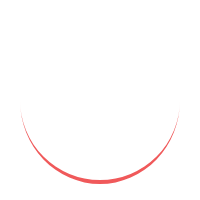
Introduction
In the world of welding, there is a crucial role that often goes unnoticed – the welding operator. These skilled professionals play a significant role in executing welding processes, ensuring precision, and maintaining safety standards. In this article, we will explore the responsibilities, skills, and qualifications of a welding operator, along with the various types of welding processes, safety precautions, common challenges, career opportunities, and more. If you're interested in the welding industry or considering becoming a welding operator, this article is for you.
What is a Welding Operator?
A welding operator is an individual responsible for setting up and operating welding equipment to join or cut metal parts. They work with various types of metals, including steel, aluminum, and stainless steel, using different welding techniques such as arc welding, MIG welding, TIG welding, and more. Welding operators interpret blueprints, select appropriate welding methods, prepare the work area, and ensure the quality and integrity of the welds.
Importance of Welding Operators
Welding operators play a vital role in numerous industries, including manufacturing, construction, automotive, aerospace, and shipbuilding. Their precise welding skills contribute to the fabrication and assembly of structures, machinery, and equipment. Without skilled welding operators, the integrity and safety of welded components could be compromised, leading to structural failures, equipment malfunction, or even hazardous situations.
Welding Operatory Skills and Qualifications
Becoming a proficient welding operator requires a combination of technical skills and qualifications. These professionals need a strong understanding of welding principles, metallurgy, and blueprint reading. Additionally, they must possess manual dexterity, hand-eye coordination, and the ability to work with precision. Welding operators often complete vocational training programs or apprenticeships and obtain certifications such as Certified Welding Operator (CWO) or Certified Welder (CW).
Welding Operatory Types of Welding Processes
Welding operators work with various welding processes, each suitable for specific applications and materials. Some common welding techniques include:
Arc Welding:
Shielded Metal Arc Welding (SMAW)
Gas Metal Arc Welding (GMAW/MIG)
Flux-Cored Arc Welding (FCAW)
Gas Welding:
Oxyfuel Welding (OFW)
Oxyacetylene Welding
Resistance Welding:
Spot Welding
Seam Welding
TIG Welding (Gas Tungsten Arc Welding)
Laser Welding
Electron Beam Welding
Plasma Arc Welding
And more...
Safety Precautions for Welding Operators
Safety is of paramount importance in welding operations due to the potential hazards involved. Welding operators must adhere to strict safety precautions to protect themselves and others from risks such as electrical shocks, fumes, fire, and UV radiation. Some essential safety measures include:
Wearing appropriate personal protective equipment (PPE) like welding helmets, gloves, and safety glasses.
Ensuring proper ventilation in the workspace to minimize f
mes and fumes.
3. Using welding screens or curtains to shield nearby workers from UV radiation.
Following proper fire prevention measures and having fire extinguishing equipment readily available.
Inspecting and maintaining welding equipment regularly to ensure safe operation.
Adhering to electrical safety protocols, such as grounding equipment and avoiding water contact.
Implementing proper handling and storage procedures for flammable gases and materials.
Welding Operatory Welding Equipment and Tools
To carry out their work effectively, welding operators utilize various equipment and tools specific to each welding process. These may include:
Welding Machines: Power sources that generate the necessary heat for welding.
Electrodes and Filler Materials: Consumable materials that create the weld joint.
Welding Guns/Torches: Handheld devices used to direct the welding arc and control the process.
Clamps and Fixtures: Tools to hold workpieces securely in place during welding.
Gas Cylinders: Containers for storing shielding gases used in some welding processes.
Welding Helmets and Protective Gear: Safety equipment to protect the operator from sparks, radiation, and other hazards.
Welding Operatory Common Challenges and Troubleshooting
Welding operators often encounter challenges during their work, which require problem-solving and troubleshooting skills. Some common issues include:
Welding Defects: These can include porosity, cracks, incomplete fusion, and distortion. Welding operators must understand the causes and remedies for these defects to ensure high-quality welds.
Material Preparation: Proper cleaning, beveling, and fit-up of workpieces are critical for successful welding. Operators must know how to prepare materials to achieve strong, durable welds.
