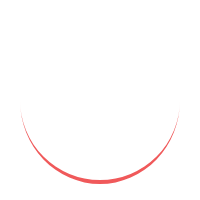
Introduction
Motor winding plays a crucial role in the functioning of heavy electrical motors. A motor winder is responsible for repairing and rewinding damaged motor coils to ensure optimal performance. This article will delve into the world of heavy electrical motor winders, discussing their skills, the process they follow, the challenges they face, and the importance of their role in the industry.
Understanding the Role of a Motor Winder
A motor winder is a skilled professional who specializes in repairing and rewinding electrical motor coils. They work with various types of motors, including those used in industrial machinery, pumps, generators, and other heavy-duty applications. Motor winders are trained to handle different motor sizes and have a deep understanding of the electrical principles involved in motor winding.
Skills and Qualifications Required for Motor Winding
Becoming a successful motor winder requires a combination of technical knowledge and practical skills. A strong foundation in electrical engineering or a related field is essential. Additionally, motor winders need to possess expertise in electrical systems, circuitry, and the operation of electrical motors. Excellent manual dexterity, attention to detail, and problem-solving abilities are also critical attributes for motor winders.
Tools and Equipment Used by Motor Winders
Motor winders employ a variety of specialized tools and equipment to carry out their work effectively. These include insulation materials, wire cutters, wire strippers, winding machines, surge testers, multimeters, and soldering equipment. They also use various safety gear, such as gloves, goggles, and protective clothing, to ensure their own safety while working with high-voltage systems.
Step-by-Step Process of Motor Winding
Motor winding involves several steps to repair or replace damaged coils in an electrical motor. The process typically includes:
Disassembling the Motor: The motor winder carefully dismantles the motor, taking note of its various components and their positions.
Inspecting and Testing the Components: The winder inspects the motor's stator, rotor, bearings, and other parts for any signs of damage or wear. They may also conduct electrical tests to identify faulty components.
Replacing Damaged Parts: If any components are found to be faulty, the motor winder replaces them with new ones of the appropriate specifications.
Winding the Coils: The winder calculates the required number of turns and the gauge of wire needed to rewind the coils. They carefully wind the new coils, ensuring proper insulation and alignment.
Assembling the Motor: Once the coils are wound, the winder reassembles the motor, ensuring all components are correctly positioned and connected.
Importance of Proper Motor Winding Techniques
Proper motor winding techniques are vital for the optimal performance and longevity of electrical motors. Well-wound coils ensure efficient power transmission, reduce electrical losses, and prevent overheating. Motor winders play a crucial role in maintaining motor performance and preventing premature motor failures. Their expertise ensures that the motor operates safely and reliably.
Common Challenges Faced by Motor Winders
Motor winders encounter several challenges in their work, requiring them to troubleshoot and find effective solutions. Some common challenges include:
Identifying Faulty Wiring: Winding faults, such as open circuits or short circuits, can be difficult to detect. Motor winders must possess advanced diagnostic skills to identify and rectify these issues.
Dealing with Coil Interturn Faults: Interturn faults, where the insulation between individual turns of a coil breaks down, can lead to motor failures. Motor winders need to address these faults to prevent further damage.
Handling High Voltage Systems: Motor winders often work with high-voltage systems, which pose risks if not handled properly. They must adhere to strict safety protocols to protect themselves and others.
Safety Measures for Motor Winders
Safety is of paramount importance in the field of motor winding. Motor winders must follow safety procedures, including wearing appropriate protective gear, de-energizing electrical systems, and using insulation materials to prevent electrical shocks. They must also be knowledgeable about fire safety and emergency response protocols.
Advancements in Motor Winding Technology
Advancements in motor winding technology have streamlined the process and improved efficiency. Automated winding machines and computer-aided design (CAD) software have made the winding process more precise and consistent. Additionally, the use of advanced insulation materials and diagnostic equipment has enhanced the reliability and performance of rewound motors.
Career Opportunities and Future Outlook
The demand for skilled motor winders continues to grow in industries such as manufacturing, energy, and transportation. As more companies rely on heavy electrical motors, the need for qualified professionals to repair and maintain these motors will remain high. Motor winders can find employment in electrical repair shops, motor manufacturing companies, and maintenance departments of various industries.
FAQs heavy electrical motors
Is motor winding a specialized skill?
Yes, motor winding requires specialized knowledge and skills in electrical engineering and motor systems.
Can I rewind a motor myself?
Motor winding is a complex task that requires expertise and experience. It is recommended to consult a professional motor winder for such repairs.
How often should motors be rewound?
The frequency of motor rewinding depends on factors such as motor usage, operating conditions, and maintenance practices. A qualified motor winder can assess the motor's condition and provide appropriate recommendations.
Are there any risks involved in motor winding?
Yes, working with electrical systems and high-voltage equipment can be dangerous. Motor winders must follow strict safety protocols to mitigate risks and ensure their own safety.
What are some signs that a motor needs rewinding?
Common signs include decreased motor performance, increased operating temperatures, unusual noises, and frequent motor failures. Consulting a motor winder can help diagnose the problem accurately.