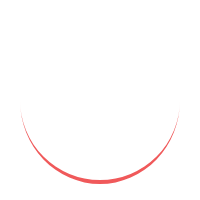
Sheet metal and fabrication are integral parts of many industries, from automotive and aerospace to construction and electronics. This article will provide a comprehensive overview of sheet metal fabrication, exploring its processes, benefits, applications, considerations, and future trends.
Introduction
Sheet metal refers to metal that is formed into thin, flat pieces. It is widely used due to its versatility, durability, and ease of fabrication. Sheet metal fabrication, on the other hand, is the process of transforming sheet metal into desired shapes and structures through various manufacturing techniques.
What is Sheet Metal?
Sheet metal is commonly made from metals such as steel, aluminum, brass, copper, or nickel. It is available in various thicknesses, typically measured in gauge, and comes in different forms, including sheets, plates, and foils. Sheet metal can be easily cut, bent, and formed, making it suitable for a wide range of applications.
Sheet Metal Fabrication: An Overview
Sheet metal fabrication involves several processes to transform flat sheets of metal into usable components and products. These processes include cutting, bending, forming, welding, assembly, and finishing. Each step requires specialized techniques and equipment to achieve the desired outcome.
Cutting
Cutting is the initial step in sheet metal fabrication. It involves separating the sheet metal into specific sizes and shapes. Common cutting methods include shearing, sawing, laser cutting, and plasma cutting.
Bending
Bending is the process of deforming the sheet metal to create angles or curves. This is typically done using a press brake, which applies force to the metal, causing it to bend along a predetermined axis.
Forming
Forming refers to the process of shaping the sheet metal without removing any material. It includes techniques such as roll forming, stamping, and deep drawing, which enable the creation of complex shapes and structures.
Welding
Welding is used to join two or more pieces of sheet metal together. Various welding techniques, such as TIG welding, MIG welding, and spot welding, are employed based on the type of metal and the desired strength of the joint.
Assembly
Assembly involves combining multiple sheet metal components to create a finished product. This may include fastening, riveting, or bonding the individual pieces together.
Finishing
Finishing is the final step in sheet metal fabrication. It includes processes such as surface cleaning, polishing, painting, and coating to enhance the appearance, protect against corrosion, or provide specific surface properties.
Benefits of Sheet Metal Fabrication
Sheet metal fabrication offers several advantages over other manufacturing methods. These include:
Versatility: Sheet metal can be easily customized and shaped to meet specific design requirements, allowing for flexibility in product development.
Strength and Durability: Sheet metal components exhibit high strength and durability, making them suitable for applications that require structural integrity.
Cost-Effective: Sheet metal fabrication is often a cost-effective solution due to the efficiency of mass production and the recyclability of metals.
Efficiency: With the use of advanced machinery and computer-aided design (CAD) software, sheet metal fabrication processes can be highly efficient, reducing production time and costs.
Wide Range of Materials: Sheet metal fabrication can be performed on various metals, offering a diverse selection of material properties and characteristics.
Applications of Sheet Metal Fabrication
Sheet metal fabrication finds applications across numerous industries, including:
Automotive: Body panels, chassis components, exhaust systems.
Aerospace: Aircraft parts, engine components, interior fittings.
Construction: Roofing, cladding, structural frameworks.
Electronics: Enclosures, cabinets, heat sinks.
Medical: Surgical instruments, equipment housings, hospital furniture.
Consumer Goods: Appliances, furniture, decorative items.
Choosing the Right Sheet Metal for Fabrication
When selecting sheet metal for fabrication, several factors need to be considered, including:
Material Selection: The choice of metal will depend on factors such as strength requirements, corrosion resistance, weight considerations, and cost.
Design Considerations: The design of the product and its intended function will influence the selection of sheet metal, including thickness, bend radius, and surface finish.
Cost and Efficiency: Balancing the cost of the material with production efficiency and desired quality is crucial in optimizing the fabrication process.
Precision and Tolerance: The level of precision and tight tolerances required for the product will influence the choice of sheet metal and fabrication techniques.
Environmental Impact: Considering the environmental impact of the selected sheet metal, including recyclability and sustainability, is becoming increasingly important.
Latest Advancements in Sheet Metal Fabrication
The field of sheet metal fabrication has witnessed several advancements in recent years. Some notable innovations include:
Additive Manufacturing: The integration of 3D printing technologies into sheet metal fabrication has revolutionized the prototyping and production processes, enabling complex geometries and reduced material waste.
Automation and Robotics: Automation and robotics have increased the speed and accuracy of sheet metal fabrication, leading to higher productivity and reduced labor costs.
Advanced Forming Techniques: Advanced forming techniques, such as hydroforming and electromagnetic forming, offer new possibilities for shaping sheet metal with improved efficiency and precision.
Digital Integration: The use of digital technologies, such as computer-aided design (CAD) and computer-aided manufacturing (CAM), has enhanced the design, simulation, and optimization of sheet metal fabrication processes.
Tips for Effective Sheet Metal Fabrication
To ensure successful sheet metal fabrication, consider the following tips:
Proper Planning and Design: Thoroughly plan and design the product to minimize errors and optimize the fabrication process.
Choosing the Right Equipment and Tools: Select appropriate machinery, tools, and software to achieve accurate and efficient fabrication results.
Quality Control and Inspection: Implement rigorous quality control measures to identify and address any defects or issues during fabrication.
Safety Measures: Adhere to proper safety guidelines and ensure the well-being of workers throughout the fabrication process.
Continuous Improvement: Strive for continuous improvement by analyzing and optimizing the fabrication process, considering feedback and lessons learned.
Future Trends in Sheet Metal Fabrication
Looking ahead, several trends are likely to shape the future of sheet metal fabrication:
Advanced Materials: The development of new lightweight and high-strength materials will expand the possibilities for sheet metal fabrication in industries such as aerospace and automotive.
Smart Manufacturing: The integration of sensors, data analytics, and machine learning in sheet metal fabrication processes will lead to improved efficiency, predictive maintenance, and quality control.
Energy Efficiency: The adoption of energy-efficient processes and equipment will contribute to sustainable and environmentally friendly sheet metal fabrication.
Customization and Personalization: With advancements in digital technologies, sheet metal fabrication will enable more customized and personalized products to meet specific customer demands.
Collaborative Robotics: The use of collaborative robots, or cobots, will enhance the interaction between humans and machines, improving productivity and flexibility in sheet metal fabrication.
FAQs
What is the difference between sheet metal and plate metal?
Sheet metal is generally thinner than plate metal, with a thickness typically measured in gauge. Plate metal, on the other hand, is thicker and often used for more heavy-duty applications.
Can any metal be used for sheet metal fabrication?
While sheet metal fabrication can be performed on various metals, common choices include steel, aluminum, brass, copper, and nickel due to their favorable properties and availability.
How do I choose the right thickness for sheet metal fabrication?
The choice of sheet metal thickness depends on factors such as the application, structural requirements, and fabrication processes. Consulting with experts or referring to industry standards can help determine the appropriate thickness.
What are some common challenges in sheet metal fabrication?
Common challenges in sheet metal fabrication include achieving precise tolerances, minimizing material waste, addressing distortion during forming processes, and ensuring proper joint strength in welding.
Is sheet metal fabrication environmentally friendly?
Sheet metal fabrication can be environmentally friendly, especially when using recyclable metals and implementing sustainable practices. Recycling scrap metal generated during fabrication further contributes to its eco-friendliness.