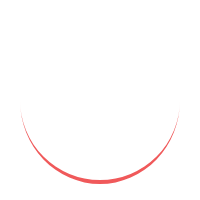
Sheet metal fabrication is a versatile and essential process in the manufacturing and construction industries. It involves transforming flat sheets of metal into various shapes and forms to create a wide range of products. From simple brackets to complex machinery parts, sheet metal fabricators play a crucial role in shaping the world around us.
Introduction
Sheet metal fabrication is the art of manipulating metal sheets into desired forms using specialized tools and techniques. It requires skill, precision, and a deep understanding of metal properties. Sheet metal fabricators work with materials such as stainless steel, aluminum, brass, copper, and more to produce high-quality components and structures.
What is Sheet Metal Fabrication?
Sheet metal fabrication encompasses several manufacturing processes, including cutting, bending, forming, joining, and finishing. It starts with raw metal sheets, which are then transformed into functional products or components through a series of carefully executed steps. This process enables the creation of custom-made parts that fit specific design requirements.
Tools and Equipment Used in Sheet Metal Fabrication
Sheet metal fabricators utilize various tools and equipment to achieve accurate and precise results. These include:
1. Shears and Nibblers
Shears and nibblers are used to cut metal sheets into desired shapes and sizes. Shears are ideal for straight cuts, while nibblers are used for curved or complex cuts.
2. Press Brakes
Press brakes are essential for bending and forming sheet metal. They apply force to the metal, causing it to bend at specific angles. This process enables the creation of precise angles and shapes.
3. Roll Forming Machines
Roll-forming machines are used to create continuous bends and curves in metal sheets. They pass the sheets through a series of rollers, gradually shaping them into the desired form.
4. Welding and Soldering Equipment
Welding and soldering equipment are crucial for joining metal components together. Various welding techniques, such as MIG, TIG, and spot welding, are employed to achieve strong and durable connections.
5. Finishing Tools
Finishing tools, such as grinders, polishers, and sanders, are used to smooth the surfaces of fabricated metal products. They enhance the aesthetic appeal and remove any sharp edges or imperfections.
Steps in Sheet Metal Fabrication Process
Sheet metal fabrication follows a systematic process that ensures accuracy and efficiency. The key steps involved in this process are as follows:
1. Design and Planning
Before starting the fabrication, a detailed design and plan are created based on the client's requirements. This includes measurements, material selection, and structural considerations.
2. Material Selection
Choosing the right type of sheet metal is essential for achieving desired results. Factors like strength, corrosion resistance, and cost are considered when selecting materials such as steel, aluminum, or copper.
3. Cutting and Shearing
The selected metal sheets are cut and sheared into the required sizes and shapes using specialized cutting tools, such as shears and nibblers.
4. Bending and Forming
Press brakes and roll-forming machines are used to bend and shape the metal sheets according to the design specifications. This step involves precision and accuracy to create the desired angles and curves.
5. Joining and Welding
Metal components are joined together using various welding techniques. Welding machines and soldering equipment ensure strong and reliable connections between the parts.
6. Finishing and Surface Treatment
The fabricated products undergo finishing processes to enhance their appearance and protect them from corrosion. This may include grinding, polishing, painting, or applying protective coatings.
Applications of Sheet Metal Fabrication
Sheet metal fabrication has a wide range of applications across industries. Some common applications include:
HVAC (Heating, Ventilation, and Air Conditioning) systems
Automotive components
Aerospace and aviation parts
Electrical enclosures
Industrial machinery
Architectural structures
Kitchen equipment and appliances
Furniture and fixtures
Advantages of Sheet Metal Fabrication
Sheet metal fabrication offers several advantages that make it a preferred choice for manufacturers and designers:
Versatility: Sheet metal can be manipulated into various shapes and forms, providing flexibility in design and functionality.
Strength and Durability: Fabricated metal products are known for their strength and durability, making them suitable for demanding applications.
Cost-Effective: Sheet metal fabrication can be a cost-effective manufacturing method, especially for large-scale production.
Customization: The ability to customize metal components allows for tailored solutions that meet specific design requirements.
Quick Turnaround: With advanced tools and efficient processes, sheet metal fabrication ensures fast turnaround times without compromising quality.
Challenges in Sheet Metal Fabrication
Despite its many advantages, sheet metal fabrication also presents some challenges that fabricators need to overcome:
Material Selection: Choosing the right material for a specific application can be challenging due to factors such as cost, availability, and compatibility.
Precision and Accuracy: Achieving precise measurements and angles requires skill and attention to detail. Even slight deviations can impact the final product's functionality.
Complex Designs: Fabricating intricate and complex designs demands expertise and specialized equipment to ensure quality and consistency.
Welding and Joining: Welding different metals or dissimilar materials can be challenging, as it requires selecting suitable techniques and materials for optimal strength and reliability.
Surface Finish: Achieving the desired surface finish and eliminating imperfections can be time-consuming and requires additional processes.
Tips for Finding a Reliable Sheet Metal Fabricator
When searching for a reliable sheet metal fabricator, consider the following tips:
Experience and Expertise: Look for fabricators with a proven track record and experience in handling similar projects.
Quality Assurance: Ensure the fabricator follows strict quality control measures to deliver high-quality products consistently.
Equipment and Technology: Assess the fabricator's equipment and technological capabilities to ensure they are up-to-date and can handle complex requirements.
Communication and Collaboration: Choose a fabricator who values clear communication and is willing to collaborate throughout the fabrication process.
Reviews and References: Read customer reviews and seek references to gain insights into the fabricator's reputation and customer satisfaction.
FAQs
1. How long does sheet metal fabrication take?
The time required for sheet metal fabrication depends on various factors, including the complexity of the design, the size of the project, and the fabricator's workload. It's best to discuss the timeline with your fabricator based on your specific requirements.
2. Can sheet metal fabrication be used for prototypes?
Yes, sheet metal fabrication is often used to create prototypes. Its flexibility allows for rapid prototyping, enabling designers and engineers to test their ideas before moving to full-scale production.
3. Is sheet metal fabrication suitable for small-scale projects?
Yes, sheet metal fabrication can accommodate both small and large-scale projects. Whether you need a single custom component or a batch of products, fabricators can adjust their processes accordingly.
4. How do I ensure the quality of fabricated products?
To ensure the quality of fabricated products, it's important to work with a reputable fabricator who follows strict quality control measures. You can also request samples, check certifications, and discuss quality requirements with the fabricator.
5. Can sheet metal fabrication be cost-effective for my project?
Sheet metal fabrication can offer cost-effective solutions, especially for larger production quantities. However, the cost will depend on various factors such as material selection, design complexity, and finishing requirements. It's best to discuss the specifics of your project with a fabricator to get accurate cost estimates.