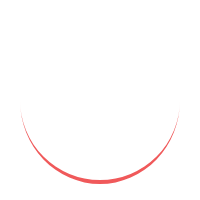
Sheet metal works and tinkering are essential processes in various industries that involve the shaping, cutting, and forming of sheet metal to create a wide range of products. From automotive to construction and aerospace to HVAC, sheet metal works play a crucial role in manufacturing and fabricating components used in different applications. This article will explore the world of sheet metal works, its history, applications, tools, skills required, the process involved, benefits, challenges, safety measures, and future trends.
Introduction
Sheet metal works refer to the manipulation of thin sheets of metal, typically less than 6mm in thickness, to create various structures and components. Tinkering, on the other hand, involves experimenting, repairing, and modifying existing sheet metal products or structures. Both processes require skilled artisans who can work with precision and attention to detail.
What is Sheet Metal Works and Tinkering?
Sheet metal works encompass a broad range of activities, including cutting, bending, welding, and assembling sheet metal to create products such as enclosures, chassis, brackets, ductwork, and more. Tinkering, on the other hand, involves working with existing sheet metal structures or products, either for repair or modification purposes. Both processes require expertise in handling and manipulating sheet metal.
The History of Sheet Metal Works and Tinkering
Sheet metal works have a rich history dating back thousands of years. Ancient civilizations like the Egyptians and Mesopotamians were known to use sheet metal for various purposes, including jewelry, weapons, and decorative items. Over time, sheet metal works evolved, and the industrial revolution brought significant advancements in the field. With the advent of machines and new technologies, sheet metal fabrication became more efficient and precise.
Applications and Industries
Sheet metal works find applications in a wide range of industries. Some notable industries where sheet metal works are indispensable include:
Automotive
The automotive industry relies heavily on sheet metal works for manufacturing car bodies, chassis, engine components, and exhaust systems. The ability to shape and mold sheet metal allows the creation of complex structures required in modern vehicles.
Construction
In the construction industry, sheet metal works are crucial for fabricating structural elements, roofing systems, gutters, and HVAC ductwork. Sheet metal's durability and versatility make it a popular choice for various construction applications.
Aerospace
Sheet metal works play a vital role in the aerospace industry, where lightweight yet strong components are required. Aircraft bodies, wings, engine parts, and even satellites often rely on sheet metal fabrication techniques.
HVAC
Heating, ventilation, and air conditioning (HVAC) systems extensively use sheet metal works for ducting, ventilation, and exhaust systems. The ability to create customized ductwork ensures efficient airflow and temperature control in buildings.
Tools and Equipment Used in Sheet Metal Works
Sheet metal works require a range of specialized tools and equipment to cut, shape, and join sheet metal. Some common tools used in sheet metal works include:
Shears and snips for cutting
Brake press for bending and folding
Rollers for curving and shaping
Welding equipment for joining metal pieces
Deburring tools for removing sharp edges
Skills Required for Sheet Metal Works
Sheet metal works demand a set of specialized skills. A sheet metal worker should possess:
Proficiency in reading and interpreting technical drawings and blueprints
Knowledge of different types of metals and their properties
Precision and attention to detail for accurate measurements and cuts
Proficiency in using various tools and equipment
Problem-solving skills to overcome challenges during fabrication
Understanding of safety protocols and procedures
The Process of Sheet Metal Works
Sheet metal works involve several stages and processes. The typical workflow includes:
Designing and Drafting
The process begins with designing the desired product using computer-aided design (CAD) software. The design is then translated into technical drawings and blueprints, specifying dimensions and material specifications.
Cutting and Shearing
The next step involves cutting the sheet metal to the required size and shape. This can be done using shears, snips, or laser cutting machines, depending on the complexity and precision needed.
Forming and Shaping
Sheet metal can be formed and shaped using various techniques such as bending, rolling, curving, and stamping. This stage requires specialized tools like brake presses and rollers.
Joining and Welding
To assemble the fabricated parts, sheet metal workers use welding techniques like TIG (Tungsten Inert Gas) or MIG (Metal Inert Gas) welding. This ensures the components are securely joined together.
Finishing and Surface Treatment
After the assembly, the fabricated product undergoes finishing processes to remove sharp edges, smoothen surfaces, and enhance the appearance. Surface treatment techniques like painting, powder coating, or anodizing may also be employed.
Benefits of Sheet Metal Works
Sheet metal works offer several advantages:
Versatility: Sheet metal can be manipulated into various shapes and sizes, making it suitable for a wide range of applications.
Strength and Durability: Sheet metal is known for its strength and durability, ensuring long-lasting products.
Customization: Sheet metal works allow for customization, enabling the creation of unique and tailored solutions.
Efficiency: With the right equipment and skills, sheet metal fabrication can be a fast and efficient process.
Cost-effectiveness: Sheet metal is a cost-effective material, and the fabrication process can be optimized for efficiency, leading to cost savings.
Challenges in Sheet Metal Works
Sheet metal works come with their share of challenges:
Precision and Accuracy: Achieving precise measurements and cuts requires expertise and attention to detail.
Material Considerations: Different types of metals have unique properties and behaviors, requiring careful selection and handling.
Complex Designs: Some projects involve intricate designs and shapes, which can be challenging to fabricate accurately.
Safety Risks: Working with metal and machinery poses safety risks, and sheet metal workers need to follow proper safety protocols.
Safety Measures in Sheet Metal Works
Safety is paramount in sheet metal works. Some essential safety measures include:
Wearing personal protective equipment (PPE) such as gloves, goggles, and helmets
Ensuring proper ventilation in the workspace to prevent exposure to harmful fumes
Regular equipment maintenance and inspections to ensure safe operation
Training employees on safe handling of tools, machinery, and materials
Adhering to local regulations and standards for occupational safety
Future Trends in Sheet Metal Works
The field of sheet metal works continues to evolve with advancements in technology. Some future trends to watch out for include:
Automation: The adoption of robotics and automation in sheet metal fabrication processes for increased efficiency and precision.
3D Printing: The integration of 3D printing technologies with sheet metal fabrication, allowing for more complex and customized designs.
Sustainable Practices: The use of environmentally friendly materials and processes to minimize waste and reduce the carbon footprint.
Digitalization: The utilization of digital tools and software for streamlined design, communication, and workflow management.
FAQs
Are sheet metal works only limited to industrial applications?
No, sheet metal works find applications in both industrial and residential settings. From automotive to HVAC systems, sheet metal is used in various sectors.
Is sheet metal expensive compared to other materials?
Sheet metal can be cost-effective due to its durability and recyclability. It provides long-term value for many applications.
Do I need specialized training to work with sheet metal?
While formal training and apprenticeships can provide a solid foundation, sheet metal works can also be learned through hands-on experience and continuous learning.
Can I use sheet metal for outdoor applications?
Yes, sheet metal is commonly used for outdoor applications as it can withstand various weather conditions and is resistant to corrosion when treated.
What are some emerging technologies in sheet metal works?
Emerging technologies include automation, 3D printing, and digitalization, which are enhancing efficiency, customization, and sustainability in the field of sheet metal works.