical stress. Finally, high-quality soldering promotes longevity, reducing the chances of premature failure and the need for repairs or replacements.
Module Soldering Operator Skills and Qualifications
Becoming a proficient module soldering operator requires a combination of technical skills and knowledge. While a formal education in electronics can provide a strong foundation, practical experience and continuous learning are equally important. Some essential skills for a module soldering operator include:
H3: 1. Manual Dexterity
A steady hand and excellent hand-eye coordination are essential for precise soldering. Operators must be able to handle small electronic components and delicate PCBs with precision.
H3: 2. Knowledge of Electronics
Understanding electronic circuits, components, and their functions is vital for successful module soldering. This knowledge helps in identifying correct soldering points and avoiding damage to sensitive parts.
H3: 3. Soldering Techniques
Proficiency in various soldering techniques, such as through-hole and surface mount soldering, is crucial. Each technique requires different tools and approaches, and the operator should be adept in selecting the appropriate method for the task at hand.
H3: 4. Problem-Solving Skills
Module soldering operators often encounter challenges during the process. The ability to troubleshoot and solve problems efficiently is essential for maintaining productivity and ensuring high-quality results.
Module Soldering Operator Tools and Equipment
To excel as a module soldering operator, it is important to have the right tools and equipment at your disposal. Here are some essential items that every soldering workstation should have:
H3: 1. Soldering Iron
A high-quality soldering iron with adjustable temperature control is crucial for precise soldering. It should have a fine, interchangeable
H4: 2. Solder Wire and Flux
Choosing the appropriate solder wire and flux is essential for achieving reliable solder joints. Different solder wire compositions are suitable for various applications, and flux helps clean and prepare the surfaces for soldering.
H4: 3. Desoldering Tools
Desoldering tools such as desoldering pumps or solder wick are necessary for correcting mistakes or removing components when needed. These tools help in the efficient removal of solder and facilitate repairs or modifications.
H4: 4. Magnifying Tools
Having magnifying tools like a magnifying glass or a microscope assists in inspecting small components, verifying solder connections, and identifying potential issues or defects.
H4: 5. Safety Equipment
Safety should never be compromised when working with soldering equipment. Essential safety equipment includes heat-resistant gloves, safety goggles, and proper ventilation to protect against burns, eye injuries, and exposure to fumes.
Step-by-Step Guide to Module Soldering
To successfully solder electronic components onto a PCB, follow these step-by-step instructions:
H3: 1. Prepare Your Workstation
Ensure you have a clean, well-organized workstation with all the necessary tools and equipment within reach. Clear any clutter and provide adequate lighting for better visibility.
H3: 2. Identify Soldering Points
Carefully examine the PCB and identify the specific points where components need to be soldered. Refer to the circuit diagram or assembly instructions to ensure accuracy.
H3: 3. Clean and Prepare the Surfaces
Clean the soldering points on the PCB and the component leads using isopropyl alcohol and a clean cloth. This removes any dirt, oils, or oxidation that could hinder proper soldering.
H3: 4. Tin the Soldering Iron
Before starting, "tin" the soldering iron tip by melting a small amount of solder onto it. This ensures better heat transfer and facilitates smooth soldering.
H3: 5. Heat the Joint
With the soldering iron heated to the appropriate temperature, gently touch the joint where the component lead and the PCB pad meet. Apply heat evenly to avoid overheating the components.
H3: 6. Apply Solder
Once the joint is heated, bring the solder wire in contact with the joint, allowing it to flow and cover the connection. Ensure the solder flows smoothly and evenly, forming a shiny, concave fillet.
H3: 7. Remove the Soldering Iron
After applying solder, remove the soldering iron and allow the joint to cool naturally. Do not disturb or move the joint until it solidifies to avoid creating cold solder joints.
H3: 8. Inspect and Test
Inspect the solder joint visually to ensure it is smooth, shiny, and free from any visible defects. Use a multimeter or appropriate testing equipment to verify the electrical continuity and functionality of the soldered components.
Module Soldering Operator Common Mistakes to Avoid
While module soldering, it's important to be aware of common mistakes that can compromise the quality of the solder joints. Here are some mistakes to avoid:
H3: 1. Insufficient Heat
Inadequate heat can result in cold solder joints that have poor electrical conductivity. Ensure the soldering iron is at the correct temperature and maintain consistent heat during the soldering process.
H3: 2. Excessive Heat
Excessive heat can damage sensitive components, PCB traces, or nearby parts. It is crucial to balance the heat applied to the joint without exceeding the component's tolerance.
H3: 3. Insufficient Cleaning
Failure to clean the surfaces properly before soldering can lead to weak joints due to poor adhesion.
About Us
The individual at work connects the positive end of a solar cell to a negative end of another solar cell by soldering and repeating the process to interconnect all the required number of solar cells in an array to form the solar module.