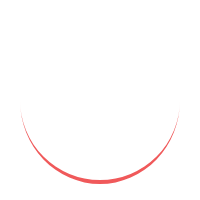
Tube splicing is an essential process in industries like automotive, aerospace, and construction. It involves joining two or more tubes using a variety of methods such as welding, brazing, and adhesive bonding. The person responsible for performing this critical task is known as a tube splicing operator. In this article, we'll explore what it takes to become a successful tube splicing operator, the skills and training required, and the tools and techniques used in this profession.
1. Tube Splicing Operator Introduction
Tube splicing is an essential process that involves joining two or more tubes to create a longer or more complex system. This process is critical in industries like aerospace, automotive, and construction, where the quality of tube splicing can affect the performance and safety of the end product. A tube splicing operator is responsible for performing this task and ensuring that the joint is strong, durable, and meets the required specifications.
2. Tube Splicing Operator What is Tube Splicing?
Tube splicing is the process of joining two or more tubes together to create a longer or more complex system. The purpose of tube splicing can vary from one application to another. For example, in automotive industries, tube splicing is used to create exhaust systems, while in aerospace, it's used to create fuel lines.
3. Tube Splicing Operator Types of Tube Splicing Techniques
There are several methods used for tube splicing, and the selection of a particular technique depends on the materials, application, and the required strength of the joint. The most common tube splicing techniques are:
Tube Splicing Operator Welding
Welding is the most common technique used for tube splicing. It involves heating the tubes to their melting point and then joining them together by applying pressure. The most common types of welding used in tube splicing are MIG, TIG, and Stick welding.
Tube Splicing Operator Brazing
Brazing is a technique used to join two or more tubes using a filler metal that has a lower melting point than the tubes. The filler metal is heated until it melts and flows into the joint, creating a strong and durable bond.
Tube Splicing Operator Adhesive Bonding
Adhesive bonding is a technique used to join two or more tubes using an adhesive. The adhesive is applied to the surface of the tubes, and then the tubes are pressed together. This technique is commonly used for lightweight and non-structural applications.
Tube Splicing Operator Mechanical Joining
Mechanical joining is a technique used to join two or more tubes using mechanical fasteners like nuts and bolts. This technique is commonly used for temporary or non-permanent joints.
4. The Role of a Tube Splicing Operator
A tube splicing operator is responsible for performing the critical task of joining two or more tubes to create a longer or more complex system. The operator must ensure that the joint is strong, durable, and meets the required specifications. In addition to performing the splicing operation, the operator is also responsible for inspecting the joint to ensure that it meets the quality standards.
5. Skills Required for Tube Splicing Operator
The job of a tube splicing operator requires a combination of technical and soft skills. Some of the essential
skills required for a tube splicing operator include:
Tube Splicing Operator Technical Skills
Knowledge of tube splicing techniques, tools, and equipment
Understanding of materials and their properties
Ability to read and interpret technical drawings and specifications
Familiarity with welding codes and standards
Tube Splicing Operator Soft Skills
Attention to detail and accuracy
Good communication skills
Problem-solving skills
Ability to work in a team environment
Adaptability and flexibility
6. Training and Education for Tube Splicing Operator
To become a tube splicing operator, you will typically need a high school diploma or equivalent. Some employers may require additional education or training, such as a certificate or associate degree in welding technology or a related field.
In addition to formal education, a tube splicing operator must also undergo on-the-job training to learn the specific techniques, tools, and equipment used by their employer.
7. Tools and Equipment Used by Tube Splicing Operator
The tools and equipment used by a tube splicing operator will depend on the splicing technique being used. Some of the most common tools and equipment used in tube splicing include:
Welding machines and accessories
Brazing torches and filler metal
Adhesives and applicators
Mechanical fasteners like nuts and bolts
Tube cutters and grinders
Inspection and testing equipment
8. Safety Measures for Tube Splicing Operator
Tube splicing can be a hazardous operation if proper safety measures are not followed. Some of the most critical safety measures for tube splicing operators include:
Wearing appropriate personal protective equipment (PPE), including eye protection, welding gloves, and respiratory protection
Ensuring proper ventilation in the workspace to prevent exposure to fumes and gases
Following proper handling and storage procedures for materials and equipment
Regular maintenance and inspection of equipment to ensure safe operation
9. Tube Splicing Operator Quality Control and Inspection
Quality control and inspection are essential in tube splicing to ensure that the joint meets the required specifications and is safe and reliable. Some of the common methods used for quality control and inspection in tube splicing include:
Visual inspection of the joint
Non-destructive testing (NDT) techniques like X-ray and ultrasonic testing
Pressure and leak testing
Mechanical testing, such as tensile and compression testing
10. Career Opportunities for Tube Splicing Operator
There is a growing demand for tube splicing operators in industries like automotive, aerospace, and construction. The job outlook for tube splicing operators is expected to be favorable, with a projected growth rate of 3% from 2020 to 2030.
11.Tube Splicing Operator Future of Tube Splicing Industry
The tube splicing industry is expected to see continued growth in the future, driven by increasing demand for lightweight and fuel-efficient components in industries like automotive and aerospace. Technological advancements in materials and splicing techniques are also expected to drive innovation in this field.
12. Challenges Faced by Tube Splicing Operator
Some of the common challenges faced by tube splicing operators include:
Exposure to hazardous materials and working conditions
Precision and accuracy required in splicing operations
Constant changes in materials and techniques used in the industry
Pressure to meet production deadlines while maintaining quality standards
13. Tube Splicing Operator FAQs
What is the salary range for a tube splicing operator?
The average salary for a tube splicing operator is around $43,000 per year, but this can vary depending on factors such as experience, location, and employer.
What type of materials can be spliced using tube splicing techniques?
Tube splicing techniques can be used to join
various types of materials, including metals, plastics, and composites.
What are some of the most common splicing techniques used by tube splicing operators?
Some of the most common splicing techniques used by tube splicing operators include welding, brazing, and adhesive bonding.
What is the job outlook for tube splicing operators?
The job outlook for tube splicing operators is expected to be favorable, with a projected growth rate of 3% from 2020 to 2030.
What are some of the safety measures that tube splicing operators must follow?
Tube splicing operators must follow several safety measures, including wearing appropriate personal protective equipment, ensuring proper ventilation, and following proper handling and storage procedures for materials and equipment.
Access All Amazing Prompts: https://bit.ly/Unlock_Prompts
About Us
A Tube Splice Operator work on splicing the ends of green tubes with valve in place to form a circular green tube ready for curing
JOB DESCRIPTION
Checking the width of tubes to be spliced against specification
Making a trial joint on tubes to check the splice for weak spots, open joints and dog ears
Rechecking the machine set points and performing clamps conduct checks again
Commencing continuous splicing once splice is of good quality
Managing rubberized clamps in order of tube sizes
Informing the Supervisor about poor/worn out or damaged rubberized clamps
Ensuring that the splicer temperature and pressure settings are as per the settings provided by technical
Applying specified cement at the ends where dog ear usually appears
Inspecting tube splice quality and finding possible solutions in case of poor quality
WORK ENVIRONMENT
It needs one to be on their toes
Need not handle a team
Local traveling maybe a part of this job role
Part-time work and contractual jobs may be available in some cities
Work from home option is not available