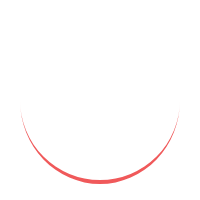
Fisheries feed manufacturing techniques play a crucial role in ensuring the growth, health, and productivity of fish in aquaculture systems. With the increasing demand for seafood and the decline of wild fish stocks, aquaculture has become an essential industry to meet global protein needs. As a result, the manufacturing of high-quality fisheries feed has gained significant importance. This article explores the various techniques involved in fisheries feed manufacturing, from ingredient selection to packaging, along with the challenges and advancements in the field.
Importance of Fisheries Feed Manufacturing
In aquaculture, the quality of the feed directly impacts the growth, health, and overall performance of fish. Well-formulated feeds provide essential nutrients, vitamins, and minerals necessary for the proper development of fish. By meeting their nutritional requirements, fisheries feed contributes to faster growth, enhanced immune system, and better resistance to diseases. Moreover, it ensures the efficient utilization of feed, reducing the environmental impact and optimizing the productivity of aquaculture operations.
Key Components of Fisheries Feed
Fisheries feed typically consists of several key components, including proteins, carbohydrates, lipids, vitamins, and minerals. Proteins, derived from various sources such as fishmeal, soybean meal, and poultry by-products, provide amino acids necessary for growth and tissue repair. Carbohydrates, often sourced from grains like corn and wheat, supply energy to fish. Lipids, such as fish oil and vegetable oils, are essential for maintaining cell integrity and hormone synthesis. Additionally, vitamins and minerals play vital roles in various metabolic processes and immune function.
Types of Fisheries Feed
Fisheries feed can be categorized into different types based on their physical properties and manufacturing processes. Understanding these types helps in selecting the most appropriate feed for different fish species and production systems
Pellet Feed
Pellet feed is one of the most common types of fisheries feed. It is produced by grinding and mixing the ingredients into a homogeneous mixture, which is then pelleted using a pellet mill. The pellets are compacted under high pressure and heat, resulting in a dense and durable feed form. Pellet feed offers high feed conversion efficiency, reduced wastage, and better control over nutrient content.
Extruded Feed
Extruded feed undergoes a different manufacturing process that involves heat, pressure, and moisture. The feed mixture is forced through an extruder, where it is subjected to high temperatures and pressure, resulting in gelatinization of starches and protein denaturation. The extruded feed has a unique texture and improved digestibility, making it suitable for species with specific feeding behaviors.
Moist Feed
Moist feed, as the name suggests, has a higher moisture content compared to other feed types. It is often used for feeding fish species that have difficulty consuming dry pellets or extruded feed. Moist feed is prepared by grinding the ingredients and mixing them with water, creating a semi-solid consistency. It provides a convenient option for hand-feeding or tank systems where water quality management is crucial.
Semi-Moist Feed
Semi-moist feed is a hybrid between dry pellets and moist feed. It offers the benefits of both feed types, combining the convenience of handling dry feed with the higher moisture content and palatability of moist feed. Semi-moist feed is typically produced by adding water to the feed mixture during the pelletizing or extrusion process, resulting in a slightly softer texture.
Floating Feed
Floating feed is designed to float on the water surface, targeting fish species that prefer to feed on or near the water surface. It is produced by incorporating buoyant materials or expanding agents during the manufacturing process. Floating feed ensures easy visual detection by fish, reduces feed waste and allows monitoring of feeding behavior.
Manufacturing Techniques for Fisheries Feed
The manufacturing of fisheries feed involves several sequential steps to ensure consistent quality and nutritional value. These techniques include ingredient selection and preparation, grinding and mixing, pelletizing or extrusion, drying and cooling, and coating and packaging.
Ingredient Selection and Preparation
The first step in fisheries feed manufacturing is the careful selection of high-quality ingredients. The ingredients should meet the nutritional requirements of the target fish species and be sourced from reputable suppliers. The raw materials undergo thorough quality control measures to ensure they are free from contaminants and meet specific standards. Once the ingredients are selected, they go through preparation processes such as grinding, sieving, and conditioning. Grinding reduces the particle size for better mixing and digestion, while sieving removes any impurities or oversized particles. Conditioning involves adding moisture to improve the pelletizing or extrusion process.
Grinding and Mixing
After preparation, the ingredients are weighed and mixed according to the feed formulation. Grinding ensures uniform particle size distribution, facilitating optimal nutrient absorption by the fish. Mixing is carried out in specialized mixers, ensuring the ingredients are evenly distributed to avoid nutrient imbalances. The mixing time and speed are carefully controlled to achieve a homogeneous mixture.
