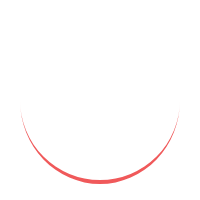
Gas welding is a versatile and widely used welding process that utilizes a flame generated by the combustion of a fuel gas and oxygen mixture. It is commonly used for joining metals and is preferred for its simplicity, portability, and cost-effectiveness. In this article, we will explore the various aspects of gas welding, including the types of processes, equipment required, safety measures, techniques, advantages, disadvantages, applications, and more.
Introduction to Gas Welding
Gas welding is a fusion welding process where the heat necessary for melting the base metal is produced by a flame obtained from the combustion of a fuel gas mixed with oxygen. The fuel gas can be acetylene, hydrogen, propane, or other gases, depending on the application and availability.
Gas welding is widely used in industries such as automotive, construction, metal fabrication, and repair. It allows for the joining of different metals and alloys, including steel, stainless steel, cast iron, aluminum, and copper.
Types of Gas Welding Processes
Oxy-Acetylene Welding
Oxy-acetylene welding, also known as oxy-fuel welding, is one of the most common gas welding processes. It uses a mixture of acetylene gas and oxygen to produce a high-temperature flame. This process is versatile and can be used for both fusion welding and brazing.
Oxy-Fuel Welding
Oxy-fuel welding is a general term that encompasses various gas welding processes using different fuel gases, such as acetylene, hydrogen, or propane. It is widely used for welding and cutting applications, providing a controlled and concentrated heat source.
Oxy-Hydrogen Welding
Oxy-hydrogen welding utilizes a mixture of hydrogen gas and oxygen to generate a high-temperature flame. This process is mainly used for specialized applications, such as jewelry making and electronics, where precise and clean welds are required.
Oxy-Propane Welding
Oxy-propane welding employs propane gas instead of acetylene or hydrogen. It offers similar characteristics to oxy-acetylene welding but with the advantage of a lower cost for fuel gas. Oxy-propane is commonly used for heating, brazing, and cutting operations.
Equipment Required for Gas Welding
To perform gas welding, certain equipment is essential. Here are the key components:
Gas Welding Torch
A gas welding torch is a handheld device that delivers the fuel gas and oxygen mixture to produce the welding flame. It consists of a handle, mixing chamber, and various nozzles or tips that control the flame characteristics.
Fuel Gas Supply
The fuel gas used in gas welding, such as acetylene, hydrogen, or propane, is stored in cylinders under pressure. The gas is then regulated and delivered to the torch through hoses.
Oxygen Supply
Oxygen is required to support the combustion of the fuel gas and create the high-temperature flame. It is also stored in cylinders and supplied to the torch through separate hoses and regulators.
Gas Cylinders
Gas cylinders are specially designed containers that store the fuel gas and oxygen. They need to be handled with care and stored in well-ventilated areas to prevent leaks and potential hazards.
Regulators and Gauges
Regulators and gauges are used to control and monitor the gas flow and pressure. They ensure a stable and consistent supply of fuel gas and oxygen, allowing for precise control during the welding process.
Safety Measures for Gas Welding
When working with gas welding, it is crucial to prioritize safety to prevent accidents and ensure a safe working environment. Here are some essential safety measures:
Proper Ventilation
Gas welding produces gases and fumes that can be hazardous if inhaled. Working in a well-ventilated area or using local exhaust ventilation systems helps remove harmful gases and ensures fresh air circulation.
Personal Protective Equipment (PPE)
Welders should wear appropriate personal protective equipment, including safety glasses, welding helmets with darkened lenses, fire-resistant clothing, gloves, and safety shoes. PPE provides protection against sparks, heat, UV radiation, and potential burns.
Fire Safety Precautions
Gas welding involves an open flame, making fire safety crucial. Keep a fire extinguisher nearby, remove flammable materials from the work area, and have a clear understanding of fire prevention and emergency procedures.
Handling Compressed Gas Cylinders
Cylinders containing fuel gas and oxygen are pressurized and require careful handling. Secure the cylinders upright, avoid dropping or mishandling them, and never tamper with valves or fittings. Use cylinder caps when not in use and follow proper storage guidelines.
