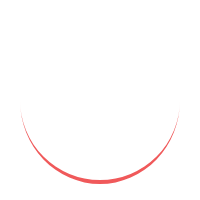
As a furnace operator in ceramics, your primary responsibility is to operate and maintain the furnace used in the production of ceramics. This role is crucial in ensuring that the furnace operates efficiently and that the quality of the ceramic products produced is consistent. In this article, we will explore the role of a furnace operator in ceramics, including their qualifications, job responsibilities, and career prospects.
To become a furnace operator in ceramics, you typically need a high school diploma or equivalent. However, some employers may prefer or require additional education, such as an associate or bachelor's degree in a related field, such as materials science, ceramics engineering, or manufacturing technology.
Furnace operators in ceramics must have a solid understanding of the principles of heat transfer, combustion, and materials science. They should also have knowledge of furnace operations, including loading and unloading, temperature control, and maintenance.
Furnace operators in ceramics must be physically fit and able to stand, walk, and lift heavy objects for extended periods. They should also have good hand-eye coordination, manual dexterity, and the ability to work in confined spaces.
The primary responsibility of a furnace operator in ceramics is to operate and monitor the furnace used in the production of ceramics. This includes loading and unloading the furnace, controlling the temperature and atmosphere inside the furnace, and adjusting the furnace's settings as needed.
Furnace operators in ceramics are responsible for maintaining the furnace and associated equipment to ensure that they operate efficiently and safely. This includes performing regular inspections, cleaning, and repairing or replacing damaged components.
Troubleshooting and Problem-Solving In addition to operating and maintaining the furnace, furnace operators in ceramics must also be able to troubleshoot and solve problems that may arise during the production process. This may involve diagnosing issues with the furnace or equipment, adjusting settings, or making repairs to minimize downtime and maintain production schedules.
Furnace operations can pose significant hazards to operators, including exposure to high temperatures, flames, and hazardous chemicals. Therefore, safety is a critical aspect of furnace operations in the ceramics industry.
Some of the hazards associated with furnace operations in ceramics include burns, electrocution, explosions, and chemical exposure. Additionally, furnace operators may be at risk of developing respiratory or hearing problems due to prolonged exposure to high temperatures and noise levels.
To minimize these risks, furnace operators in ceramics must follow strict safety procedures and guidelines. This may include wearing protective clothing and equipment, ensuring proper ventilation and air quality, and following established protocols for loading, unloading, and operating the furnace.
As with many industries, furnace operations in ceramics are constantly evolving, driven by new technologies and innovations. Some of the emerging trends in furnace operations in ceramics include:
Advancements in automation and digital technologies are revolutionizing furnace operations in ceramics. This includes the use of sensors and software to monitor and control furnace operations, improving efficiency, and reducing the risk of errors.
As concerns about the environment and energy costs continue to grow, there is an increasing focus on sustainability and energy efficiency in furnace operations in ceramics. This includes the use of renewable energy sources and optimizing the furnace's design to minimize waste and energy consumption.
As the demand for ceramic products continues to grow, so does the need for skilled furnace operators. The outlook for careers in furnace operations in ceramics is strong, with many opportunities for advancement and growth.
According to the Bureau of Labor Statistics, the employment of furnace, kiln, and oven operators in the ceramics industry is expected to grow by 4% from 2020 to 2030, with an increasing demand for skilled operators to support the growth of the industry.
The average annual salary for furnace operators in ceramics is around $37,000, with opportunities for advancement and higher salaries with experience and additional training.
Furnace operators in ceramics may have opportunities for advancement into supervisory or management roles, or to specialize in areas such as furnace design, automation, or materials science.
What qualifications do I need to become a furnace operator in ceramics?
What are the job responsibilities of a furnace operator in ceramics?
What safety procedures are involved in furnace operations in ceramics?
What emerging technologies are changing furnace operations in ceramics?
What are the career prospects for furnace operators in ceramics?
JOB DESCRIPTION
The tasks a Furnaceman, Glass is expected to perform include:
Operating the gas, oil, coal, coke or electric furnace to melt ingredients such as sand, soda, potash, borax and broken glass for making the required type of glass articles
Feeding or directing the feeding of premixed ingredients to the furnace
Heating the furnace and maintaining the temperature at correct level with aid of instrument controls or by sight
Checking and ensuring that the melting process of the ingredients in the furnace pot is proceeding correctly and to the required consistency
Collecting samples of the molten glass for laboratory analysis
Maintaining a record of batches of mixture melted
Cleaning the melting pot periodically and examining furnace walls for worn spots and leaks
WORK ENVIRONMENT
It is a field job
Need not handle a team
Local travelling is not a part of this job
Part-time work and contractual jobs are available in some cities
Work from home option is not available
Working hours
Factories usually work for 6 days a week and 8/10 hours every day. This may vary from factory to factory
Shift system may be available