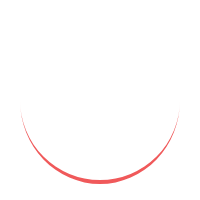
Valve applicators are versatile machines used in various industries for dispensing liquids or pastes in containers, bottles, or tubes. These machines come in different types, designs, and sizes, depending on the application and production needs. In this article, we will discuss everything you need to know about valve applicators, including their types, working principles, applications, advantages, maintenance, and more.
1. Valve Applicator Introduction
Valve applicators are machines that dispense liquids, creams, gels, or pastes into containers or packages accurately and consistently. They are used in various industries, such as cosmetics, pharmaceuticals, food and beverage, and chemical manufacturing, where precise dosing and filling are critical for product quality and safety. Valve applicators are efficient, reliable, and cost-effective solutions for high-volume production lines or small-scale operations.
2. Types of Valve Applicators
There are different types of valve applicators, each with its unique features and applications. The most common types are:
a. Piston Valve Applicators
Piston valve applicators use a piston and cylinder mechanism to control the flow of liquid or paste. They are suitable for high-viscosity products, such as adhesives, sealants, or greases, and can dispense a precise amount of material with a high degree of repeatability.
b. Diaphragm Valve Applicators
Diaphragm valve applicators use a flexible diaphragm to regulate the material flow. They are ideal for low to medium viscosity products, such as paints, inks, or lotions, and can handle abrasive or corrosive materials.
c. Needle Valve Applicators
Needle valve applicators use a needle or spout to dispense the material in drops or lines. They are perfect for small-scale operations or applications that require precise and controlled dispensing, such as soldering, lubrication, or marking.
3. Working Principle of Valve Applicators
Valve applicators work based on the principles of positive displacement, air pressure, or gravity feed. In positive displacement systems, the material is forced through a chamber or cylinder by a piston or diaphragm, and the flow is controlled by a valve or nozzle. In air pressure systems, the material is pushed by compressed air or gas, and the flow is regulated by a valve or nozzle. In gravity feed systems, the material flows naturally from a reservoir or hopper to the valve or nozzle, and the flow is adjusted by the opening or closing of the valve or nozzle.
4. Applications of Valve Applicators
Valve applicators have various applications in different industries, such as:
Dispensing adhesives, sealants, or coatings in automotive, construction, or electronics manufacturing
Filling bottles, jars, or tubes with creams, lotions, or gels in cosmetic or pharmaceutical production
Applying inks, dyes, or paints in printing, textile, or packaging industries
Dosing and mixing chemicals or additives in food and beverage or chemical manufacturing
Dispensing lubricants, solvents, or fuels in automotive, aerospace, or marine applications
5. Advantages of Valve Applicators (cont.)
semi-automatic dispensing methods, such as:
Increased production speed and efficiency: Valve applicators can dispense the material accurately and consistently at a high speed, reducing production time and labor costs.
Improved product quality and consistency: Valve applicators can control the material flow and volume precisely, ensuring the product's quality and consistency.
Reduced waste and material costs: Valve applicators can dispense the exact amount of material required, reducing waste and material costs.
Enhanced safety and hygiene: Valve applicators can prevent spillage, contamination, or exposure to hazardous materials, ensuring worker safety and product hygiene.
6. Factors to Consider When Choosing Valve Applicators
When selecting valve applicators, several factors should be considered, such as:
Type of material to be dispensed: Different types of valve applicators are suitable for specific materials, depending on their viscosity, texture, or chemical composition. Selecting the right valve applicator can ensure accurate and efficient dispensing.
Volume and speed of production: The production volume and speed can determine the type and size of valve applicators needed. High-volume production lines may require automatic valve applicators, while small-scale operations may benefit from manual or semi-automatic valve applicators.
Type of container or package: The size, shape, and material of the container or package can affect the valve applicator's compatibility and performance. Selecting the right valve applicator can ensure the proper filling and sealing of the container or package.
Cost and maintenance: The cost and maintenance of valve applicators can vary depending on the type, design, and manufacturer. Considering the initial investment, operating costs, and maintenance requirements can help select the most cost-effective and reliable valve applicator.
7. Maintenance of Valve Applicators
Proper maintenance of valve applicators can prolong their lifespan, ensure their performance, and prevent downtime or malfunctions. The maintenance procedures may vary depending on the type and manufacturer of valve applicators. However, some general maintenance practices include:
Regular cleaning of the valve, nozzle, and feed lines to prevent clogging or contamination.
Lubrication of moving parts and seals to reduce wear and tear and improve performance.
Inspection of the valve and parts for damage, leaks, or wear and replacing them if necessary.
Calibration of the valve and dispenser to ensure accurate and consistent dispensing.
8. Common Problems with Valve Applicators and Their Solutions
Despite their efficiency and reliability, valve applicators may encounter some problems or malfunctions, such as:
Clogging or blockage of the valve, nozzle, or feed lines due to dried material, debris, or contamination. The solution is to clean or replace the affected parts and prevent further contamination.
Inconsistent or inaccurate dispensing due to worn or damaged parts, incorrect calibration, or air pressure fluctuations. The solution is to inspect and replace the worn or damaged parts, recalibrate the valve and dispenser, and stabilize the air pressure.
Leakage or dripping of the material due to worn or damaged seals, incorrect valve adjustment, or overpressure. The solution is to replace the damaged seals, readjust the valve, and regulate the pressure.
10. Valve Applicator FAQs
What is a valve applicator?
A valve applicator is a machine that dispenses liquids, pastes, or creams into containers or packages
What types of valve applicators are available?
There are several types of valve applicators, such as manual, semi-automatic, and automatic, depending on the production volume and speed.
What materials can be dispensed using valve applicators?
Valve applicators can dispense various materials, such as adhesives, sealants, coatings, greases, and food products, depending on their viscosity, texture, or chemical composition.
How can I choose the right valve applicator for my application?
You should consider factors such as the type of material to be dispensed, volume and speed of production, type of container or package, and cost and maintenance when selecting a valve applicator.
How can I maintain my valve applicator?
You should regularly clean the valve, nozzle, and feed lines, lubricate the moving parts and seals, inspect the valve and parts for damage, leaks, or wear, and calibrate the valve and dispenser to ensure accurate and consistent dispensing.
Access All Amazing Prompts: https://bit.ly/Unlock_Prompts
About Us
A Valve Applicator is responsible for applying specified valves on green tubes