Gas Welding Techniques
To successfully perform gas welding, several techniques need to be followed. Here is a step-by-step guide:
Setting up the Equipment: Ensure all the necessary equipment is assembled correctly and in good working condition. Connect the gas cylinders to the regulators, and attach the hoses to the torch.
Igniting the Torch: Open the fuel gas valve on the torch handle slightly and ignite the flame using a suitable ignition source, such as a spark lighter or a friction lighter.
Adjusting the Flame: Adjust the fuel gas and oxygen valves to achieve the desired flame characteristics. A neutral flame with a sharp inner cone and a surrounding feather is typically used for welding.
Starting the Welding Process: Clean the base metal surfaces to be welded and secure them in the desired position. Position the torch at the starting point of the weld joint and bring the flame close to the metal until it reaches the appropriate temperature.
Creating Weld Beads: Move the torch along the joint in a controlled manner, maintaining the desired flame shape and distance from the metal. Add filler metal, if necessary, to create a strong and continuous weld bead.
Advantages and Disadvantages of Gas Welding
Gas welding offers various advantages and disadvantages compared to other welding processes. Let's explore them:
Advantages
Portability: Gas welding equipment is relatively lightweight and portable, allowing for flexibility in different work environments.
Cost-Effective: Gas welding is generally more affordable compared to other welding methods, especially for small-scale operations.
Versatility: Gas welding can be used for joining a wide range of metals and alloys, making it versatile for various applications.
Easy to Learn: Gas welding is considered relatively easy to learn, making it accessible to beginners and DIY enthusiasts.
Disadvantages
Slower Welding Speed: Gas welding can be slower compared to other processes, particularly for thicker metals, due to lower heat input.
Limited Thickness Range: Gas welding may not be suitable for welding thicker sections of metal due to its lower heat output and penetration capabilities.
Skill-Dependent: Achieving high-quality welds in gas welding requires skill and practice to control the flame, heat input, and filler metal deposition effectively.
Applications of Gas Welding
Gas welding finds application in various industries and fields. Some common applications include:
Automotive Industry
Gas welding is used for repairs, fabrication, and customization of automotive components and structures. It is commonly employed for exhaust system repairs, bodywork, and fabrication of custom exhaust headers and roll cages.
Metal Fabrication
In metal fabrication, gas welding is utilized for joining different metal components to create structures and assemblies. It is commonly used for welding steel, stainless steel, and aluminum in applications such as construction, shipbuilding, and structural engineering.
Repair and Maintenance Work
Gas welding plays a vital role in repair and maintenance activities across different industries. It enables the repair of machinery, equipment, and infrastructure, ensuring their continued functionality and extending their service life.
Art and Sculpture
Gas welding offers artists and sculptors the flexibility to work with metal and create intricate and detailed pieces. It allows for precise control over the heat input, enabling the manipulation of metal to form artistic shapes and structures.
FAQs
Is gas welding suitable for all types of metals?
Gas welding can be used for various metals, including steel, stainless steel, cast iron, aluminum, and copper. However, the thickness and specific properties of the metal should be considered to determine its suitability for gas welding.
How does gas welding compare to electric arc welding?
Gas welding and electric arc welding are different processes. Gas welding uses a flame generated by the combustion of fuel gas and oxygen, while electric arc welding utilizes an electric arc to create the heat required for melting the metal.
Can gas welding be performed outdoors?
Gas welding can be performed outdoors; however, proper ventilation and wind conditions should be considered to ensure the safety of the welder and maintain the quality of the weld.
What safety precautions should I take when handling gas cylinders?
When handling gas cylinders, always ensure they are secured upright and stored in a well-ventilated area. Avoid dropping or mishandling them, and use protective caps when not in use. Follow proper guidelines for storing and transporting cylinders.
Are there any specialized applications for gas welding?
Gas welding has specialized applications in fields such as jewelry making and electronics. Oxy-hydrogen welding, in particular, is often used for precise and clean welds in these industries.