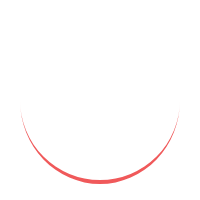
Introduction
Forklifts are essential heavy machines used in various industries for material handling and logistics purposes. These versatile vehicles provide a convenient solution for lifting, moving, and transporting heavy loads in warehouses, construction sites, manufacturing facilities, and more. To ensure optimal performance, safety, and longevity of forklifts, proper operation and maintenance practices are crucial. In this article, we will explore the key aspects of operating and maintaining forklifts efficiently.
Understanding Forklift Machines
Forklifts, also known as lift trucks or powered industrial trucks, are motorized vehicles equipped with forks or attachments that allow them to lift, carry, and stack loads. They come in various sizes and configurations to suit different applications. Forklifts use hydraulic systems to raise and lower the forks, enabling operators to maneuver heavy materials with ease. These machines are designed to be operated both indoors and outdoors, offering flexibility in different working environments.
Importance of Operation and Maintenance
Proper operation and maintenance of forklifts are vital for several reasons. Firstly, efficient operation ensures the safety of operators and other personnel working in the vicinity. Forklift accidents can lead to severe injuries, property damage, and even fatalities. Secondly, well-maintained forklifts are more reliable, reducing the risk of breakdowns and costly repairs. Regular maintenance enhances the performance and lifespan of the machines, optimizing productivity in the workplace.
Safety Measures for Operating Forklifts
Operating a forklift requires strict adherence to safety protocols. Here are some crucial safety measures to follow:
Wear appropriate personal protective equipment (PPE) such as hard hats, safety shoes, and high-visibility vests.
Conduct a thorough pre-operational inspection to ensure the forklift is in proper working condition.
Follow designated traffic routes and speed limits within the facility.
Maintain clear visibility by removing obstructions and adjusting mirrors.
Keep a safe distance from pedestrians and other vehicles.
Use horns, alarms, and warning signals when necessary.
Do not carry loads exceeding the specified capacity of the forklift.
Avoid sudden stops, starts, and sharp turns to prevent tip-overs.
Lower the forks and engage the parking brake when leaving the forklift unattended.
Only trained and authorized personnel should operate forklifts.
Preparing for Forklift Operation
Before operating a forklift, it is essential to follow certain preparatory steps:
Check the fuel or battery level and ensure it is sufficient for the intended duration of operation.
Inspect the tires for any damage or excessive wear.
Adjust the seat, mirrors, and controls to fit the operator comfortably.
Fasten the seatbelt and ensure all safety features are functional.
Familiarize yourself with the controls, including the steering, lifting, and tilting mechanisms.
Essential Forklift Maintenance Tasks
Regular maintenance plays a crucial role in maximizing the performance and longevity of forklifts. Here are some essential maintenance tasks:
Keep the forklift clean by regularly washing the exterior and removing debris from the working parts.
Lubricate the moving components, such as chains, pulleys, and bearings, as recommended by the manufacturer.
Check and replace engine oil, hydraulic fluid, and other fluids according to the maintenance schedule.
Inspect and tighten loose bolts, nuts, and fasteners.
Monitor tire pressure and tread wear regularly.
Clean or replace air filters to ensure proper engine performance.
Regularly inspect the brakes, steering, lights, and horn to ensure they are in good working condition.
Schedule regular professional inspections and servicing by qualified technicians.
Daily Inspection Checklist
Performing a daily inspection before each shift helps identify any potential issues or defects. Use the following checklist:
Check for any visible damage, leaks, or worn-out parts.
Test the brakes, including the parking brake, for effectiveness.
Inspect the tires for proper inflation, tread condition, and any signs of damage.
Ensure all lights, indicators, and alarms are functioning correctly.
Examine the forks, mast, and hydraulic system for any signs of wear or leaks.
Verify that the seatbelt, mirrors, and other safety features are in good working order.
Test the horn and backup alarm.
Confirm that the fire extinguisher and other emergency equipment are present and functional.
Handling Fuel and Batteries
Forklifts can be powered by either internal combustion engines or electric batteries. Proper handling of fuel or batteries is essential for safety and performance.
For internal combustion forklifts:
Refuel in designated areas with proper ventilation.
Turn off the engine before refueling.
Use the appropriate fuel type recommended by the manufacturer.
For electric forklifts:
Follow battery charging guidelines provided by the manufacturer.
