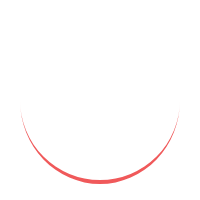
I. Introduction
In today's world, electroplating plays a crucial role in enhancing the appearance and durability of various objects. Whether it's adding a glossy finish to jewelry or protecting metal components from corrosion, electroplating operators are the skilled professionals responsible for ensuring the success of these processes. In this article, we will explore the world of electroplating operators, the training required to become one, and the job opportunities available in this field.
II. Role of an Electroplating Operator
Electroplating operators are individuals who specialize in applying a layer of metal onto the surface of an object through an electrochemical process. Their primary responsibility is to prepare the objects for plating, monitor the plating process, and ensure the quality and adherence of the plated metal. They work with a variety of metals, such as gold, silver, nickel, and copper, depending on the desired outcome. Attention to detail, precision, and knowledge of chemicals and equipment are crucial for this role.
III. Training and Certification
To become a competent electroplating operator, a diploma in electroplating operator is highly recommended. This specialized diploma program provides comprehensive training on the electroplating process, safety protocols, troubleshooting techniques, and the proper use of equipment. The duration of the program may vary, but it typically ranges from six months to a year.
During the course, students learn about different plating techniques, such as rack plating, barrel plating, and continuous plating. They gain practical experience in handling chemicals, analyzing plating thickness, and performing quality control tests. Moreover, the diploma program emphasizes the importance of environmental sustainability and encourages students to adopt eco-friendly practices.
IV. Diploma in Electroplating Operator Job Opportunities
After completing a diploma in electroplating operator, individuals can explore diverse career opportunities. Electroplating operators are in demand across various industries, including automotive, aerospace, jewelry manufacturing, and electronics. They can work in plating laboratories, metal fabrication plants, or specialized plating shops. With experience and expertise, they can advance to supervisory or managerial roles.
V. Electroplating Process
The electroplating process involves several steps to ensure the successful deposition of metal onto the object's surface. Firstly, the object is thoroughly cleaned and prepared to remove any impurities. It is then immersed in a chemical solution containing the desired metal ions. An electrical current is passed through the solution, causing the metal ions to bond with the object's surface. The duration of the plating process depends on the desired thickness of the metal layer.
To facilitate the electroplating process, operators use various tools and equipment such as rectifiers, plating tanks, and temperature controllers. They carefully monitor the parameters, including voltage, current, temperature, and plating time, to achieve the desired plating quality.
VI. Safety Precautions
Safety is paramount in the electroplating industry due to the presence of hazardous chemicals and electrical equipment. Electroplating operators must adhere to strict safety protocols to protect themselves and prevent accidents. They should wear appropriate personal protective equipment (PPE), including gloves, goggles, and aprons, to minimize exposure to chemicals.
Additionally, proper ventilation systems should be in place to prevent the buildup of fumes. Operators should also be trained in emergency response procedures and be aware of the potential hazards associated with the chemicals they handle.
VII. Troubleshooting
During the electroplating process, operators may encounter various challenges. Common issues include poor adhesion, uneven plating, and blistering. To overcome these problems, operators need to possess troubleshooting skills and a deep understanding of the plating process.
By carefully analyzing the conditions, operators can identify the root cause of the problem and implement appropriate corrective measures. This may involve adjusting the voltage, modifying the plating solution composition, or improving the cleaning process. Regular maintenance of equipment is also essential to avoid operational issues.
VIII. Advancements in Electroplating
The field of electroplating is continuously evolving, with advancements in technology and techniques. Automation and digitization have revolutionized the industry, enabling precise control over the plating process and reducing human error. Automated systems can optimize parameters such as plating thickness, current density, and temperature, resulting in consistent and high-quality plating.
Furthermore, advancements in nanotechnology have opened up new possibilities for electroplating. Nanoscale plating offers enhanced performance characteristics, such as increased hardness and resistance to wear. It finds applications in industries like electronics and medical devices, where miniature components require precise plating.
IX. Environmental Considerations
While electroplating brings numerous benefits, it is important to address its potential impact on the environment. Efforts are being made to develop sustainable electroplating practices that minimize the use of hazardous chemicals and reduce waste generation. Recycling and proper disposal of plating solutions are essential to prevent pollution.
Moreover, alternative plating techniques, such as electroless plating, are gaining prominence as they eliminate the need for electrical current and reduce energy consumption. Research and development in eco-friendly plating solutions are focused on achieving the desired plating results while minimizing environmental harm.
Diploma in Electroplating Operator FAQs
What is the average salary of an electroplating operator?
The average salary of an electroplating operator varies depending on factors such as location, experience, and industry. However, on average, electroplating operators can expect to earn a competitive salary ranging from $35,000 to $55,000 per year.
How long does it take to complete a diploma in electroplating operator?
The duration of a diploma in electroplating operator program typically ranges from six months to a year. However, the exact duration may vary depending on the educational institution and the curriculum.
Is prior experience required for this role?
While prior experience is not always a mandatory requirement, it can be advantageous in securing a job as an electroplating operator. Practical experience or apprenticeships in electroplating can provide valuable hands-on training and enhance job prospects.
Can I pursue a career in electroplating without a diploma?
While a diploma in electroplating operator is highly recommended for better job prospects and skills development, it is possible to enter the field without a diploma. However, acquiring relevant certifications or undergoing on-the-job training is essential to gain the necessary knowledge and skills.
What are the growth opportunities in this field?
Electroplating operators who continuously update their skills and stay informed about advancements in the field have ample opportunities for growth. They can progress to supervisory or managerial roles, specialize in niche plating techniques, or even establish their own electroplating businesses.