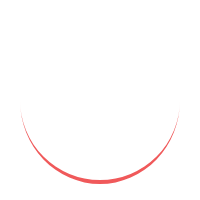
Article Outline
Introduction
What is Tie & Dye?
History of Tie & Dye
Techniques and Materials
Traditional Tie & Dye Techniques
Modern Tie & Dye Techniques
Materials Used in Tie & Dye
Applications of Tie & Dye
Fashion Industry
Home Decor
Textile Art
Tie & Dye Process Step by Step
Preparing the Fabric
Tying and Folding Techniques
Dyeing the Fabric
Setting the Colors
Unveiling the Design
Tips and Tricks for Successful Tie & Dye
Color Combinations
Design Placement
Dyeing Techniques
Fabric Selection
Maintenance and Care of Tie & Dye Items
Tie & Dye as a Business
Starting a Tie & Dye Business
Marketing and Selling Tie & Dye Products
Challenges and Opportunities
Conclusion
FAQs
Tie & Dye Technician
Tie & dye is a popular textile dyeing technique that involves creating unique and colorful patterns on fabric by tying, folding, or clamping it before applying dyes. This technique has a long history and has evolved over time, resulting in various methods and materials being used. In this article, we will explore the art of tie & dye, its techniques, applications, and the role of a tie & dye technician in creating stunning designs.
Tie & dye is a form of resist dyeing where certain areas of the fabric are prevented from absorbing the dye, creating patterns and designs. It is believed to have originated in ancient times, with evidence of tie & dye techniques found in cultures across the globe. Today, tie & dye is not only a traditional craft but also a contemporary fashion trend and a creative outlet for textile artists.
Tie & dye, also known as resist dyeing, is a technique that involves manipulating fabric to create patterns by preventing the dye from reaching certain areas. The fabric is folded, pleated, or tied with strings, rubber bands, or other materials before dyeing. The tied sections resist the dye, resulting in unique patterns and color combinations. The tie & dye technique can be applied to various types of fabrics, including cotton, silk, rayon, and more.
The art of tie & dye has a rich history that spans different cultures and time periods. It has been practiced for centuries in countries such as India, Japan, Indonesia, and Nigeria. In India, tie & dye is known as "Bandhani," and it has been a part of Indian textile traditions for thousands of years. In Japan, the technique is called "Shibori," and it has been used to create intricate patterns on kimonos and other garments.
Techniques and Materials
Traditional tie & dye techniques involve using simple tools and methods to create intricate designs. Some popular techniques include:
Knotting: This technique involves tying the fabric in knots using thread or rubber bands. The tied areas resist the dye, resulting in circular or irregular patterns.
Fold and Clamp: Fabric is folded in a specific pattern and then secured with clamps or blocks before dyeing. The clamped areas create unique geometric designs.
Twist and Bind: Sections of fabric are twisted tightly and then bound with string or rubber bands. The twisted sections resist the dye, creating spiral or marbled patterns.
Modern tie & dye techniques have expanded the possibilities of this art form. Some contemporary techniques include:
Spray Dyeing: Instead of immersing the fabric in a dye bath, the dye is sprayed onto the fabric using spray bottles or airbrushes. This technique allows for more control over color placement.
Ice Dyeing: The fabric is first soaked in soda ash solution and then placed on a rack or a tray covered with ice. Dye powder is sprinkled on top of the ice, which gradually melts and creates unique patterns as the dye spreads.
Ombre Dyeing: Ombre dyeing involves creating a gradient effect by gradually changing the intensity of the dye from light to dark or vice versa. This can be achieved by immersing the fabric partially in the dye bath or by applying the dye with a sponge or brush.
Tie & dye requires specific materials to achieve the desired results. Some essential materials include:
Fabric: Natural fibers like cotton, silk, and linen are ideal for tie & dye due to their absorbent nature. However, synthetic fabrics like rayon and polyester can also be used with the right dyes.
Dyes: Various types of dyes can be used for tie & dye, including fiber reactive dyes, acid dyes, and natural dyes. These dyes come in a wide range of colors and can be mixed to create custom shades.
Fixatives: Fixatives or mordants are used to set the dye and ensure colorfastness. Common fixatives include salt, vinegar, and soda ash, depending on the type of dye used.
Tools: Rubber bands, strings, clamps, and blocks are essential tools for creating different tie & dye techniques. Plastic squeeze bottles, spray bottles, and brushes are used for applying dyes.
Protective Gear: When working with dyes, it is important to wear protective gloves, aprons, and goggles to prevent skin and eye irritation.
Tie & dye has a wide range of applications in various industries and art forms. Some notable applications include:
Fashion Industry
Tie & dye has become a popular fashion trend, with designers incorporating tie & dye fabrics into their collections. From vibrant t-shirts and dresses to stylish scarves and accessories, tie & dye adds a unique and eye-catching element to fashion.
Home Decor
Tie & dye techniques can be applied to home decor items such as curtains, beddings, tablecloths, and pillow covers. These items can instantly transform a living space with their vibrant colors and intricate designs.