Ensure the battery is properly connected and secured.
Avoid overcharging or deep discharging the battery.
Proper Loading and Unloading Techniques
Loading and unloading materials require specific techniques to ensure stability and safety. Here are some best practices:
Assess the weight and dimensions of the load to determine the appropriate forklift and attachments.
Position the forklift correctly, ensuring stability and maintaining a level surface.
Center the load on the forks and tilt them slightly back for better balance.
Drive slowly and smoothly, avoiding sudden stops or movements.
Use pallets, straps, or attachments to secure the load.
When unloading, ensure the area is clear and free from obstacles.
Operating Forklifts in Different Environments
Forklifts can operate in various environments, each with its unique challenges. Here are some considerations for different settings:
Indoor environments: Pay attention to overhead obstacles, low clearance areas, and floor conditions.
Outdoor environments: Be cautious of uneven terrain, potholes, and inclement weather conditions.
Hazardous environments: Follow all safety guidelines and regulations for operating in hazardous areas.
Cold storage facilities: Take extra precautions for battery-powered forklifts in low-temperature environments.
Common Forklift Operational Challenges
Operating a forklift may present certain challenges. Here are some common issues and tips for overcoming them:
Limited visibility: Use additional mirrors, spotter assistance, or proximity warning devices to enhance visibility.
Narrow aisles: Practice maneuvering techniques and use specialized narrow aisle forklifts if required.
Uneven surfaces: Drive slowly and carefully, adjusting the forklift's speed and tilt as necessary.
Obstacles and obstructions: Clear the path and avoid driving over loose debris or objects.
Pedestrian interaction: Always prioritize pedestrian safety and communicate effectively with hand signals or horns.
Troubleshooting and Basic Repairs
While regular maintenance minimizes breakdowns, occasional troubleshooting and basic repairs may be necessary. Some common issues include:
Engine starting problems: Check the battery, fuel level, and ignition system.
Hydraulic system issues: Inspect for leaks, damaged hoses, or low fluid levels.
Braking problems: Ensure the brakes are adjusted correctly and inspect the brake components.
Electrical system malfunctions: Check the fuses, wiring, and connections.
Tire-related issues: Inspect for punctures, wear, or improper inflation.
For complex repairs or issues, consult a qualified technician or the manufacturer's support team.
Forklift Training and Certification
To operate a forklift safely and efficiently, proper training and certification are necessary. Training programs cover essential topics such as:
Forklift operation techniques
Safety guidelines and regulations
Hazard recognition and prevention
Load handling and stability principles
Maintenance and inspection procedures
Obtaining a forklift operator certification ensures compliance with legal requirements and enhances the operator's skills and knowledge.
Benefits of Regular Maintenance
Regular maintenance offers several benefits for forklift operators and businesses:
Increased safety: Well-maintained forklifts minimize the risk of accidents and injuries.
Improved performance: Regular maintenance enhances efficiency and productivity.
Extended lifespan: Proper care extends the lifespan of the forklift, reducing the need for premature replacements.
Cost savings: Preventive maintenance reduces the likelihood of expensive repairs or downtime due to breakdowns.
Compliance with regulations: Adhering to maintenance schedules ensures compliance with safety and environmental regulations.
FAQs
How often should a forklift undergo maintenance?
Regular maintenance intervals vary depending on factors such as usage, environment, and manufacturer recommendations. However, a general guideline is to schedule maintenance every 200-250 hours of operation or quarterly.
Can anyone operate a forklift without training?
No. Operating a forklift without proper training and certification is both illegal and highly dangerous. Training programs educate operators about safety measures, regulations, and best practices for efficient forklift operation.
Are forklifts suitable for outdoor use?
Yes, forklifts can be used in outdoor environments. However, operators must take into account factors such as uneven terrain, weather conditions, and potential obstacles. Outdoor forklifts may require additional features for enhanced durability and performance.
What should I do if I encounter an issue with the forklift during operation?
If you encounter an issue while operating a forklift, follow the company's established procedures for reporting malfunctions. It is crucial to cease operation, secure the area, and notify the appropriate personnel to ensure the issue is addressed promptly.
Can forklift maintenance be performed in-house, or should it be outsourced?
Both options are viable depending on the resources and expertise available within the organization. Some companies choose to perform basic maintenance tasks in-house and outsource more complex repairs to professional technicians. Others prefer to rely entirely on external service providers for maintenance and repairs.