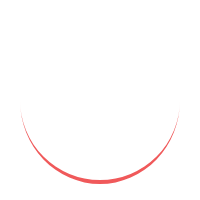
The potential for Water Jet Looms to transform the textile industry
Shuttle Less Looms have been an essential part of the textile industry for many years. They have revolutionized the production of fabrics and have greatly contributed to the industry's growth. However, with the emergence of Water Jet Looms, a new and more efficient alternative has been introduced.
Shuttle Less Loom Fitter - Water Jet Introduction
Shuttle Less Looms are looms that operate without a shuttle, unlike traditional looms. They use various mechanisms to interlace the weft threads into the warp threads. The Shuttle Less Looms' technology is more advanced than that of traditional looms, and they offer a range of benefits, including increased efficiency and productivity, reduced waste, and enhanced fabric quality and appearance.
Water Jet Looms, on the other hand, are a revolutionary alternative to Shuttle Less Looms. They use water jets to insert the weft threads into the warp threads. Water Jet Looms offer several advantages over Shuttle Less Looms, including increased efficiency, enhanced fabric quality, and reduced costs.
Shuttle Less Loom Fitter - Water Jet The Evolution of Shuttle Less Looms
Shuttle Less Looms were first introduced in the 1950s and have since undergone significant advancements in technology. Shuttle Less Looms come in various forms, including Projectile Looms, Rapier Looms, and Air Jet Looms. Shuttle Less Looms have become increasingly popular in the textile industry, and they are widely used in the production of various fabrics, including denim, silk, and cotton.
Shuttle Less Loom Fitter - Water Jet Water Jet Looms: A Revolutionary Alternative
Water Jet Looms are an innovative alternative to Shuttle Less Looms. They use a high-pressure water jet to insert the weft threads into the warp threads. Water Jet Looms offer several advantages over Shuttle Less Looms, including increased efficiency, enhanced fabric quality, and reduced costs. Water Jet Looms are also more energy-efficient than Shuttle Less Looms and produce less noise.
Water Jet Looms are also more efficient than Air Jet Looms. Air Jet Looms use compressed air to insert the weft threads into the warp threads, which can cause the yarn to break
Shuttle Less Loom Fitter - Water Jet The Advantages of Using Water Jet Looms
Water Jet Looms offer several advantages over traditional looms and Shuttle Less Looms. One of the most significant advantages is increased efficiency and productivity. Water Jet Looms can produce fabrics at a faster rate than traditional looms, resulting in higher productivity and faster delivery times.
Another advantage of Water Jet Looms is enhanced fabric quality and appearance. The high-pressure water jet used in Water Jet Looms ensures that the weft threads are accurately placed, resulting in a tighter weave and a smoother surface. This results in fabrics that are more durable, have better color fastness, and have a more consistent appearance.
Water Jet Looms also reduce costs and waste in the production process. The high-pressure water jet used in Water Jet Looms reduces the amount of yarn required to produce fabrics, resulting in less waste and lower costs. Water Jet Looms also require less energy than Shuttle Less Looms, resulting in lower energy costs.
Finally, Water Jet Looms are a more sustainable and environmentally-friendly option than traditional looms and Shuttle Less Looms. The reduction in yarn waste and energy consumption results in a lower carbon footprint and less pollution.
Shuttle Less Loom Fitter - Water Jet Implementing Water Jet Looms in Textile Manufacturing
Transitioning from traditional looms or Shuttle Less Looms to Water Jet Looms requires careful planning and consideration. Manufacturers must ensure that their Water Jet Loom operators are adequately trained to operate the new machinery. Additionally, maintenance and repair requirements for Water Jet Looms must be considered.
However, the benefits of Water Jet Looms make the transition worthwhile. Manufacturers who make the switch can significantly increase their productivity, reduce their costs, and improve their fabric quality and appearance.
Shuttle Less Loom Fitter - Water Jet The Future of Textile Manufacturing with Water Jet Looms
As the demand for high-quality fabrics continues to grow, the use of Water Jet Looms is expected to increase significantly. Advancements in Water Jet Loom technology are also expected, resulting in even more efficient and productive machinery.
The potential for Water Jet Looms to revolutionize the textile industry is significant. Water Jet Looms offer a more sustainable, cost-effective, and efficient option than traditional looms and Shuttle Less Looms.
Shuttle Less Loom Fitter - Water Jet FAQs:
What are Shuttle Less Looms?
Shuttle Less Looms are looms that operate without a shuttle, unlike traditional looms. They use various mechanisms to interlace the weft threads into the warp threads.
What are Water Jet Looms?
Water Jet Looms are looms that use a high-pressure water jet to insert the weft threads into the warp threads.
What are the advantages of using Water Jet Looms?
Water Jet Looms offer increased efficiency and productivity, enhanced fabric quality and appearance, reduced costs and waste, and a more sustainable production option.
Can Water Jet Looms be used for all types of fabrics?
Yes, Water Jet Looms can be used for a wide range of fabrics, including denim, silk, and cotton.
Are there any downsides to using Water Jet Looms?
While Water Jet Looms offer many advantages over traditional looms
Apologies for the mistake. Here is the continuation of the article:
While Water Jet Looms offer many advantages over traditional looms and Shuttle Less Looms, there are some downsides to consider. One of the primary downsides is the initial cost of purchasing Water Jet Looms, which can be higher than traditional looms. Additionally, maintenance and repair costs may also be higher due to the complexity of the machinery.
Another potential downside is the need for trained operators to operate the Water Jet Looms. Manufacturers may need to invest in training programs to ensure that their operators are proficient in operating the new machinery.
Overall, however, the advantages of Water Jet Looms far outweigh the downsides. As the textile industry continues to evolve, Water Jet Looms offer an innovative and efficient option for textile manufacturing that can lead to increased productivity, higher-quality fabrics, and a more sustainable production process.
Access All Amazing Prompts: https://bit.ly/Unlock_Prompts
Brief Job Description
A Fitter shuttle-less loom Water jet is a job role in a weaving department. The responsibility of Fitter Water jet loom is to maintain the loom efficiently so as to get maximum output with minimum defects given due importance to safety and environmental aspects
Personal Attributes
A shuttle-less loom Fitter Water jet should have good eyesight, eye-hand coordination, motor skills, and vision (including near vision distance vision, color vision, peripheral vision, depth perception and ability to change focus).
Scope
This unit/task covers the following:
Take charge of shift from Shuttle-Less Loom Fitter Water Jet
Handing over the shift to Shuttle-Less Loom Fitter Water Jet