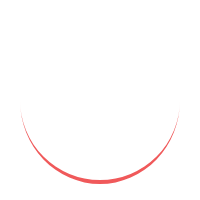
From the advent of the industrial revolution to the technological advancements of the present day, manufacturing processes have undergone significant transformations. One such groundbreaking innovation that has emerged in recent years is Additive Manufacturing (AM). In this article, we will explore the world of AM, its importance, advantages, applications, working principles, materials used, limitations, and the exciting future it holds.
1. Introduction
In today's fast-paced world, where customization, efficiency, and sustainability are paramount, traditional manufacturing methods face limitations. AM, also known as 3D printing, offers a solution that has the potential to revolutionize the way we design, produce, and distribute products.
2. What is AM?
AM refers to the process of creating three-dimensional objects by adding material layer by layer. Unlike subtractive manufacturing methods that involve cutting or drilling away material from a solid block, AM builds objects from the ground up. It utilizes computer-aided design (CAD) models and specialized machines to create complex geometries with precision.
3. The Importance of AM
AM presents numerous advantages over traditional manufacturing methods, making it a crucial technology in various industries. It allows for the creation of highly customized products, reduces waste through optimized material usage, enables rapid prototyping, and facilitates on-demand production. These factors contribute to shorter lead times, cost savings, and improved sustainability.
4. Advantages of AM
4.1 Design Freedom and Customization
AM enables the production of intricate designs and complex geometries that were previously challenging or impossible to manufacture. Designers can push boundaries, creating products with improved functionality and aesthetics. Additionally, customization is a key advantage of AM, allowing products to be tailored to individual requirements.
4.2 Waste Reduction and Material Efficiency
Traditional manufacturing processes often result in significant material waste due to cutting or machining excess material. AM minimizes waste by adding material only where it is needed, reducing the overall environmental impact of manufacturing.
4.3 Rapid Prototyping and Iteration
With AM, the time and cost associated with creating prototypes are significantly reduced. Designers and engineers can quickly produce physical prototypes, evaluate their performance, and make necessary modifications. This accelerated iteration process improves product development cycles and helps bring products to market faster.
5. Applications of AM
The versatility of AM has led to its adoption in diverse industries. Here are a few notable applications:
5.1 Healthcare and Biomedical
AM has revolutionized the medical field by enabling the production of patient-specific implants, prosthetics, and anatomical models for surgical planning. Customized medical devices enhance patient outcomes and improve the efficiency of treatments.
5.2 Aerospace and Automotive
In the aerospace and automotive industries, AM has transformed manufacturing processes. It allows for the production of lightweight components with complex internal structures, reducing weight and improving fuel efficiency. Rapid prototyping and on-demand spare part production are also vital applications.
5.3 Architecture and Construction
AM has opened new horizons in architecture and construction. It facilitates the creation of intricate and unique structures, enables faster and more cost-effective building techniques, and promotes sustainable construction practices through optimized material usage.
6. How Does AM Work?
The AM process involves several key steps:
Designing the object using CAD software.
Converting the design into a printable file format, such as STL (Standard Tessellation Language).
Preparing the printer by calibrating settings and selecting appropriate materials.
Layer-by-layer printing of the object, guided by the CAD model.
Post-processing, which may include removing support structures, surface finishing, and any necessary treatments or coatings.
7. Materials Used in AM
AM utilizes a wide range of materials, including polymers, metals, ceramics, composites, and even biological materials. The selection of material depends on the specific application, desired properties of the final product, and the capabilities of the AM technology being used.
8. Limitations of AM
While AM offers numerous advantages, it also has certain limitations that should be considered. These include limited material options for certain applications, lower production speeds compared to traditional methods for large-scale production, and challenges in achieving consistent quality across different machines and processes.
9. Future of AM
The future of AM is filled with possibilities. Ongoing research and development aim to overcome current limitations and expand the capabilities of AM further. Improved material options, increased production speeds, enhanced automation, and integration with other advanced technologies like artificial intelligence and robotics are some of the exciting directions AM is heading towards.
AM Conclusion
AM has emerged as a game-changer in the manufacturing industry, offering unprecedented design freedom, customization, waste reduction, and rapid prototyping capabilities. Its applications span across various sectors, and its potential for the future is immense. As AM continues to evolve and mature, it holds the promise of transforming how we create and consume products. Embracing this technology is key to unlocking new opportunities and staying competitive in a rapidly evolving global market.
AM FAQs
1. Is AM the same as 3D printing?
Yes, AM is often used interchangeably with 3D printing. AM encompasses various technologies that build objects layer by layer, and 3D printing is one of the most widely known and used methods.
2.What are the main advantages of AM?
AM offers design freedom, customization, waste reduction, rapid prototyping, and on-demand production, leading to shorter lead times, cost savings, and improved sustainability.
3. Can AM be used in the medical field?
Yes, AM has revolutionized healthcare by enabling the production of patient-specific implants, prosthetics, and anatomical models for surgical planning.
4. Are there any limitations to AM?
AM has limitations, including limited material options for certain applications, lower production speeds for large-scale production, and challenges in achieving consistent quality across different machines and processes.
5. What does the future hold for AM?
The future of AM looks promising, with ongoing research and development focused on improving material options, production speeds, automation, and integration with other advanced technologies like artificial intelligence and robotics.