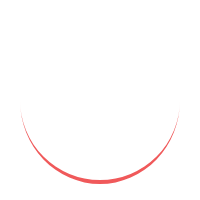
Heat treatment is a crucial process in various industries that involves altering the properties of materials to improve their mechanical and physical characteristics. This article explores the role of a heat treatment operator, their responsibilities, required skills, common processes, safety measures, and more.
Introduction
Heat treatment plays a vital role in manufacturing processes, particularly in industries such as automotive, aerospace, and metallurgy. It involves subjecting materials to controlled heating and cooling cycles to modify their microstructure and enhance their properties. A heat treatment operator is responsible for executing these processes effectively and ensuring the desired outcomes.
What is Heat Treatment?
Heat treatment is a metallurgical process used to alter the physical and chemical properties of materials. By applying heat to the material and controlling the cooling process, the operator can achieve desired characteristics such as hardness, strength, toughness, and ductility. This process can be applied to various materials, including metals, alloys, and even some polymers.
Importance of Heat Treatment Operators
Heat treatment operators play a critical role in ensuring the quality and integrity of the treated materials. Their expertise in controlling heating and cooling cycles is essential to achieve the desired material properties. The skills and knowledge of heat treatment operators directly impact the performance and reliability of components and products in many industries.
Roles and Responsibilities of a Heat Treatment Operator
Heat treatment operators have multifaceted responsibilities throughout the heat treatment process. Some of their key roles include:
Workpiece Preparation: Inspecting, cleaning, and organizing the workpieces before heat treatment.
Operating Equipment: Setting up and operating heat treatment equipment such as furnaces, quenching tanks, and tempering ovens.
Process Execution: Following established heat treatment procedures, including heating, soaking, cooling, and monitoring.
Quality Control: Conducting inspections and tests to ensure the desired material properties are achieved.
Documentation: Maintaining accurate records of heat treatment parameters, results, and any deviations from standard procedures.
Maintenance and Troubleshooting: Performing routine maintenance on equipment and troubleshooting issues that arise during the process.
Required Skills and Qualifications
To excel as a heat treatment operator, several skills and qualifications are necessary. These include:
Technical Knowledge: Understanding the principles of heat treatment, metallurgy, and the behavior of different materials during the process.
Operating Equipment: Proficiency in operating heat treatment equipment, including temperature controls, timers, and cooling systems.
Attention to Detail: Being meticulous in following procedures, recording data accurately, and recognizing deviations or abnormalities.
Problem-solving Skills: The ability to identify and resolve issues that may arise during heat treatment processes.
Knowledge of Safety Measures: Being aware of safety protocols, handling hazardous materials, and mitigating risks associated with heat treatment operations.
Equipment and Tools Used in Heat Treatment
Heat treatment operators work with various equipment and tools to carry out their tasks effectively. Some common ones include:
Furnaces: Used for heating workpieces to specific temperatures for different heat treatment processes.
Quenching Tanks: Used for rapid cooling of heated workpieces to achieve desired material properties.
Tempering Ovens: Used to relieve internal stresses and adjust the hardness of hardened workpieces.
Thermocouples and Pyrometers: Instruments used to measure and monitor temperatures accurately.
Protective Gear: Safety equipment such as gloves, goggles, aprons, and masks to ensure operator safety during handling and exposure to high temperatures and hazardous materials.
Safety Measures in Heat Treatment Operations
Safety is of utmost importance in heat treatment operations. Heat treatment operators must adhere to safety protocols to prevent accidents and injuries. Some essential safety measures include:
Personal Protective Equipment (PPE): Wearing appropriate protective gear to safeguard against heat, sparks, chemicals, and other hazards.
Ventilation: Ensuring proper ventilation in the workspace to prevent the accumulation of toxic fumes or gases.
Fire Safety: Having fire extinguishers readily available and implementing fire prevention measures.
Material Handling: Using proper lifting techniques and equipment to handle heavy or hot workpieces.
Training and Education: Providing comprehensive training to operators on safety procedures and potential risks.
Heat Treatment Operator Common Heat Treatment Processes
Heat treatment encompasses various processes, each serving specific purposes. Some common heat treatment processes include:
Annealing
Annealing involves heating the material to a specific temperature and then gradually cooling it. This process reduces internal stresses, improves machinability, and increases ductility.
Hardening
Hardening is a process where the material is heated and then rapidly cooled, typically through quenching. It results in increased hardness, strength, and wear resistance.
Tempering
Tempering is a heat treatment process performed after hardening to reduce brittleness and improve toughness. It involves reheating the hardened material to a lower temperature and then cooling it.
Case Hardening
Case hardening involves adding a hard outer layer to a material while maintaining a relatively softer core. This process enhances wear resistance while retaining the toughness of the core material.
Heat Treatment Procedures
Heat treatment procedures involve several steps to ensure the desired material properties are achieved consistently. The key steps include:
Preparing the Workpiece
Before heat treatment, the workpiece needs to be cleaned thoroughly to remove contaminants. It should also be inspected for any defects or damage that may affect the process.
Heating the Workpiece
The workpiece is then placed in the furnace and heated to the specified temperature. The heating rate and soaking time depend on the material and the desired properties.
Cooling the Workpiece
After reaching the desired temperature, the workpiece is rapidly cooled using methods like quenching or air cooling. The cooling rate affects the material's final properties, and specific techniques are chosen accordingly.
Monitoring and Quality Control in Heat Treatment
Throughout the heat treatment process, monitoring and quality control are crucial to ensure the desired material properties are achieved. Heat treatment operators employ various techniques such as:
Temperature Monitoring: Continuously monitoring and recording the temperature using thermocouples or pyrometers.
Microstructure Examination: Inspecting the material's microstructure using microscopy techniques to assess grain size, phase changes, and other characteristics.
Hardness Testing: Conducting hardness tests using methods like Rockwell or Vickers hardness testing to measure the material's hardness.
Dimensional and Visual Inspection: Checking the workpiece's dimensions, surface finish, and overall quality against specified requirements.
Challenges and Problems in Heat Treatment Operations
Heat treatment operations can present various challenges and problems that heat treatment operators must address. Some common issues include:
Distortion: Workpieces can experience distortion or warping due to non-uniform heating or cooling rates. Proper fixturing and quenching techniques can help minimize this issue.
Cracking: Rapid cooling can cause thermal stresses, leading to cracking in the material. Quenching media and process parameters must be carefully chosen to prevent cracking.
Decarburization: Some materials are prone to surface decarburization, which can affect their properties. Protective atmospheres or heat treatment under controlled environments can mitigate this problem.
Tips for Becoming a Successful Heat Treatment Operator
Becoming a successful heat treatment operator requires a combination of technical knowledge, practical skills, and a dedication to quality. Here are some tips for aspiring operators:
Continuous Learning: Stay updated with the latest advancements, techniques, and equipment in the field of heat treatment through training programs, workshops, and industry publications.
Attention to Detail: Be meticulous in following procedures, recording data accurately, and observing any deviations or abnormalities during the process.
Collaboration: Work closely with metallurgists, engineers, and quality control personnel to understand specific requirements and ensure the desired outcomes.
Problem-solving Abilities: Develop strong problem-solving skills to identify and resolve issues that may arise during heat treatment operations.
Safety Consciousness: Prioritize safety at all times by following safety protocols, wearing appropriate protective gear, and being aware of potential hazards.
Heat Treatment Operator Career Opportunities and Growth
A career as a heat treatment operator offers opportunities for growth and advancement. With experience and additional training, operators can progress to supervisory or managerial roles within heat treatment departments or transition to roles such as metallurgists, quality control specialists, or process engineers. Continuous learning and staying updated with industry developments can pave the way for long-term career growth.
Heat Treatment Operator FAQs
1. Is heat treatment only applicable to metals?
Heat treatment is commonly used for metals and alloys, but it can also be applied to certain polymers and other materials with thermal properties that allow for controlled heating and cooling.
2. Can heat treatment change the dimensions of a workpiece?
Yes, heat treatment processes can cause dimensional changes in workpieces due to thermal expansion and contraction. Proper fixturing and compensation techniques can help minimize dimensional alterations.
3. Are there any risks associated with heat treatment operations?
Heat treatment operations involve working with high temperatures, hazardous chemicals, and potentially dangerous equipment. Adhering to safety protocols and wearing appropriate protective gear is essential to mitigate risks.
4. How long does it take to become a proficient heat treatment operator?
Becoming a proficient heat treatment operator typically requires a combination of practical experience, on-the-job training, and continuous learning. The timeline can vary, but it generally takes several years to develop the necessary skills and knowledge.
5. Can heat treatment be performed on site, or is it typically outsourced?
Heat treatment operations can be performed on-site if the necessary equipment and expertise are available. However, many companies choose to outsource heat treatment processes to specialized facilities for efficiency and quality assurance.