Welding in Challenging Positions: Welding may sometimes require working in confined spaces or overhead positions, which can be physically demanding. Welding operators need to adapt to these conditions while maintaining weld quality.
Equipment Malfunctions: Like any machinery, welding equipment can experience malfunctions or breakdowns. Operators must be familiar with troubleshooting techniques and maintenance practices to keep the equipment running smoothly.
Welding Operatory Training and Certification
To become a welding operator, acquiring the necessary training and certification is essential. Many vocational schools, community colleges, and trade organizations offer comprehensive welding programs that provide hands-on training in various welding techniques and safety practices. These programs often culminate in certifications recognized by industry standards, such as the American Welding Society (AWS) certification.
Welding Operatory Career Opportunities
The demand for skilled welding operators remains high across multiple industries. Graduates of welding programs can find employment in sectors like:
Manufacturing and Fabrication: Welding operators contribute to the production of metal components, structures, and machinery.
Construction: Welding is crucial in the construction of buildings, bridges, and infrastructure.
Automotive and Aerospace: Welding operators play a role in vehicle manufacturing and aircraft assembly.
Shipbuilding and Offshore Industries: Welding is vital in constructing ships, oil rigs, and other marine structures.
Maintenance and Repair: Skilled welding operators are needed for repairing and maintaining metal equipment and structures.
Welding Operatory Salary and Job Outlook
The salary of a welding operator can vary depending on factors such as experience, location, and industry. According to the Bureau of Labor Statistics (BLS), the median annual wage for welders, cutters, solderers, and brazers was $44,190 as of May 2020. The job outlook for welding operators is favorable, with a projected employment growth of 3% from 2020 to 2030. Skilled welding operators who can adapt to new technologies and processes will have better prospects in the industry.
Welding Operatory Advancements and Specializations
c continue to gain experience and expertise, they have opportunities for advancements and specializations within the field. Some potential paths for growth include:
Welding Inspector: A welding operator can become a certified welding inspector (CWI) by acquiring additional training and passing examinations. Inspectors ensure that welding work meets quality standards and code requirements.
Welding Supervisor or Foreman: With experience, a welding operator can advance to a supervisory role, overseeing a team of welding operators and managing projects.
Welding Engineer: Those interested in the technical and engineering aspects of welding can pursue a degree in welding engineering. Welding engineers design welding procedures, develop new techniques, and optimize welding processes.
Specialized Welding Processes: Welding operators can specialize in specific welding techniques such as TIG welding, underwater welding, or laser welding. Specializing in a niche area can open up unique career opportunities.
Entrepreneurship: Experienced welding operators with business acumen may choose to start their own welding business, providing welding services to various industries.
Welding Operatory FAQs (Frequently Asked Questions)
What qualifications do I need to become a welding operator?
To become a welding operator, you typically need vocational training or an apprenticeship, along with certifications such as Certified Welding Operator (CWO) or Certified Welder (CW). These programs provide the necessary skills and knowledge to perform welding tasks effectively.
What safety precautions should welding operators follow?
Welding operators should wear appropriate personal protective equipment (PPE), ensure proper ventilation, and adhere to electrical safety protocols. They should also be familiar with fire prevention measures and handle welding equipment and materials safely.
What are some common challenges faced by welding operators?
Common challenges include welding defects, material preparation, working in challenging positions, and equipment malfunctions. Welding operators need to troubleshoot these issues and ensure the quality of their welds.
Are there opportunities for career advancement in welding?
Yes, welding operators can advance their careers by becoming welding inspectors, supervisors, or even welding engineers. They can also specialize in specific welding processes or start their own businesses.
What is the job outlook for welding operators?
The job outlook for welding operators is favorable, with a projected employment growth of 3% from 2020 to 2030. Skilled welding operators who stay updated with new technologies and processes will have better opportunities in the field.
About Us
The individual is primarily involved in all robotic and manual welding operations performed in automotive manufacturing. They use various types of welding processes such as TIG, MIG, SMAW welding etc. They support the welding technician in activities such as inspection of equipment condition, welding, gauging, testing and inspection of welded work pieces