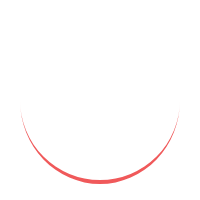
In the world of metalworking, cutting through iron and steel has never been easy. However, with the introduction of the plasma cutter, metalworkers have been able to slice through these materials like a knife through butter. In this article, we will explore everything you need to know about the plasma cutter and how it has revolutionized the world of metalworking.
1. Iron & Steel Plasma Cutter Introduction
When it comes to metalworking, cutting through iron and steel can be a challenging task. Traditional methods like sawing, grinding, and shearing are not only time-consuming but also produce a lot of heat and sparks, which can be dangerous. This is where the plasma cutter comes in - a tool that has revolutionized metal cutting.
2. What is a Plasma Cutter?
A plasma cutter is a cutting tool that uses a high-velocity jet of ionized gas (plasma) to cut through metal. The plasma is created by passing an electric arc through a gas such as nitrogen, oxygen, or argon, which then heats the gas to its plasma state. The plasma is then forced through a small nozzle at high speeds, creating a concentrated jet of hot plasma that melts and blows through the metal, cutting it cleanly.
3. How Does a Plasma Cutter Work?
The plasma cutter works by using an electric arc to ionize the gas, creating plasma, and directing it through the metal to be cut. The plasma jet is focused by a nozzle, which helps to create a high-velocity stream of plasma that can melt and cut through metal. The process is similar to a welding torch, but instead of welding two pieces of metal together, it cuts through them.
4. Different Types of Plasma Cutters
There are three main types of plasma cutters - manual, semi-automatic, and fully automatic. Manual plasma cutters are the most basic and require the operator to hold the torch and move it by hand. Semi-automatic plasma cutters use a machine to move the torch along a pre-determined path, while the operator controls the cutting speed. Fully automatic plasma cutters use a computer-controlled machine that moves the torch and adjusts the cutting speed and power, making them the most precise.
5. Benefits of Using a Plasma Cutter
There are several benefits to using a plasma cutter, including:
Speed: Plasma cutters are much faster than traditional metal cutting methods.
Precision: Plasma cutters are incredibly precise, making them ideal for intricate cuts.
Versatility: Plasma cutters can cut through a wide range of metals, including aluminum, stainless steel, and copper.
Clean cuts: Plasma cutters produce clean, smooth cuts that require minimal clean-up.
Cost-effective: Plasma cutters are relatively inexpensive and require little maintenance.
6. Safety Measures when Using a Plasma Cutter
Like any cutting tool, plasma cutters can be dangerous if not used properly. To stay safe when using a plasma cutter, you should:
Wear protective clothing, including a face shield, gloves, and apron.
Keep the work area clean and free of clutter.
Always ensure that the cutter
Always ensure that the cutter is grounded properly.
Never touch the metal being cut or the plasma torch while it is in operation.
Keep a fire extinguisher nearby in case of a fire.
Follow the manufacturer's instructions and safety guidelines.
7. Tips for Using a Plasma Cutter
To get the most out of your plasma cutter, consider these tips:
Use the correct gas and amperage settings for the metal being cut.
Keep the torch perpendicular to the metal being cut for a clean, straight cut.
Move the torch at a steady pace to avoid overheating the metal.
Use a guide or template to create precise cuts.
Allow the metal to cool before handling it.
Keep the torch clean and free of debris.
8. Maintenance and Care of a Plasma Cutter
To ensure that your plasma cutter performs at its best, regular maintenance is crucial. Some maintenance tasks include:
Regularly cleaning the torch and nozzle to prevent clogs.
Checking the gas and electrical connections for leaks or damage.
Inspecting the consumables (nozzle, electrode, and shield) for wear and tear.
Replacing worn-out consumables as needed.
Keeping the machine and work area clean and free of debris.
9. Best Plasma Cutters on the Market
There are many plasma cutters on the market, each with its own set of features and benefits. Some of the best plasma cutters include:
Hypertherm Powermax45 XP
Miller Spectrum 625 X-Treme
Lincoln Electric Tomahawk 375 Air
Hobart Airforce 27i
Everlast PowerPlasma 50S
10. How to Choose the Right Plasma Cutter for Your Needs
Choosing the right plasma cutter depends on several factors, including:
Type of metal being cut
Thickness of the metal
Cutting frequency
Portability needs
Budget
Consider these factors when choosing a plasma cutter to ensure that it meets your specific needs.
11. Plasma Cutter vs. Other Metal Cutting Tools
Plasma cutters have several advantages over other metal cutting tools, including:
Faster cutting speeds
More precise cuts
Cleaner cuts
Able to cut through thicker metal
More versatile
12. Common Applications of Plasma Cutting
Plasma cutting is used in a wide range of industries and applications, including:
Automotive repair and restoration
Metal fabrication
Construction
Industrial manufacturing
Art and sculpture
HVAC systems
13. Future of Plasma Cutting
As technology continues to advance, the future of plasma cutting looks bright. Advancements in computer-controlled plasma cutters and new materials that can be cut with plasma will continue to improve the precision and efficiency of plasma cutting.
15. Iron & Steel Plasma Cutter FAQs
Is plasma cutting dangerous?
Plasma cutting can be dangerous if not used properly, so it is important to follow safety guidelines.
What kind of gas is used in a plasma cutter?
A plasma cutter can use various gases, including nitrogen, oxygen, and argon.
How thick of metal can a plasma cutter cut?
Plasma cutters can cut through a range of thicknesses, depending on the cutter's power and amperage settings.
Can a plasma cutter cut aluminum?
Yes, a plasma cutter can cut through aluminum.
How much does a plasma cutter cost?
The cost of a plasma cutter
About Us
IRON & STEEL: PLASMA CUTTER
The job is all about reducing one-of-a-kind substances (mild carbon steel, stainless steel, aluminum, excessive tensile and distinctive steels, and different materials) in quite a number of profiles.This includes setting up and getting ready for operations decoding the proper statistics from the specification documents, acquiring the proper consumables and different materials, and so forth