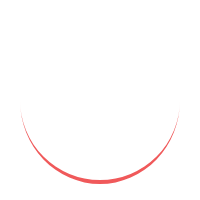
Understanding the Inner Layer
The inner layer, often referred to as the core, is a vital component in the manufacturing of various products, including electronic circuit boards, laminates, and composite materials. It acts as a foundation, providing mechanical support and electrical connectivity between different layers. The inner layer consists of a substrate material, such as fiberglass or resin, and is typically sandwiched between copper foils.
Inner Layer and Pressing Operator Role of the Pressing Operator
The pressing operator is responsible for the critical task of laminating the inner layers together to form a solid and cohesive structure. This process involves applying heat and pressure to fuse the layers and ensure their proper adhesion. The pressing operator operates specialized machinery, closely monitors the temperature and pressure levels, and follows specific procedures to achieve the desired results.
Importance of Inner Layer and Pressing Operator
The quality and reliability of the final product depend greatly on the proper functioning of the inner layer and the expertise of the pressing operator. A well-constructed inner layer ensures the stability of the product, prevents delamination, and enhances its overall performance. Likewise, a skilled pressing operator ensures that the pressing process is carried out accurately, minimizing defects and ensuring consistent quality.
Qualities of a Proficient Pressing Operator
Being a pressing operator requires a combination of technical skills, attention to detail, and problem-solving abilities. Here are some essential qualities of a proficient pressing operator:
Technical Knowledge: A deep understanding of the pressing machinery, materials, and the pressing process is essential for optimal performance.
Attention to Detail: Precise measurements, monitoring temperature and pressure, and identifying potential issues require a keen eye for detail.
Troubleshooting Skills: The ability to identify and resolve pressing-related problems quickly is crucial to maintain efficiency and minimize downtime.
Adaptability: Adapting to changing production requirements and working with different materials and technologies is necessary for a pressing operator.
Teamwork: Collaborating with colleagues, such as design engineers and quality control personnel, to ensure smooth operations is vital.
Inner Layer and Pressing Operator Training and Skills Required
To become an effective pressing operator, acquiring the necessary skills and training is crucial. While formal education in manufacturing or engineering can provide a solid foundation, hands-on experience and on-the-job training are equally important. Some essential skills for a pressing operator include:
Understanding of pressing machinery and its operation
Knowledge of materials used in the inner layer and their properties
Ability to interpret technical drawings and specifications
Familiarity with safety protocols and procedures
Troubleshooting and problem-solving skills
Basic computer literacy for machine control interfaces
Inner Layer and Pressing Operator Steps to Become an Effective Pressing Operator
Education and Training: Pursue relevant educational programs or certifications in manufacturing or engineering to gain theoretical knowledge.
Hands-on Experience: Seek internships or apprenticeships in manufacturing companies to gain practical experience with pressing machinery.
On-the-Job Training: Join a manufacturing company as a trainee pressing operator to receive comprehensive training and guidance from experienced professionals.
Continuous Learning: Stay updated with the latest advancements in pressing technology and materials by attending workshops, seminars, or online courses.
Practice and Improvement: Continuously refine pressing skills through practice and seeking feedback from supervisors and colleagues.
Inner Layer and Pressing Operator Common Challenges and How to Overcome Them
Being a pressing operator can come with its fair share of challenges. Some common ones include:
Uneven Pressing: Uneven application of pressure can result in delamination or weak spots. Regularly calibrate and maintain pressing machinery to ensure even pressure distribution.
Temperature Control: Inadequate temperature control can lead to insufficient bonding or material damage. Regularly monitor and adjust temperature settings as required.
Material Compatibility: Different materials require specific pressing conditions. Gain a thorough understanding of the materials used and their pressing requirements.
Quality Control: Ensuring consistent quality can be challenging. Implement robust quality control measures, conduct regular inspections, and address any deviations promptly.
Tips for Success as a Pressing Operator
Attention to Detail: Pay meticulous attention to every aspect of the pressing process to maintain high-quality standards.
Effective Communication: Collaborate and communicate effectively with colleagues, supervisors, and other stakeholders to ensure smooth operations.
Continuous Learning: Stay updated with industry trends, new technologies, and best practices to enhance your skills and knowledge.
Problem-Solving Mindset: Develop strong problem-solving abilities to address pressing-related issues and improve efficiency.
Adaptability: Embrace changes and be adaptable to evolving production requirements, technologies, and materials.
Inner Layer and Pressing Operator FAQs
Q1. What is the role of the inner layer in product manufacturing?
The inner layer provides mechanical support and electrical connectivity between different layers in products like electronic circuit boards and laminates.
Q2. What does a pressing operator do?
A pressing operator is responsible for laminating inner layers together by applying heat and pressure, ensuring proper adhesion.
Q3. What qualities are required to be a proficient pressing operator?
A proficient pressing operator should possess technical knowledge, attention to detail, troubleshooting skills, adaptability, and teamwork abilities.
Q4. How can I become a pressing operator?
You can pursue relevant education, gain hands-on experience through internships or apprenticeships, and receive on-the-job training to become a pressing operator.
Q5. What are some common challenges faced by pressing operators?
Common challenges include uneven pressing, temperature control issues, material compatibility, and maintaining consistent quality. Calibration, temperature monitoring, and robust quality control measures can help overcome these challenges.