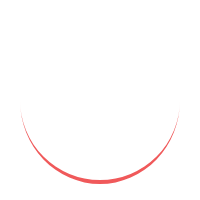
As businesses grow, so does the need for effective management. One of the key roles in any production environment is that of the line supervisor. Line supervisors play a vital role in ensuring the smooth running of operations, ensuring that targets are met, and that the workforce is working efficiently. In this article, we will take a closer look at the role of a line supervisor, the skills required, and the qualifications needed to become one.
Introduction: What is a Line Supervisor?
A line supervisor is a front-line manager who oversees production lines in manufacturing plants, warehouses, or any organization that requires efficient and timely production. They are responsible for the supervision of a team of workers, ensuring that their team meets production targets, quality standards, and safety regulations. Line supervisors play a critical role in coordinating and managing the production process, ensuring that the workforce is productive and motivated, and that the final product meets the required standards.
Responsibilities of a Line Supervisor
The responsibilities of a line supervisor include:
1. Supervising Workers
Line supervisors are responsible for supervising workers and ensuring they are meeting their production targets. They monitor the work of their team, ensuring that it is done correctly and according to established procedures.
2. Maintaining Equipment and Machinery
Line supervisors are responsible for ensuring that equipment and machinery are maintained and kept in good working order. This involves performing routine maintenance checks, repairs, and replacements when necessary.
3. Ensuring Compliance with Regulations
Line supervisors are responsible for ensuring that their team adheres to safety and quality regulations. They ensure that their team follows the proper procedures, and that the final product meets the required standards.
4. Managing Inventory
Line supervisors are responsible for managing inventory levels, ensuring that raw materials and finished products are available when needed. They work closely with the procurement department to ensure that inventory levels are maintained at optimal levels.
5. Managing Production Schedules
Line supervisors are responsible for managing production schedules, ensuring that production targets are met, and that the workforce is working efficiently. They work closely with the production planning department to ensure that production schedules are realistic and achievable.
6. Reporting to Senior Management
Line supervisors report to senior management on a regular basis, providing updates on production targets, quality standards, and safety regulations. They provide recommendations for improvements, and work closely with senior management to ensure that goals are met.
Skills Required to be a Line Supervisor
The skills required to be a line supervisor include:
1. Leadership Skills
Line supervisors must have strong leadership skills, as they are responsible for supervising a team of workers. They must be able to motivate and inspire their team to meet production targets and quality standards.
2. Communication Skills
Line supervisors must have strong communication skills, as they must communicate effectively with their team, senior management, and other departments. They must be able to provide clear instructions, feedback, and recommendations.
3. Technical Skills
Line supervisors must have technical skills related to the production process, including knowledge of machinery and equipment, production procedures, and quality standards.
Apologies for the confusion. Here is the continuation of the article:
4. Problem-Solving Skills
Line supervisors must have strong problem-solving skills, as they are responsible for identifying and resolving production-related issues. They must be able to think creatively and find effective solutions to problems that arise.
5. Time Management Skills
Line supervisors must have strong time management skills, as they are responsible for managing production schedules and ensuring that targets are met. They must be able to prioritize tasks and manage their time effectively to ensure that deadlines are met.
6. Organizational Skills
Line supervisors must have strong organizational skills, as they are responsible for managing inventory levels and ensuring that the production process runs smoothly. They must be able to manage multiple tasks and priorities effectively.
7. Interpersonal Skills
Line supervisors must have strong interpersonal skills, as they work closely with their team and other departments. They must be able to build strong relationships with their team and work collaboratively with others to achieve common goals.
Qualifications Needed to Become a Line Supervisor
The qualifications needed to become a line supervisor vary depending on the industry and organization. However, most organizations require a high school diploma or equivalent, as well as relevant work experience in the industry.
In addition, some organizations may require a bachelor's degree in a related field, such as business or engineering. Certifications, such as Six Sigma or Lean Manufacturing, may also be preferred by some organizations.
How to Become a Line Supervisor
To become a line supervisor, it is important to gain relevant work experience in the industry. This can be achieved by starting in an entry-level position, such as a production worker, and working your way up through the organization.
In addition, taking courses or certifications in leadership, communication, and technical skills can help prepare you for a career as a line supervisor. Networking with others in the industry and building strong relationships can also be beneficial.