Pelletizing or Extrusion
The next step involves transforming the feed mixture into the desired feed form. Pelletizing and extrusion are the two main techniques used in fisheries feed manufacturing. In pelletizing, the feed mixture is compressed through a die with small holes, creating cylindrical pellets of specific sizes. The pellets are formed under high pressure and heat, which gelatinizes the starches and proteins, resulting in a stable feed form. The pellets are then cut to the desired length and cooled before further processing. Extrusion involves passing the feed mixture through an extruder, which consists of a barrel, screws, and a die. The feed undergoes high temperatures and pressure as it moves through the extruder, causing the starches to expand and proteins to denature. The extruded feed is then cut into desired shapes and sizes before being cooled.
Drying and Cooling
After the pelletizing or extrusion process, the feed needs to be dried and cooled to remove excess moisture and stabilize its physical properties. Drying is typically done in a specialized dryer, where heated air is circulated through the pellets or extrudates, reducing the moisture content to the desired level. Cooling is then carried out to prevent the feed from clumping and ensure proper storage stability.
Coating and Packaging
In some cases, coatings may be applied to the feed pellets or extrudates to enhance palatability, improve nutrient retention, or provide additional protection. Coatings can be made from fats, oils, vitamins, or other bioactive compounds.
Finally, the processed feed is packaged in appropriate containers, such as bags or bulk containers, ensuring proper storage and transportation. Proper packaging materials are used to protect the feed from moisture, light, and physical damage.
Quality Control in Fisheries Feed Manufacturing
Maintaining consistent quality in fisheries feed manufacturing is crucial to ensure the health and performance of fish. Several quality control measures are implemented throughout the manufacturing process.
Proximate Analysis
Proximate analysis is conducted to determine the nutritional composition of the feed, including protein, fat, carbohydrate, fiber, moisture, and ash content. This analysis helps to ensure that the feed formulation meets the nutritional requirements of the target fish species.
Physical Properties Evaluation
Physical properties of the feed, such as pellet durability, size distribution, and water stability, are evaluated to assess the feed's handling characteristics and its ability to withstand water conditions without disintegrating. This evaluation helps optimize feed performance and reduce wastage.
Palatability and Digestibility Testing
Palatability testing is conducted to assess the feed's taste and acceptability to fish. Digestibility trials are also carried out to determine the feed's nutrient utilization and digestibility by fish. Both tests provide valuable insights into the feed's performance and suitability for different fish species.
Microbial Testing
Microbial testing is performed to ensure the feed's safety and hygiene. It involves analyzing the feed for the presence of harmful microorganisms, such as bacteria, molds, and yeasts. Stringent microbial control measures are implemented to prevent the contamination of feed and the transmission of diseases to fish.
Advancements in Fisheries Feed Manufacturing
The field of fisheries feed manufacturing has witnessed significant advancements in recent years, aiming to improve the nutritional value, sustainability, and efficiency of feed production.
Nutritional Optimization
Researchers and feed manufacturers are continuously exploring ways to optimize the nutritional composition of fisheries feed. This includes identifying alternative protein sources, improving amino acid profiles, and enhancing the bioavailability of nutrients. By tailoring the feed formulation to meet the specific nutritional requirements of different fish species at various growth stages, feed efficiency and fish performance can be maximized.
Feed Additives and Supplements
The use of feed additives and supplements has become prevalent in fisheries feed manufacturing. These additives include vitamins, minerals, enzymes, probiotics, prebiotics, and immunostimulants. They are added to the feed formulation to enhance nutrient utilization, improve digestion, boost immune function, and promote overall fish health. Feed additives also play a crucial role in reducing the environmental impact of aquaculture by minimizing the excretion of nutrients into the surrounding ecosystem.
Sustainable Manufacturing Practices
Sustainability is a key focus in modern fisheries feed manufacturing. Efforts are being made to reduce the reliance on fishmeal and fish oil, which are limited resources and can contribute to overfishing. Alternative protein sources, such as plant-based proteins, insect meal, and single-cell protein, are being incorporated into feed formulations. Additionally, energy-efficient manufacturing processes, waste management strategies, and responsible sourcing of raw materials are being implemented to minimize the environmental footprint of feed production.
Challenges and Solutions in Fisheries Feed Manufacturing
Fisheries feed manufacturing faces several challenges that require innovative solutions to ensure sustainable and efficient production.
