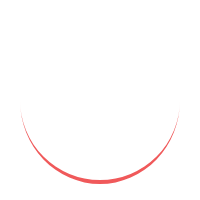
Forklifts play a vital role in material handling operations across various industries. These powerful machines efficiently lift and transport heavy loads, making them indispensable in warehouses, construction sites, and manufacturing facilities. However, operating and maintaining forklifts require careful attention to ensure safety, maximize productivity, and prolong the lifespan of the equipment.
Introduction
What is a forklift?
A forklift, also known as a lift truck, is a powered industrial truck designed to lift, carry, and stack heavy loads. It consists of a mast, an overhead guard, and forks for handling pallets or materials. Forklifts are commonly used to move goods over short distances, both indoors and outdoors.
Importance of forklift operation and maintenance
Effective forklift operation and maintenance are essential for several reasons. Firstly, proper operation ensures the safety of operators and those working in close proximity to forklifts. Additionally, regular maintenance enhances the equipment's performance, reduces the risk of breakdowns, and extends its lifespan. This article will delve into the intricacies of forklift operation and maintenance to provide valuable insights for operators and stakeholders.
Forklift Types and Components
Different types of forklifts
Forklifts come in various types, each designed for specific applications. Common types include counterbalance forklifts, reach trucks, pallet jacks, and order pickers. Counterbalance forklifts are the most widely used and feature a weight at the back to counterbalance the load being lifted.
Key components of a forklift
Understanding the main components of a forklift is crucial for both operators and maintenance personnel. These components include the mast, carriage, forks, hydraulic system, tires, and the power source (typically an internal combustion engine or an electric motor). Each component plays a vital role in the overall functionality and safety of the forklift.
Forklift Operation
Pre-operational checks
Before operating a forklift, it is essential to conduct thorough pre-operational checks. These checks include inspecting the tires, brakes, steering, lights, and horn. It is also crucial to ensure proper fluid levels and check for any leaks. By performing these checks, operators can identify and rectify potential issues that may compromise safety and performance.
Safe driving practices
Safe driving practices are paramount in forklift operation. Operators should be aware of their surroundings, maintain proper visibility, and adhere to speed limits. They should also ensure proper load placement and secure loads to prevent accidents or damage. Obeying traffic signs, using designated pedestrian walkways, and avoiding abrupt maneuvers are essential for safe operation.
Loading and unloading techniques
Efficient loading and unloading techniques are crucial for minimizing the risk of accidents and damage. Operators should ensure the load is evenly distributed, within the forklift's capacity, and properly secured. They should also consider factors such as load height, stability, and clearance to avoid collisions or tip-overs. Adhering to proper loading and unloading procedures promotes safety and protects the goods being handled.
Forklift Maintenance
Regular inspections
Regular inspections are key to identifying and addressing potential issues before they escalate. Operators should conduct visual inspections at the start of each shift, checking for visible damage, leaks, and loose components. Additionally, scheduled maintenance inspections carried out by trained technicians are vital for comprehensive assessments and preventive maintenance.
Fluid checks and replacements
Maintaining appropriate fluid levels is crucial for optimal forklift performance. Operators should regularly check and replenish fluids such as engine oil, coolant, hydraulic fluid, and brake fluid. Following manufacturer guidelines for fluid specifications and change intervals ensures proper lubrication, cooling, and braking, extending the life of the forklift.
Battery maintenance
For electric forklifts, battery maintenance is essential for smooth operation and prolonged battery life. Operators should follow charging guidelines, check battery connections for tightness and corrosion, and monitor battery water levels. Implementing proper battery maintenance practices prevents unexpected downtime and ensures optimal performance.
Forklift Safety
Importance of safety protocols
Safety should be a top priority in forklift operations. Establishing and enforcing safety protocols helps minimize accidents, injuries, and property damage. These protocols should include speed limits, traffic management plans, pedestrian safety measures, and guidelines for working at height. Regular safety training and communication among all stakeholders contribute to a safe working environment.
Personal protective equipment (PPE)
Wearing appropriate personal protective equipment (PPE) is crucial for forklift operators. PPE such as safety helmets, high-visibility vests, steel-toed boots, and safety glasses protect operators from potential hazards, including falling objects, collisions, and debris. Ensuring the availability and proper use of PPE promotes a culture of safety and mitigates risks.
Common safety hazards and how to avoid them
Forklift operations entail several safety hazards, including tip-overs, collisions, and falling loads. To prevent such incidents, operators should be trained on hazard identification and avoidance. Implementing measures like clear signage, designated traffic routes, and restricted areas can minimize risks. Regular risk assessments and continuous safety improvement initiatives are essential for a safe working environment.
Forklift Training and Certification
Importance of proper training
Proper training is crucial for forklift operators to acquire the necessary skills and knowledge. Training programs should cover equipment operation, safety procedures, load handling techniques, and emergency protocols. Comprehensive training ensures operators understand the nuances of forklift operation and are equipped to handle potential challenges safely.
Certification requirements
Certification is often required to operate forklifts legally. Regulations may vary by jurisdiction, but certifications typically involve both theoretical and practical assessments. Employers should ensure their operators hold valid certifications and provide opportunities for ongoing training and skill development.