Career Progression for Line Supervisors
Line supervisors can progress in their careers by gaining additional experience and education, as well as by taking on additional responsibilities within the organization. Some may move into management roles, such as production manager or plant manager, while others may specialize in a particular area, such as quality control or safety.
Challenges Faced by Line Supervisors
Line supervisors face a number of challenges in their roles. These include:
1. Meeting Production Targets
Line supervisors are responsible for ensuring that their team meets production targets. This can be challenging, particularly when production schedules are tight and unexpected issues arise.
2. Managing a Diverse Workforce
Line supervisors must manage a diverse workforce, which can include individuals from different backgrounds and with different skill sets. This can be challenging, particularly when it comes to communication and motivation.
3. Adhering to Regulations
Line supervisors must ensure that their team adheres to safety and quality regulations. This can be challenging, particularly when regulations change or are updated.
4. Managing Inventory
Line supervisors must manage inventory levels, ensuring that raw materials and finished products are available when needed. This can be challenging, particularly when demand is high or supply chain issues arise.
How to Overcome Common Challenges
To overcome common challenges faced by line supervisors, it is important to:
1. Communicate Effectively
Effective communication is key to overcoming challenges in any role. Line supervisors must communicate clearly and effectively with their team, senior management, and other departments.
2. Be Flexible
Flexibility is important when unexpected issues arise. Line supervisors must be able to adapt to changing circumstances and find creative solutions to problems.
3. Build Strong Relationships
Building strong relationships with team members and other departments can help overcome challenges. Line supervisors must work collaboratively with others to achieve common
goals and build trust and rapport with their team.
4. Stay Up-to-Date with Regulations
Line supervisors must stay up-to-date with safety and quality regulations to ensure that their team adheres to them. This can be achieved by attending training sessions, reading industry publications, and staying informed about changes and updates.
5. Develop Skills and Knowledge
Developing skills and knowledge in areas such as leadership, communication, and technical skills can help line supervisors overcome challenges and progress in their careers. This can be achieved through training programs, certifications, and networking opportunities.
Line Supervisor FAQs
What is the role of a line supervisor?
A line supervisor is responsible for overseeing production processes and ensuring that production targets are met.
What skills are needed to become a line supervisor?
Skills needed to become a line supervisor include leadership, communication, problem-solving, time management, organizational, and interpersonal skills.
What qualifications are needed to become a line supervisor?
Most organizations require a high school diploma or equivalent, as well as relevant work experience in the industry. Some organizations may also require a bachelor's degree in a related field, such as business or engineering.
What are some challenges faced by line supervisors?
Challenges faced by line supervisors include meeting production targets, managing a diverse workforce, adhering to regulations, and managing inventory.
How can line supervisors overcome common challenges?
Line supervisors can overcome common challenges by communicating effectively, being flexible, building strong relationships, staying up-to-date with regulations, and developing skills and knowledge in areas such as leadership, communication, and technical skills.
About Us Assembly line supervisor
An Assembly line supervisor oversees meeting operation as per the required norms. Assembly of factors consists of engines, transmission components, electrical and digital circuit and components, dashboards, seating system, wheels, doorways etc. and meeting of these aggregates in the cars at the required areas and as per required car type/ batch, deploying manpower as per requirement, guiding operatives and technicians to whole the assigned task, retaining a protected & wholesome working surroundings on the keep flooring and retaining data associated to production, rejections, cloth motion and manpower productiveness for a line/shift.
Line Supervisor Responsibilities and Duties
Monitor production lines operations to ensure that it complies with the quality and safety standards of the company.
Recommend improvements in quality processes and production procedures and equipment.
Provide proper trainings to staffs on their job duties.
Ensure each staff meets the assigned production targets daily.
Manage resource allocation including work station assignments, employee breaks and shift rotations to achieve assigned objectives.
Coordinate and manage shut downs, productions startups, and changeovers.
Manage proper staffing level daily by checking sick leaves, forecasted employee vacations and unanticipated absences.
Conduct shift meetings to ensure that staffs understand daily objectives and output requirements.
Follow Standard Operating Procedures (SOP) for operational efficiency.
Coordinate with Plant Manager and Shift Supervisor to address issues and safety concerns immediately.
Build safe, clean and positive working atmosphere.
Prepare daily production reports that will include output quality and quantity.