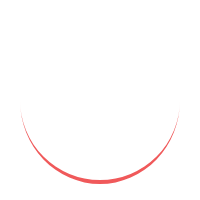
Introduction:
Crane operation and maintenance are crucial aspects of ensuring safe and efficient lifting operations in various industries. Whether it's construction, manufacturing, or logistics, cranes play a vital role in handling heavy loads. This article will provide an in-depth understanding of crane operation and maintenance, including different types of cranes, safe operation practices, maintenance guidelines, troubleshooting common issues, and promoting crane safety.
Section 1: Types of Cranes
Mobile Cranes:
Mobile cranes are versatile and commonly used in construction sites. They feature a telescopic boom mounted on a wheeled chassis, allowing them to be easily moved from one location to another.
Tower Cranes:
Tower cranes are commonly seen in tall building construction projects. They are fixed to the ground or building structure and have a long horizontal jib with a lifting capacity that can extend to great heights.
Overhead Cranes:
Overhead cranes, also known as bridge cranes, are typically used in factories and warehouses. They consist of a bridge-like structure that moves along elevated tracks and a hoist that moves horizontally.
Crawler Cranes:
Crawler cranes are equipped with caterpillar tracks, which provide stability and allow them to move on uneven terrain. They are often used in heavy-duty lifting operations, such as in the oil and gas industry.
Floating Cranes:
Floating cranes are mounted on barges or pontoons and are used for marine-based lifting operations. They are commonly seen in port areas for loading and unloading cargo from ships.
Section 2: Crane Operation
Pre-Operational Checks:
Before operating a crane, conducting thorough pre-operational checks is essential to ensure its safety and proper functioning. These checks involve visual inspections, mechanical inspections, and reviewing necessary documentation such as load charts and maintenance records.
Safe Crane Operation Practices:
Safe crane operation practices are crucial for preventing accidents and ensuring the well-being of workers. Proper operator training and certification, understanding load capacity and stability, effective communication protocols, and compliance with safety regulations are key aspects of safe crane operation.
Section 3: Crane Maintenance
Regular Inspections and Maintenance Schedule:
Regular inspections and adhering to a maintenance schedule are vital for keeping cranes in optimal condition. These inspections involve checking for wear and tear, loose or damaged components, and identifying any potential issues that may affect the crane's performance.
Lubrication and Cleaning:
Proper lubrication and cleaning of crane components help reduce friction, prevent corrosion, and extend the lifespan of the equipment. Regular greasing, oiling, and cleaning of critical parts contribute to smoother operation and enhanced reliability.
Electrical System Maintenance:
The electrical system of a crane requires regular inspection and maintenance. This includes checking wiring, connections, switches, and controls for any signs of damage or malfunction. Electrical system maintenance ensures safe and efficient operation.
Hydraulic System Maintenance:
The hydraulic system plays a crucial role in the lifting capabilities of cranes. Regular checks for hydraulic leaks, monitoring fluid levels, and maintaining hydraulic cylinders and valves are essential for smooth operation and avoiding potential failures.
Structural Inspections and Repairs:
Inspecting the structural integrity of the crane, including the boom, mast, and supporting structures, is necessary to identify any signs of damage or deformation. Timely repairs or replacement of structural components prevent accidents and ensure safe crane operation.
Section 4: Common Crane Issues and Troubleshooting
Malfunctioning Controls:
Issues with crane controls can arise due to electrical failures, damaged switches, or faulty wiring. Troubleshooting involves checking electrical connections, replacing damaged components, and testing the control system for proper functionality.
Electrical System Failures:
Electrical system failures can lead to crane breakdowns or unsafe operation. Troubleshooting includes diagnosing the root cause of the failure, repairing or replacing faulty components, and ensuring proper electrical connections.
Hydraulic Leaks:
Hydraulic leaks can affect the performance and safety of a crane. Identifying and repairing leaks, checking hydraulic hoses and fittings, and maintaining the proper fluid levels are necessary steps in troubleshooting hydraulic issues.
Wear and Tear of Components:
Regular use and heavy loads can cause wear and tear on crane components. Monitoring critical parts, such as wire ropes, hooks, and pulleys, and replacing them when necessary, ensures the crane's reliability and prevents accidents.
Unusual Noises or Vibrations:
Unusual noises or vibrations during crane operation may indicate underlying mechanical problems. Troubleshooting involves inspecting bearings, gears, motors, and other mechanical components to identify the source of the issue and taking appropriate corrective measures.
Section 5: Crane Safety Measures
Establishing a Safety Culture:
Creating a safety culture within an organization involves promoting awareness, providing proper training, enforcing safety policies, and encouraging open communication regarding crane operation and maintenance.
Proper Signage and Barricading:
Clear and visible signage, including load capacity limits, restricted zones, and safety instructions, helps prevent accidents. Barricading areas where cranes are operating ensures that unauthorized personnel stay clear of the danger zone.
Fall Protection Systems:
Implementing fall protection systems, such as harnesses and safety nets, reduces the risk of workers falling from elevated positions during crane operation. Adequate training on using fall protection equipment is essential.
Personnel Training and Awareness:
Thorough training programs for crane operators, riggers, and other personnel involved in crane operations enhance their knowledge, skills, and awareness of potential hazards. Regular safety meetings and refresher courses are important for maintaining safety standards.
Emergency Response Procedures:
Establishing emergency response procedures, including evacuation plans, communication protocols, and first aid training, ensures a prompt and effective response in the event of accidents or emergencies during crane operations.
FAQs
How often should a crane be inspected?
Cranes should undergo regular inspections, including pre-operational checks and scheduled maintenance, as outlined by the manufacturer's guidelines. Depending on the frequency of crane use, inspections may range from daily to monthly or yearly.
What are the common causes of crane accidents?
Common causes of crane accidents include operator error, improper maintenance, exceeding load capacity, inadequate training, unstable ground conditions, and adverse weather conditions.
Can anyone operate a crane?
No, operating a crane requires proper training and certification. Crane operators must undergo specialized training programs and obtain the necessary licenses or certifications to ensure safe and competent operation.
How long does it take to become a certified crane operator?
The duration to become a certified crane operator may vary based on the specific training program and the type of crane. Generally, it can take several weeks to several months to complete the necessary training and meet the certification requirements.
What are the penalties for not following crane safety regulations?
Penalties for not following crane safety regulations vary by jurisdiction but can include fines, work stoppages, license revocation, and legal liabilities in case of accidents or injuries caused by negligence.