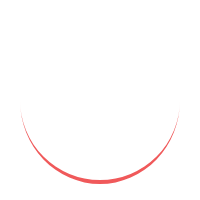
In today's rapidly evolving world, the field of equipment manufacturing is undergoing significant transformations. As industries strive to improve their production processes, it becomes crucial to explore and adopt advanced manufacturing techniques. This article will delve into the various techniques employed in equipment manufacturing, highlighting the shift from traditional methods to advanced approaches, their benefits, and the role of emerging technologies like the Internet of Things (IoT).
Introduction
Manufacturing techniques play a pivotal role in the production of equipment across various industries. These techniques determine the quality, precision, and efficiency of the end products. Traditionally, equipment manufacturing relied on methods such as casting, machining, and welding. However, with advancements in technology, a new wave of techniques has emerged, revolutionizing the manufacturing landscape.
Importance of Equipment Manufacturing Techniques
Effective equipment manufacturing techniques are essential for several reasons. First and foremost, they ensure the production of high-quality products that meet industry standards. By leveraging efficient techniques, manufacturers can minimize defects, enhance durability, and improve overall performance. Additionally, these techniques contribute to increased productivity, reduced costs, and shortened lead times, thereby giving businesses a competitive edge.
Traditional Manufacturing Techniques
Casting
Casting is a conventional manufacturing technique that involves pouring molten material into a mold, allowing it to solidify and take the desired shape. It is commonly used for creating intricate parts, such as engine components and industrial machinery.
Machining
Machining involves the removal of material from a workpiece using various cutting tools. It encompasses processes like drilling, milling, turning, and grinding. Machining is widely employed in equipment manufacturing to achieve precise dimensions and smooth finishes.
Welding
Welding is a process that joins two or more pieces of metal together by melting and fusing them. It is extensively used in the fabrication of structural components and equipment assemblies.
Advanced Manufacturing Techniques
With technological advancements, advanced manufacturing techniques have gained prominence in the equipment manufacturing industry. Let's explore some of these techniques:
Additive Manufacturing
Additive manufacturing, also known as 3D printing, is a revolutionary technique that builds three-dimensional objects layer by layer. It offers design flexibility, rapid prototyping capabilities, and the ability to create complex geometries. Additive manufacturing has found applications in various sectors, including aerospace, automotive, and medical equipment manufacturing.
Computer Numerical Control (CNC)
CNC involves the use of computer-controlled machines to automate the manufacturing process. It enables precise and repeatable production of components, leading to improved accuracy and reduced human errors. CNC machines are commonly used for cutting, milling, and drilling operations.
Robotics
Robotics plays a vital role in modern equipment manufacturing. Robotic systems automate repetitive tasks, enhance efficiency, and ensure consistent quality. They can handle complex assembly processes, material handling, and inspection, thus boosting productivity.
Benefits of Advanced Manufacturing Techniques
The adoption of advanced manufacturing techniques offers numerous benefits for equipment manufacturers. Let's explore some of the key advantages:
Enhanced Precision and Accuracy
Advanced techniques, such as additive manufacturing and CNC, enable manufacturers to achieve higher levels of precision and accuracy. This ensures that equipment components fit together seamlessly, leading to improved performance and reduced maintenance issues.
Increased Efficiency and Productivity
By leveraging advanced manufacturing techniques, equipment manufacturers can streamline their production processes, eliminate bottlenecks, and optimize resource utilization. This results in increased productivity, shorter lead times, and higher output volumes.
Design Flexibility and Customization
Advanced techniques provide designers and engineers with greater design freedom. Additive manufacturing, in particular, allows for complex geometries and customization options that were previously unattainable. Manufacturers can create equipment tailored to specific customer requirements, giving them a competitive advantage.
Cost Savings
Advanced manufacturing techniques often lead to cost savings in the long run. By optimizing material usage, reducing waste, and minimizing the need for manual labor, manufacturers can achieve significant cost reductions. Additionally, the ability to rapidly prototype and iterate designs using additive manufacturing helps in minimizing development costs.
Integration of Internet of Things (IoT) in Equipment Manufacturing
The Internet of Things (IoT) has emerged as a game-changer in equipment manufacturing. IoT technologies facilitate connectivity and data exchange between equipment components, enabling real-time monitoring, predictive maintenance, and remote control. By leveraging IoT, manufacturers can optimize equipment performance, reduce downtime, and enhance overall operational efficiency.
Future Trends in Equipment Manufacturing Techniques
The field of equipment manufacturing continues to evolve rapidly. Some of the future trends to watch out for include:
Smart factories powered by automation, data analytics, and artificial intelligence.
Continued advancements in additive manufacturing materials and processes.
Adoption of augmented reality (AR) and virtual reality (VR) technologies for training and design visualization.
Integration of machine learning algorithms to optimize manufacturing processes and improve product quality.
Challenges and Limitations
While advanced manufacturing techniques offer numerous benefits, they also come with challenges and limitations. These include:
Initial high setup costs and investment in new technologies.
The need for upskilling the workforce to operate and maintain advanced equipment.
Quality control and ensuring consistent material properties in additive manufacturing.
Intellectual property and security concerns associated with digital design files and IoT connectivity.
FAQs
Q: How do advanced manufacturing techniques benefit equipment manufacturers?
A: Advanced manufacturing techniques offer benefits such as enhanced precision, increased efficiency, design flexibility, and cost savings.
Q: What is additive manufacturing?
A: Additive manufacturing, also known as 3D printing, is a technique that builds objects layer by layer, allowing for complex geometries and rapid prototyping.
Q: How does the Internet of Things (IoT) impact equipment manufacturing?
A: IoT enables connectivity between equipment components, facilitating real-time monitoring, predictive maintenance, and remote control for improved performance and efficiency.
Q: What are the future trends in equipment manufacturing?
A: Future trends include smart factories, advancements in additive manufacturing, augmented reality, virtual reality, and machine learning integration.
Q: What challenges are associated with advanced manufacturing techniques?
A: Challenges include high setup costs, workforce