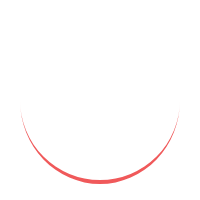
As the demand for accurate measurement and quality control continues to rise across industries, the need for qualified professionals to operate weighing equipment becomes more important than ever. The weighing operator is responsible for ensuring that products are weighed and measured accurately, with a high level of precision and attention to detail. In this article, we'll take a closer look at the role and responsibilities of a weighing operator, as well as the skills, qualifications, and training required to excel in this field.
Weighing Operator What is a Weighing Operator?
A weighing operator is a professional who operates and manages weighing equipment in various industries. These professionals are responsible for ensuring that weighing and measurement processes are accurate, efficient, and compliant with regulations and standards. Weighing operators work with a variety of weighing equipment, including scales, balances, and weighbridges, and may work in settings such as manufacturing plants, laboratories, or transportation facilities.
Responsibilities of a Weighing Operator
The primary responsibility of a weighing operator is to ensure that products are weighed accurately and consistently. This involves:
Calibrating weighing equipment to ensure accuracy
Measuring products and materials to determine weight and quantity
Recording and reporting measurements accurately
Performing routine maintenance and cleaning of weighing equipment
Troubleshooting and resolving issues with weighing equipment
Adhering to regulations and standards for weighing operations
Ensuring that products are weighed and measured safely and efficiently
Skills and Qualifications of a Weighing Operator
Weighing operators require a unique set of skills and qualifications to be successful in their role. Some of the most important skills for weighing operators include:
Attention to detail and accuracy
Strong analytical and problem-solving skills
Excellent communication and interpersonal skills
Basic computer literacy
Ability to work independently and in a team
Weighing Operator Physical dexterity and coordination
In terms of qualifications, most weighing operators have a high school diploma or equivalent, and may have completed vocational or technical training in weighing operations or a related field. Some employers may also require certifications or licenses for weighing operators, depending on the industry and the specific equipment being used.
Weighing Operator Training for Weighing Operators
Training for weighing operators can vary depending on the industry and the specific equipment being used. Some common training programs for weighing operators include:
On-the-job training: Many weighing operators receive training directly from their employer, which may involve shadowing experienced operators or participating in training sessions on weighing equipment and processes.
Vocational or technical training: Some schools offer vocational or technical training programs in weighing operations, which can provide a more structured and comprehensive approach to training.
Manufacturer training: Equipment manufacturers may offer training programs for their specific products, which can help operators learn the ins and outs of a particular piece of equipment.
Types of Weighing Equipment
Weighing operators work with a variety of weighing equipment, including:
Scales: These are the most common type of weighing equipment, and can range from small laboratory scales to large industrial scales used in manufacturing and transportation.
Balances: Balances are more precise than scales, and are commonly used in laboratory settings for measuring small quantities of
Weighing Operator materials.
Weighbridges: Weighbridges are large scales used to weigh vehicles, such as trucks or trains.
Load cells: Load cells are sensors that measure the weight of objects by detecting changes in electrical resistance.
Each type of weighing equipment has its own unique features, strengths, and limitations, and weighing operators must be familiar with the equipment they are working with in order to use it effectively.
Calibration and Maintenance of Weighing Equipment
To ensure accurate measurements, weighing equipment must be calibrated regularly. Calibration involves comparing the measurements of a weighing device to a known standard, and adjusting the device as necessary to ensure accuracy. Weighing operators are responsible for calibrating the equipment they use and keeping records of calibration activities.
In addition to calibration, weighing equipment must also be maintained regularly to ensure that it continues to function properly. This may involve cleaning the equipment, replacing worn or damaged parts, and troubleshooting issues as they arise.
Regulations and Standards for Weighing Operations
Weighing operations are subject to a variety of regulations and standards, depending on the industry and the equipment being used. Some of the most common regulations and standards for weighing operations include:
OIML: The International Organization of Legal Metrology (OIML) provides standards and guidelines for measurement and weighing equipment used in trade and commerce.
