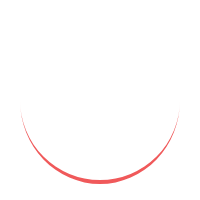
In today's highly advanced manufacturing industries, wire bonding plays a vital role in the assembly of electronic components. As technology continues to advance, the demand for skilled wire bonding operators is on the rise. In this article, we will explore the responsibilities, skills, and challenges faced by wire bonding operators, as well as the techniques, tools, and materials involved in the wire bonding process. Whether you're aspiring to become a wire bonding operator or seeking insights into this field, this article will provide you with a comprehensive understanding of the role.
Introduction to Wire Bonding
Wire bonding is a technique widely used in the electronics industry to connect integrated circuits (ICs) or other semiconductor devices to their respective packaging or substrates. It involves the precise bonding of thin wires, typically made of gold, aluminum, or copper, to designated contact points on the device and the substrate. This connection enables the transfer of electrical signals between various components, ensuring their functionality.
What is a Wire Bonding Operator?
A wire bonding operator is an essential member of the manufacturing team responsible for executing the wire bonding process accurately. As a wire bonding operator, you are entrusted with the crucial task of creating reliable and durable wire bonds that establish electrical connections within electronic devices. It requires a combination of technical skills, attention to detail, and adherence to quality standards.
Skills and Qualifications of a Wire Bonding Operator
To excel as a wire bonding operator, several skills and qualifications are necessary. These include:
1. Technical Knowledge:
As a wire bonding operator, you must possess a strong understanding of wire bonding techniques, materials, and equipment. Knowledge of electrical circuits and basic semiconductor principles is also valuable.
2. Hand-Eye Coordination:
Precise wire bonding requires excellent hand-eye coordination to maneuver the bonding tool accurately and bond wires to the designated areas.
3. Attention to Detail:
Attention to detail is essential in identifying potential issues, such as misalignment, wire deformation, or other anomalies that may compromise the quality of the bond.
4. Problem-Solving Abilities:
Wire bonding operators must be able to troubleshoot common bonding problems, such as wire lifting, ball bonding issues, or insufficient bond strength, and implement appropriate solutions.
5. Communication Skills:
Clear communication with supervisors and colleagues is crucial to ensure proper understanding of work instructions and to report any challenges or concerns.
6. Quality Focus:
Maintaining a high level of quality is paramount in wire bonding. A wire bonding operator must be committed to adhering to quality control standards and implementing best practices.
Responsibilities of a Wire Bonding Operator
As a wire bonding operator, your responsibilities may include:
continuing from the outline:
Setting up and preparing wire bonding equipment and machines for operation.
Loading appropriate bonding tools, materials, and wire spools.
Ensuring proper alignment and calibration of the bonding machine.
Following work instructions and specifications provided by supervisors or engineers.
Performing visual inspections of the bond wires before and after bonding.
Operating the wire bonding machine to create accurate and reliable wire bonds.
Monitoring the bonding process for any issues or abnormalities.
Troubleshooting and resolving bonding-related problems.
Conducting regular maintenance and cleaning of the bonding equipment.
Documenting production data, including bond parameters and quality control records.
Collaborating with other team members to optimize production efficiency.
Adhering to safety protocols and guidelines to minimize workplace hazards.
The Wire Bonding Process
The wire bonding process involves several steps and considerations to ensure successful and reliable connections. Let's delve into the key aspects of the wire bonding process.
Wire Bonding Techniques
There are two primary wire bonding techniques: ball bonding and wedge bonding.
Ball bonding involves creating a small ball at the end of the wire, typically through thermal or ultrasonic energy, and then attaching it to the designated contact point. This technique is commonly used for gold and aluminum wires.
Wedge bonding, on the other hand, involves using a wedge-shaped tool to bond the wire directly to the contact point without the need for a ball formation. Wedge bonding is often employed for copper wires.
Wire Bonding Machines and Tools
Wire bonding machines are specialized equipment designed for precise wire bonding operations. These machines typically consist of a bonding head, a bonding tool, a wire feed mechanism, and control systems.
The bonding head holds the bonding tool and controls its movements during the bonding process. The wire feed mechanism guides the wire from the spool to the bonding tool. The control systems regulate parameters such as bonding force, ultrasonic or thermal energy, and bonding time.
