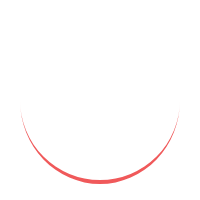
Outline
Introduction to Gas & Arc Welder
What is Gas Welding?
Subheading: Gas Welding Process
Subheading: Advantages of Gas Welding
Subheading: Applications of Gas Welding
What is Arc Welding?
Subheading: Arc Welding Process
Subheading: Advantages of Arc Welding
Subheading: Applications of Arc Welding
Gas Welder vs. Arc Welder
Subheading: Differences in Process
Subheading: Differences in Applications
Subheading: Factors to Consider in Choosing Between Gas and Arc Welders
Safety Precautions for Gas and Arc Welding
Subheading: Personal Protective Equipment (PPE)
Subheading: Ventilation and Fire Safety
Subheading: Electrical Safety
Common FAQs about Gas & Arc Welders
Subheading: What are the main types of gas welders?
Subheading: Can I use an arc welder for gas welding?
Subheading: Is gas welding or arc welding stronger?
Subheading: What safety gear do I need for gas and arc welding?
Subheading: How do I choose the right welder for my needs?
Conclusion
Gas and arc welding are two popular methods used in the field of welding. These techniques allow professionals to join metals and create strong and durable connections. In this article, we will explore the processes, advantages, applications, and differences between gas and arc welding, helping you understand which method is best suited for your specific welding needs.
Gas welding, also known as oxy-fuel welding, is a welding process that utilizes a mixture of fuel gas and oxygen to generate a flame for melting the base metal and a filler material. The filler material, usually a rod or wire, is added to the molten metal to form a strong bond upon solidification.
The gas welding process involves the following steps:
Preparation: The base metal is cleaned and prepared for welding by removing any dirt, rust, or contaminants.
Gas Setup: The welding torch is connected to a gas source, typically acetylene, and oxygen tanks.
Ignition: The gas mixture is ignited to create a flame.
Heating: The flame is directed towards the workpiece to heat the metal until it reaches the desired temperature.
Filler Material: The filler material is added to the molten pool to create a strong joint.
Cooling: The welded joint is allowed to cool and solidify, forming a strong bond.
Gas welding allows for precise control of the heat input, making it suitable for delicate and thin materials.
It is a versatile process that can be used for welding various metals, including steel, copper, and aluminum.
Gas welding produces aesthetically pleasing welds with good color matching and minimal distortion.
Applications of Gas Welding
Gas welding finds its applications in various industries, including:
Automotive repair and restoration
Plumbing and pipefitting
Jewelry making
Sculpture and artwork creation
Arc welding is a welding process that uses an electric arc between an electrode and the base metal to create a weld joint. The heat generated by the electric arc melts the electrode and base metal, which solidify upon cooling and form a strong weld.
Arc Welding Process
The arc welding process involves the following steps:
Preparation: Similar to gas welding, the base metal is cleaned and prepared for welding.
Power Supply: An arc welding machine is used to provide the necessary electric current for the welding process.
Electrode Selection: The appropriate electrode, based on the base metal and desired weld characteristics, is selected.
Arc Ignition: The electrode is brought into contact with the workpiece, and when a sufficient gap is achieved, an electric arc is struck.
Welding: The electrode is moved along the joint, and as it melts, it creates a weld pool that fuses the base metal.
Solidification: The molten metal solidifies, forming a strong bond.
Arc welding is a high-speed welding process, making it suitable for high-production applications.
It can be used to weld a wide range of materials, including steel, stainless steel, cast iron, and aluminum.
Arc welding provides deep penetration and strong welds, making it ideal for heavy-duty applications.
Arc welding is commonly used in the following industries:
Construction and infrastructure development
Manufacturing and fabrication
Shipbuilding and offshore industries
Repair and maintenance
While both gas and arc welding techniques are effective, they differ in several aspects, including the welding process and applications.
Differences in Process
Gas welding involves the use of a fuel gas and oxygen mixture to create a flame, while arc welding relies on an electric arc between an electrode and the base metal. Gas welding allows for more precise heat control, whereas arc welding provides deeper penetration.
Gas welding is commonly used for applications that require intricate work and finer control over the heat input. It is often preferred for projects involving thin metals and artistic creations. On the other hand, arc welding is suitable for heavy-duty applications that require strong and durable welds, such as structural welding and fabrication.