Textile Art
Tie & dye is also embraced by textile artists who use the technique to create one-of-a-kind artworks. From wall hangings and tapestries to wearable art pieces, tie & dye allows artists to explore their creativity and produce stunning textile masterpieces.
The tie & dye process involves several steps to achieve the desired results. Here is a step-by-step guide:
Preparing the Fabric: Start by washing and drying the fabric to remove any sizing or impurities. Pre-washing ensures better dye absorption.
Tying and Folding Techniques: Choose a tying or folding technique based on the desired pattern. Experiment with different methods like knots, pleats, or twists to create unique designs.
Dyeing the Fabric: Prepare the dye bath according to the instructions provided with the dye. Immerse the tied fabric in the dye and make sure it is fully saturated. Allow the fabric to sit in the dye for the recommended time.
Setting the Colors: After dyeing, follow the instructions to set the colors. This usually involves rinsing the fabric in cold water and soaking it in a fixative solution. The fixative helps the dye bond with the fibers and improves colorfastness.
Unveiling the Design: Once the fabric has been rinsed and dried, carefully remove the ties or folds to reveal the tie & dye pattern. Admire the unique design you have created!
To achieve the best results in tie & dye, consider the following tips and tricks:
Color Combinations: Experiment with different color combinations to create visually appealing designs. Consider contrasting colors for a bold look or analogous colors for a harmonious effect.
Design Placement: Plan the placement of your ties and folds strategically to create balanced and symmetrical patterns. Consider the overall composition and how the design will appear on the final fabric.
Dyeing Techniques: Explore various dyeing techniques like dip-dyeing, scrunching, or pouring to add texture and depth to your tie & dye creations.
Fabric Selection: Different fabrics absorb and hold dye differently. Consider the fabric's absorbency, texture, and weight when choosing the material for your tie & dye projects.
To maintain the vibrant colors and patterns of your tie & dye items, follow these care instructions:
Washing: Hand wash tie & dye items separately in cold water using a mild detergent. Avoid soaking for long periods or using harsh chemicals that can fade the colors.
Drying: Line dry your tie & dye items away from direct sunlight to prevent color fading. Avoid using a dryer, as the heat can damage the fabric and alter the colors.
Ironing: Iron your tie & dye items on a low heat setting, preferably on the reverse side or with a pressing cloth. Avoid ironing directly on the dyed areas to prevent color transfer.
If you are passionate about tie & dye and want to turn it into a business, here are some considerations:
Starting a Tie & Dye Business
Skills and Training: Hone your tie & dye skills by taking workshops, classes, or online courses. Practice different techniques and experiment with various materials to expand your knowledge.
Equipment and Supplies: Invest in high-quality equipment and materials for your tie & dye business. This includes dyes, fabrics, tying tools, and protective gear.
Workspace: Set up a dedicated workspace with proper ventilation and ample room for dyeing and drying fabrics. Ensure you have storage for your supplies and a comfortable area for creating designs.
Online Presence: Create a website or online store to showcase your tie & dye products. Use social media platforms to share your designs, process videos, and engage with potential customers.
Collaborations: Collaborate with local fashion designers, boutiques, or interior decorators to showcase and sell your tie & dye creations. Participate in craft fairs or markets to reach a wider audience.
Challenges and Opportunities
Starting a tie & dye business comes with its challenges and opportunities. Some challenges include competition in the market, sourcing quality materials, and maintaining consistent quality in your products. However, there is a growing demand for unique and handcrafted items, providing an opportunity for creative entrepreneurs to thrive.
Tie & dye is a captivating art form that allows individuals to express their creativity and create visually stunning designs on fabric. From its ancient origins to modern techniques, tie & dye continues to captivate artists, designers, and enthusiasts alike. Whether you want to explore tie & dye as a hobby or turn it into a business, the possibilities are endless. So grab your dyes, fabrics, and tying tools, and let your imagination run wild with this vibrant and versatile art form.
Q1: Can I use synthetic fabrics for tie & dye?
Yes, synthetic fabrics like rayon and polyester can be used for tie & dye. However, they may require different types of dyes and dyeing techniques compared to natural fibers.
Q2: Is tie & dye suitable for all types of clothing?
Tie & dye can be applied to various types of clothing, including t-shirts, dresses, scarves, and more. However, consider the fabric's texture and weight when choosing the tying and dyeing techniques.
Q3: How long does it take to complete a tie & dye project?
The time required to complete a tie & dye project depends on various factors, including the complexity of the design, the dyeing technique used, and the fabric's absorbency. It can range from a few hours to several days.
Q4: Can I achieve precise patterns with tie & dye?
While tie & dye is known for its organic and unpredictable patterns, you can still create more precise designs by using advanced folding, pleating, or clamping techniques.
Q5: Can I re-dye a tie & dye item if I'm not satisfied with the results?
Yes, you can re-dye a tie & dye item if you're not satisfied with the colors or patterns. Make sure to remove the ties or folds, rinse the fabric thoroughly, and start the dyeing process again with new colors or techniques.