Wire Bonding Materials
Various materials are used in wire bonding, depending on the application and requirements. Commonly used materials include:
Gold (Au) wires: Known for their excellent conductivity and corrosion resistance, gold wires are often used for high-performance applications.
Aluminum (Al) wires: Aluminum wires are widely used for general-purpose wire bonding due to their affordability and good electrical conductivity.
Copper (Cu) wires: Copper wires are gaining popularity due to their superior electrical conductivity and cost-effectiveness.
Bonding adhesives and materials: These include epoxy or adhesive materials used to secure the wire bonds and provide mechanical support.
The choice of wire material depends on factors such as electrical performance, device requirements, and cost considerations.
Safety Considerations for Wire Bonding Operators
Safety is of utmost importance for wire bonding operators, given the nature of the equipment and materials involved. Some key safety considerations include:
Proper training on operating the wire bonding machines and tools.
Wearing appropriate personal protective equipment (PPE), such as safety glasses and gloves.
Ensuring a clean and organized workspace to minimize the risk of accidents or injuries.
Adhering to electrical safety protocols to prevent shocks or short circuits.
Following proper handling and disposal procedures for bonding materials and waste.
By prioritizing safety, wire bonding operators can create a secure working environment and minimize potential risks.
Common Challenges Faced by Wire Bonding Operators
Wire bonding operators may encounter various challenges during the bonding process. Understanding these challenges and implementing appropriate solutions is essential for ensuring successful wire bonding operations.
Wire Bonding Failures and Troubleshooting
Bonding failures can occur due to issues such as wire lifting, wire breakage, bond quality defects, or insufficient bond strength. Troubleshooting these failures involves careful analysis and understanding of the root causes. Some common troubleshooting steps include:
Checking for proper wire alignment and tension: Misalignment or improper tension can lead to wire lifting or breakage. Ensure that the wire is correctly positioned and has sufficient tension for a secure bond.
Adjusting bonding parameters: Fine-tuning bonding parameters such as bonding force, ultrasonic or thermal energy, and bonding time can help improve bond quality and strength. Experiment with different settings to find the optimal parameters for a specific application.
Cleaning and maintaining bonding tools: Contaminated or worn-out bonding tools can affect bond quality. Regularly clean and inspect the bonding tools, replacing them when necessary.
Conducting post-bonding inspections: After bonding, visually inspect the wire bonds for any defects or anomalies. Use magnification tools if needed to ensure accuracy. Address any issues promptly to prevent further failures.
Collaborating with engineers and supervisors: In case of persistent bonding failures or complex issues, seek assistance from engineers or supervisors. They can provide valuable insights and guidance to troubleshoot and resolve challenging problems.
Quality Control in Wire Bonding
Maintaining quality control is essential in wire bonding to ensure reliable and durable connections. Some key quality control measures include:
Conducting regular bond strength tests: Perform pull or shear tests on a sample of wire bonds to evaluate their strength and adherence. This helps identify weak bonds and ensures adherence to quality standards.
Monitoring bond parameters: Continuously monitor and document bonding parameters such as bonding force, energy, and time. Deviations from specified ranges may indicate potential issues and require corrective action.
Implementing process controls: Establish and follow standardized procedures for wire bonding, including machine setup, material handling, and inspection processes. This minimizes variations and ensures consistent quality.
Performing visual inspections: Thoroughly inspect wire bonds for any visual defects such as wire deformation, cracks, or improper positioning. Reject any bonds that do not meet the required criteria.
By implementing robust quality control measures, wire bonding operators contribute to the overall reliability and performance of electronic devices.
Best Practices for Wire Bonding Operators
To excel in their role, wire bonding operators can adopt the following best practices:
1. Preparing for Wire Bonding
Familiarize yourself with the specifications and requirements of the bonding job.
Ensure proper alignment and calibration of the bonding machine.
Double-check the wire feed mechanism and bonding tools for any defects or contamination.
Verify the availability and suitability of bonding materials.
2. Operating Wire Bonding Machines
Follow the prescribed bonding parameters for the specific wire material and device.
Maintain consistent and steady hand movements during the bonding process.