Ongoing training and refresher courses
Forklift technology and safety practices continue to evolve, making ongoing training essential. Refresher courses and periodic evaluations help operators stay up to date with the latest industry standards and best practices. Continuous learning fosters competency and reinforces safe and efficient forklift operation.
Forklift Efficiency and Productivity
Optimizing fuel consumption
Efficient fuel consumption not only reduces operating costs but also minimizes environmental impact. Operators can optimize fuel consumption by avoiding unnecessary idling, practicing smooth acceleration and deceleration, and properly maintaining the forklift's engine. Regular tune-ups and adherence to manufacturer recommendations for fuel types and grades contribute to fuel efficiency.
Proper load handling techniques
Proper load handling techniques enhance productivity while minimizing the risk of accidents or damage. Operators should assess load weights, dimensions, and stability to determine appropriate lifting methods. Utilizing attachments like clamps, rotators, or sideshifters can improve efficiency and versatility. Training operators on efficient load handling techniques leads to increased productivity and reduced operational costs.
Maintenance schedules for maximum uptime
Adhering to recommended maintenance schedules is crucial for maximizing forklift uptime. Regular maintenance, including oil changes, filter replacements, and component inspections, prevents unexpected breakdowns and ensures equipment reliability. Employing computerized maintenance management systems (CMMS) can help track maintenance tasks and schedule them efficiently.
Common Forklift Issues and Troubleshooting
Identifying common issues
Understanding common forklift issues empowers operators to recognize and address them promptly. Issues such as engine misfires, hydraulic leaks, steering problems, and electrical malfunctions can disrupt operations and compromise safety. Operators should be vigilant in identifying signs of potential issues and report them to maintenance personnel.
Troubleshooting techniques
Basic troubleshooting techniques can help resolve minor forklift issues quickly. These techniques may include checking fluid levels, inspecting fuses and electrical connections, and verifying fuel supply. Operators should follow manufacturer guidelines and receive proper training on troubleshooting procedures. It is essential to exercise caution and seek professional assistance for complex issues.
When to seek professional help
While some issues can be resolved internally, others require professional intervention. Major mechanical failures, complex electrical problems, and structural damage should be addressed by trained technicians. Engaging qualified service providers ensures thorough diagnostics, repairs, and adherence to manufacturer specifications.
Forklift Technologies and Innovations
Advancements in forklift technology
Forklift technology continues to evolve, bringing advancements that enhance efficiency, safety, and sustainability. Technologies like advanced driver assistance systems (ADAS), telematics, and fleet management software improve operational visibility and facilitate data-driven decision-making. Staying informed about emerging technologies helps businesses leverage these innovations to optimize their material handling operations.
Automated and electric forklifts
Automation and electrification are transforming the forklift industry. Automated forklifts, guided by sensors, cameras, and artificial intelligence, offer increased efficiency and productivity while reducing the need for manual labor. Electric forklifts, with their zero-emission profiles and reduced noise levels, are gaining popularity as environmentally friendly alternatives to internal combustion engine-powered forklifts.
Integration with warehouse management systems
Integrating forklifts with warehouse management systems (WMS) streamlines operations and enhances productivity. WMS integration enables real-time inventory tracking, optimized routing, and efficient task allocation. The seamless flow of information between forklifts and WMS improves efficiency, reduces errors, and supports data-driven decision-making.
Environmental Considerations
Forklift emissions and environmental impact
Internal combustion engine-powered forklifts contribute to emissions and environmental pollution. The combustion of fuel releases carbon monoxide (CO), nitrogen oxides (NOx), and particulate matter (PM). Organizations committed to sustainability should explore alternatives like electric forklifts or fuel-cell-powered models, which produce zero-emissions during operation.
Eco-friendly alternatives and practices
To minimize environmental impact, organizations can adopt eco-friendly alternatives and practices. This includes implementing energy-efficient technologies, exploring renewable energy sources for charging electric forklifts, and promoting recycling programs for batteries and other components. Evaluating the entire lifecycle of forklifts, including manufacturing, usage, and disposal, helps identify opportunities for reducing the environmental footprint.
FAQs
How often should forklift operators conduct pre-operational checks?
Forklift operators should conduct pre-operational checks at the start of each shift to ensure the equipment is in proper working condition.
Are there any specific requirements for forklift certification?
Certification requirements for forklift operators may vary by jurisdiction, but they typically involve both theoretical and practical assessments to ensure competency in operating the equipment safely.
Can forklifts be operated outdoors as well?
Yes, forklifts can be operated both indoors and outdoors, depending on the type of forklift and the specific operational requirements.
What is the recommended maintenance schedule for forklifts?
The recommended maintenance schedule for forklifts varies based on factors such as usage, operating conditions, and manufacturer guidelines. Regular inspections, fluid checks, and scheduled maintenance tasks should be performed as outlined in the equipment's manual.
How can I optimize fuel consumption in my forklift fleet?
To optimize fuel consumption, operators should practice efficient driving techniques, minimize idle time, and ensure regular maintenance of the forklifts' engines. Additionally, transitioning to electric forklifts or exploring alternative fuel options can significantly reduce fuel consumption and emissions.