Sourcing of Raw Materials
The availability and cost of raw materials, particularly fishmeal and fish oil, pose challenges to feed manufacturers. Increasing demand for seafood and limited fish stocks have led to higher prices and the need to find suitable alternatives. Research is focused on identifying and utilizing alternative protein sources and sustainable feed ingredients to reduce reliance on marine resources.
Feed Conversion Efficiency
Feed conversion efficiency (FCE) is a critical parameter in aquaculture, measuring how efficiently fish convert feed into body mass. Improving FCE is essential to reduce feed costs, minimize waste, and optimize fish growth. Researchers are studying the factors influencing FCE, including feed composition, feed processing techniques, and fish genetics, to develop strategies for improving feed efficiency.
Environmental Impact
Fisheries feed manufacturing can have environmental implications, such as nutrient runoff, water pollution, and habitat degradation. To mitigate these impacts, feed manufacturers are adopting sustainable practices, such as optimizing feed formulations to reduce nutrient excretion, implementing waste management strategies, and developing eco-friendly packaging materials. Integration of aquaculture with other farming systems, such as using aquaponics to recycle nutrients, is also being explored.
Waste Management
Efficient waste management is crucial in fisheries feed manufacturing to minimize the environmental impact and comply with regulatory requirements. Strategies such as anaerobic digestion, composting, and utilization of by-products from other industries help in reducing waste and recovering valuable resources. Recycling and reusing water in the manufacturing process further contribute to sustainable waste management.
Future Trends in Fisheries Feed Manufacturing
The future of fisheries feed manufacturing holds promising developments that will revolutionize the industry.
Advancements in feed formulation technologies, such as the use of artificial intelligence and precision nutrition, will enable more precise and tailored feed formulations for different fish species. Nutrigenomics, the study of how nutrients interact with genes, will provide insights into individual fish requirements and enable personalized feed formulations.
Innovative feed ingredients, such as insect meal, single-cell protein, and microalgae, will become increasingly prevalent in feed formulations. These alternative protein sources offer sustainable and nutrient-rich options, reducing reliance on fishmeal and fish oil.
Digitalization and automation will streamline feed manufacturing processes, improving efficiency, traceability, and quality control. Real-time monitoring systems, IoT integration, and data analytics will enable better feed management and decision-making.
The integration of circular economy principles in fisheries feed manufacturing will gain prominence. By optimizing resource utilization, reducing waste, and recycling by-products, the industry will move towards a more sustainable and environmentally friendly approach.
In summary, fisheries feed manufacturing techniques are vital for the success of aquaculture operations. The selection and preparation of ingredients, grinding and mixing, pelletizing or extrusion, drying and cooling, and coating and packaging are key steps in the process. Quality control measures ensure consistent feed quality and nutritional value. Advancements in nutritional optimization, feed additives, and sustainable practices contribute to improved feed performance and environmental sustainability. Despite challenges such as raw material sourcing and environmental impact, the industry is moving towards innovative solutions and future trends that will shape the future of fisheries feed manufacturing.
FAQs Fisheries Feed Manufacturing
What is the role of fisheries feed in aquaculture?
Fisheries feed is essential in aquaculture as it provides the necessary nutrients for the growth, health, and performance of fish. It ensures efficient feed utilization, enhances immune function, and supports the overall development of fish in aquaculture systems.
What are the different types of fisheries feed?
The different types of fisheries feed include pellet feed, extruded feed, moist feed, semi-moist feed, and floating feed. These feed types vary in their physical properties, manufacturing processes, and suitability for different fish species and culture systems.
How is the quality of fisheries feed ensured?
The quality of fisheries feed is ensured through proximate analysis, physical properties evaluation, palatability and digestibility testing, and microbial testing. These quality control measures assess the nutritional composition, physical characteristics, acceptability, digestibility, and safety of the feed.
What are the challenges in fisheries feed manufacturing?
Challenges in fisheries feed manufacturing include sourcing raw materials, improving feed conversion efficiency, managing environmental impact, and implementing efficient waste management strategies. These challenges require innovative solutions to ensure sustainable and efficient feed production.
What are the future trends in fisheries feed manufacturing?
Future trends in fisheries feed manufacturing include advancements in feed formulation technologies, innovative feed ingredients, digitalization and automation, and the integration of circular economy principles. These trends aim to optimize feed formulations, enhance sustainability, improve manufacturing processes, and reduce environmental impact.