Monitor the bonding machine for any abnormalities or deviations.
Immediately address any issues or failures during the bonding process.
3. Post-Bonding Inspections and Tests
Perform visual inspections of the wire bonds to detect any defects or anomalies.
Conduct bond strength tests periodically to ensure adequate bond integrity.
Document all relevant information, including bonding parameters and inspection results.
By following these best practices, wire bonding operators can enhance productivity, efficiency, and the overall quality of wire bonding operations.
The Role of Wire Bonding Operators in Manufacturing Industries
Wire bonding operators play a critical role in the manufacturing of various electronic devices, including semiconductors, integrated circuits, sensors, and microelectronic components. Their precise and meticulous work ensures the reliable functionality of these devices. Wire bonding operators collaborate closely with engineers, technicians, and other team members to meet production goals, maintain quality standards, and drive innovation in the industry.
The increasing demand for smaller, faster, and more complex electronic devices further highlights the significance of wire bonding operators. Their expertise and attention to detail contribute to the success of cutting-edge technologies in areas such as telecommunications, automotive,
medical devices, consumer electronics, and aerospace industries. As technology advances, wire bonding operators need to stay updated with the latest bonding techniques, materials, and equipment to meet the evolving demands of the industry.
The role of wire bonding operators extends beyond the manufacturing floor. They actively contribute to process improvement initiatives, providing valuable insights and feedback to enhance efficiency and yield. Their expertise in troubleshooting bonding-related issues plays a crucial role in minimizing downtime and optimizing production output.
In summary, wire bonding operators are instrumental in ensuring the reliable and efficient assembly of electronic devices. Their technical skills, attention to detail, and commitment to quality make them indispensable contributors to the manufacturing process.
Future Trends in Wire Bonding Technology
The field of wire bonding continues to evolve with advancements in technology and industry requirements. Some notable trends and developments in wire bonding technology include:
Miniaturization and high-density bonding: The demand for smaller, more compact electronic devices drives the need for finer wire bonding capabilities. Advanced techniques and tools enable wire bonding at microscale dimensions, facilitating high-density interconnections.
Wireless bonding: As wireless communication technologies become ubiquitous, wire bonding operators may encounter the need to work with wireless bonding techniques. This involves bonding antennas and wireless modules to enable wireless connectivity in devices.
Advanced bonding materials: Research and development efforts focus on exploring new wire bonding materials with improved electrical conductivity, reliability, and cost-effectiveness. Novel materials, such as silver-based wires or hybrid wire compositions, are being investigated for their suitability in specific applications.
Automation and robotics: Automation plays an increasingly significant role in wire bonding operations. Robotic systems and automated processes enhance precision, productivity, and repeatability, reducing human error and increasing overall efficiency.
Wire bonding for advanced packaging: The emergence of advanced packaging technologies, such as system-in-package (SiP) and fan-out wafer-level packaging (FOWLP), poses new challenges and opportunities for wire bonding operators. Adapting to these packaging techniques requires understanding the unique requirements and implementing specialized bonding approaches.
As the industry continues to push the boundaries of technology, wire bonding operators must embrace continuous learning and upskilling to stay at the forefront of these developments.
Wire Bonding Operator FAQs (Frequently Asked Questions)
1. Is wire bonding the only method used for interconnecting electronic components?
No, wire bonding is one of several methods used for interconnecting electronic components. Other methods include flip-chip bonding, soldering, and conductive adhesive bonding. The choice of interconnection method depends on factors such as device design, package type, and application requirements.
2. Can wire bonding be performed on different types of materials?
Yes, wire bonding can be performed on various materials, including metals like gold, aluminum, and copper. The selection of wire material depends on factors such as electrical conductivity, cost, and compatibility with the device and substrate materials.
3. Are there any limitations or challenges associated with wire bonding?
Wire bonding, like any manufacturing process, has its limitations and challenges. Some common challenges include wire deformation, bonding failures, and the need for precise alignment. These challenges can be overcome with proper training, troubleshooting skills, and continuous improvement in processes and equipment.
About Us
The individual at work operates the automated or semi-automated wire bonding machine to connect the die or chip to the lead frame or PCB through a micro-length metal wire.