NIST Handbook 44: The National Institute of Standards and Technology (NIST) publishes Handbook 44, which provides guidelines and requirements for weighing and measuring devices used in the United States.
ISO 9001: The International Organization for Standardization (ISO) publishes standards for quality management, which can apply to weighing operations in various industries.
Weighing operators must be familiar with these regulations and standards, and ensure that their weighing operations are compliant with applicable requirements.
Safety Considerations for Weighing Operators
Weighing operations can involve a variety of hazards and risks, including exposure to chemicals, lifting heavy objects, and working with electrical equipment. Weighing operators must be trained in appropriate safety procedures and equipment to ensure that they can operate weighing equipment safely.
Some common safety considerations for weighing operators include:
Wearing appropriate personal protective equipment, such as gloves or safety glasses
Ensuring that the weighing area is well-ventilated and free of hazards
Following proper lifting techniques to avoid injury
Avoiding contact with electrical components or moving parts of weighing equipment
Challenges and Opportunities in Weighing Operations
Weighing operations can be complex and challenging, requiring attention to detail and a high level of precision. However, there are also many opportunities for weighing operators to advance in their careers and take on new challenges.
Some potential challenges and opportunities for weighing operators include:
Developing expertise in a specific type of weighing equipment or industry
Advancing to a supervisory or management role
Pursuing additional training or education to expand skills and knowledge
Exploring new applications for weighing technology in emerging industries, such as biotech or renewable energy
Industry Applications for Weighing Operators
Weighing operators are needed in a wide range of industries, including:
Manufacturing: Weighing operators in manufacturing settings are responsible for weighing raw materials and finished products to ensure consistency and quality.
Transportation: Weighing operators in transportation settings operate weighbridges to weigh vehicles and ensure that they are within legal weight limits.
Pharmaceuticals: Weighing operators in pharmaceutical settings measure and mix precise quantities of drugs and other ingredients to ensure product safety and efficacy.
Agriculture: Weighing operators in agriculture settings weigh crops, livestock, and other agricultural products to determine yield and quality.
Future Outlook for Weighing Operations
As industries continue to focus on quality control and efficiency, the demand for qualified weighing operators is expected to remain
strong. Additionally, advancements in weighing technology and data analysis are creating new opportunities for weighing operators to contribute to process optimization and product innovation.
One area of particular growth is in the field of industrial Internet of Things (IIoT) and smart weighing systems. These systems use sensors and data analysis to monitor and optimize production processes, and can help companies improve efficiency, reduce waste, and increase profitability. Weighing operators with experience in these systems will be in high demand as the IIoT continues to expand.
Weighing Operator FAQs
What kind of education or training is required to become a weighing operator?
The education and training requirements for weighing operators vary depending on the industry and the specific equipment being used. Some employers may require a high school diploma or equivalent, while others may prefer candidates with technical or vocational training.
What is the typical career path for a weighing operator?
Many weighing operators begin their careers in entry-level positions, such as material handler or quality control technician, and advance to more senior roles over time. Some may pursue additional education or training to specialize in a particular area or advance to a management position.
What are some of the most common types of weighing equipment used in industry?
Some common types of weighing equipment used in industry include scales, balances, load cells, and weighbridges.
What are some of the biggest challenges facing weighing operators today?
One of the biggest challenges facing weighing operators today is the need to keep up with advancements in technology and data analysis. Additionally, weighing operators may face safety risks or other hazards associated with their work.
What are some emerging trends in the field of weighing operations?
One emerging trend is the use of smart weighing systems and IIoT technology to optimize production processes and improve efficiency. Additionally, there is growing interest in the use of weighing technology in emerging industries such as biotech and renewable energy.
About Us
A weighing operator is responsible for weighing accurately ingredients, prepared mixes, semi-finished products and finished products as available at different stages of production.