Factors to Consider in Choosing Between Gas and Arc Welders
When choosing between gas and arc welders, consider the following factors:
Project Requirements: Determine the specific welding needs of your project, including the type of metal, joint configuration, and thickness.
Skill Level: Gas welding requires more skill and precision, while arc welding can be relatively easier to learn.
Budget: Gas welders tend to be more expensive initially, but gas refills and consumables may be more cost-effective in the long run.
Portability: Gas welders are often more portable and can be used in remote locations without the need for an electrical power source.
Future Expansion: Consider your future welding needs and whether one method may be more versatile for a wider range of projects.
Safety Precautions for Gas and Arc Welding
Both gas and arc welding processes involve inherent risks, and it is essential to follow safety precautions to ensure a safe working environment.
Wear appropriate safety gear, including welding helmets, safety glasses, welding gloves, and fire-resistant clothing.
Use respiratory protection, such as a welding respirator, when working in confined spaces or in the presence of harmful fumes.
Ventilation and Fire Safety
Ensure proper ventilation in the workspace to minimize the accumulation of flammable gases and welding fumes.
Keep a fire extinguisher nearby and familiarize yourself with its usage.
Electrical Safety
Inspect welding equipment regularly for any damaged cables or connections.
Avoid contact with live electrical parts and ensure proper grounding of the welding equipment.
Q: What are the main types of gas welders?
A: The main types of gas welders include oxy-acetylene welders, oxy-propane welders, and oxy-natural gas welders. These types differ based on the fuel gas used in the welding process.
Q: Can I use an arc welder for gas welding?
A: No, arc welders are specifically designed for the arc welding process and cannot be used for gas welding without modifications.
Q: Is gas welding or arc welding stronger?
A: The strength of the weld depends on various factors, such as the base metal, welding technique, and operator skill. Both gas and arc welding methods can produce strong and durable welds when executed correctly.
Q: What safety gear do I need for gas and arc welding?
A: Essential safety gear includes a welding helmet, safety glasses, welding gloves, fire-resistant clothing, and respiratory protection. Additional safety equipment, such as welding curtains and ear protection, may also be necessary depending on the specific welding environment.
Q: How do I choose the right welder for my needs?
A: Consider factors such as project requirements, skill level, budget, portability, and future expansion when selecting a welder. It's recommended to consult with welding professionals or experts to determine the most suitable welder for your specific needs.
Gas and arc welding are versatile techniques that offer effective solutions for joining metals. Gas welding is well-suited for precision work and artistic projects, while arc welding excels in heavy-duty applications. By understanding the processes, advantages, and applications of both methods, you can make an informed decision when choosing the appropriate welding technique for your specific projects.
Q: Can I use an arc welder for gas welding?
A: No, arc welders are specifically designed for the arc welding process and cannot be used for gas welding without modifications.
Q: Is gas welding or arc welding stronger?
A: The strength of the weld depends on various factors, such as the base metal, welding technique, and operator skill. Both gas and arc welding methods can produce strong and durable welds when executed correctly.
Q: What safety gear do I need for gas and arc welding?
A: Essential safety gear includes a welding helmet, safety glasses, welding gloves, fire-resistant clothing, and respiratory protection. Additional safety equipment, such as welding curtains and ear protection, may also be necessary depending on the specific welding environment.
Q: How do I choose the right welder for my needs?
A: Consider factors such as project requirements, skill level, budget, portability, and future expansion when selecting a welder. It's recommended to consult with welding professionals or experts to determine the most suitable welder for your specific needs.
Q: What are the main types of gas welders?
A: The main types of gas welders include oxy-acetylene welders, oxy-propane welders, and oxy-natural gas welders. These types differ based on the fuel gas used in the welding process.
Gas & Arc Welder is a vocational trade This trade taken around one year and its syllabus is divide in four semesters. It is a tradesperson who parfect in fusing materials together. The course syllabus offers study such as welding skills and metal working techniques used in the exploration of metal sculpture; oxy-fuel and plasma arc cutting, hot and cold working of steel, shielded metal arc welding, weld design and finishing techniques; emphasized through hands on instruction and practice with the opportunity for creative expression and practical application. It open various job option for candidates after its successful completion. Candidates can get work in the aerospace, defence, ship building, construction and automotive industries on a large scale.
Welder Job Scopes: