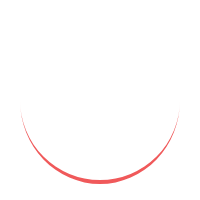
In today's rapidly advancing technological landscape, the role of a service engineer has become crucial, especially in the field of installation and commissioning. Service engineers play a vital role in ensuring that complex machinery and equipment are set up correctly and functioning optimally. This article explores the responsibilities, skills, challenges, and best practices of service engineers involved in installation and commissioning processes.
What is a Service Engineer?
A service engineer is a technical professional who possesses in-depth knowledge and expertise in a specific field. They are trained to handle complex machinery and equipment and are responsible for ensuring that these systems operate efficiently. Service engineers may specialize in different areas, such as mechanical, electrical, or software engineering, depending on the nature of the equipment they work with.
Role of a Service Engineer in Installation and Commissioning
Responsibilities of a Service Engineer
Service engineers involved in installation and commissioning have several key responsibilities. Their primary role is to ensure that the equipment is installed correctly, according to the manufacturer's specifications and industry standards. They must also conduct thorough testing to verify that the equipment is functioning as intended. Additionally, service engineers are responsible for documenting their work, preparing reports, and providing feedback to the relevant stakeholders.
Importance of Installation and Commissioning
The installation and commissioning phase is critical for any machinery or equipment. It ensures that the system is set up correctly, minimizing the risk of operational issues or breakdowns in the future. Proper installation and commissioning also contribute to the overall performance and longevity of the equipment, enhancing its efficiency and reducing potential downtime.
Skills and Qualifications of a Service Engineer
To excel in the role of a service engineer, certain skills and qualifications are essential. While specific requirements may vary depending on the industry and equipment involved, the following are key attributes for success:
Service Engineer - Installation and Commissioning Technical Knowledge
Service engineers must have a solid understanding of the equipment they work with. This includes knowledge of its technical specifications, operating principles, and troubleshooting methods. They should be able to interpret technical diagrams, schematics, and manuals effectively.
Service Engineer - Installation and Commissioning Problem-solving Skills
Service engineers often encounter complex issues that require quick and effective problem-solving. They must be able to identify the root cause of problems and implement appropriate solutions efficiently. Strong analytical thinking and troubleshooting abilities are crucial in this role.
Service Engineer - Installation and Commissioning Communication Skills
Effective communication is essential for service engineers, as they interact with clients, colleagues, and manufacturers regularly. They should be able to explain technical concepts in a clear and concise manner, both verbally and in written reports. Good interpersonal skills are also important for building rapport with customers.
Service Engineer - Installation and Commissioning Attention to Detail
Precision and attention to detail are critical for service engineers during the installation and commissioning process. They must carefully follow instructions, perform accurate measurements, and ensure that all connections and configurations are correct. Even minor oversights can lead to significant operational issues later on.
Service Engineer - Installation and Commissioning Steps Involved in Installation and Commissioning
The installation and commissioning process typically involves several sequential steps. While the exact procedure may vary depending on the equipment and industry, the following steps provide a general overview:
Service Engineer - Installation and Commissioning Site Assessment and Preparation
Before the installation begins, service engineers conduct a thorough assessment of the site where the equipment will be installed. This includes evaluating the available space, ensuring the necessary infrastructure is in place, and assessing any potential risks or challenges.
Service Engineer - Installation and Commissioning Equipment Inspection and Verification
Service engineers inspect the equipment to ensure it is in perfect condition and matches the client's specifications. They verify the presence of all components, check for any damages or defects, and compare the received equipment with the purchase order or contract.
Service Engineer - Installation and Commissioning Installation and Assembly
Once the site is prepared and the equipment is verified, the installation process begins. Service engineers follow the manufacturer's guidelines to assemble the equipment correctly. They connect all necessary components, such as electrical, mechanical, or software interfaces, following the specified procedures.
Service Engineer - Installation and Commissioning Testing and Calibration
After the installation, service engineers perform comprehensive testing to verify the equipment's functionality. This includes checking all connections, running diagnostic tests, and calibrating the system to ensure optimal performance. They analyze the test results and make any necessary adjustments or corrections.
Service Engineer - Installation and Commissioning Documentation and Reporting
Throughout the installation and commissioning process, service engineers maintain detailed documentation of their activities. This includes recording all installation steps, test results, and any modifications made. They generate comprehensive reports summarizing the installation process and provide them to the relevant stakeholders.
Service Engineer - Installation and Commissioning Challenges Faced by Service Engineers
Service engineers in the field of installation and commissioning often encounter various challenges that can impact their work. Some common challenges include:
Service Engineer - Installation and Commissioning Time Constraints
Installation and commissioning projects often operate on tight schedules. Service engineers must efficiently complete their tasks within the allocated time frame, ensuring that the equipment is up and running promptly. Time management and prioritization skills are crucial to meet project deadlines.
Service Engineer - Installation and Commissioning Unforeseen Issues
Despite meticulous planning, service engineers may encounter unexpected issues during the installation process. This could include compatibility issues, component failures, or unanticipated site conditions. Service engineers must be adaptable and resourceful in finding solutions to such challenges.
Service Engineer - Installation and Commissioning Safety Considerations
Installation and commissioning involve working with complex machinery and equipment, which can pose safety risks. Service engineers must adhere to safety protocols, use personal protective equipment, and prioritize the well-being of themselves and others during the installation process.
Service Engineer - Installation and Commissioning Customer Expectations
Meeting customer expectations is essential for service engineers. They must ensure that the installed equipment performs as expected and meets the client's requirements. Clear communication and understanding of customer needs are crucial to deliver a satisfactory outcome.
Best Practices for Service Engineers in Installation and Commissioning
To ensure successful installation and commissioning projects, service engineers can follow these best practices:
Service Engineer - Installation and Commissioning Planning and Organization
Thorough planning is key to a smooth installation process. Service engineers should create a detailed project plan, including timelines, tasks, and resource requirements. Organizing tools, equipment, and materials in advance minimizes delays and ensures a structured workflow.
Service Engineer - Installation and Commissioning Effective Communication
Service engineers must maintain clear and open communication with clients, colleagues, and other stakeholders throughout the installation and commissioning process. Regular updates, progress reports, and addressing concerns promptly foster trust and collaboration.
Service Engineer - Installation and Commissioning Continual Learning and Skill Development
Technology and equipment evolve rapidly, making continuous learning essential for service engineers. Staying updated with the latest industry trends, attending training programs, and acquiring new certifications helps service engineers enhance their skills and adapt to new challenges.
Service Engineer - Installation and Commissioning Importance of Customer Satisfaction
Customer satisfaction is paramount in the role of a service engineer. Providing exceptional service not only builds trust and loyalty but also enhances the reputation of the organization. Service engineers should prioritize customer needs, actively listen to feedback, and promptly address any concerns.
Service Engineer - Installation and Commissioning Building Customer Trust
By demonstrating expertise, professionalism, and a customer-centric approach, service engineers can build trust with clients. This involves delivering on promises, providing accurate information, and consistently exceeding customer expectations.
Service Engineer - Installation and Commissioning Handling Customer Complaints
Even with meticulous planning, issues can arise during installation and commissioning. Service engineers should be prepared to handle customer complaints effectively. This involves active listening, empathy, and proactive problem-solving to find satisfactory resolutions.
Service Engineer - Installation and Commissioning FAQs
What are the typical working hours for a service engineer?
The working hours for service engineers can vary depending on the industry and specific projects. They may involve regular daytime hours or require flexibility, including evening and weekend work, particularly for urgent installations or maintenance.
Is a technical degree necessary to become a service engineer?
While a technical degree can provide a strong foundation, it is not always a strict requirement. Practical experience, relevant certifications, and specialized training can also qualify individuals for service engineer roles.
How long does the installation and commissioning process usually take?
The duration of the installation and commissioning process depends on the complexity of the equipment and the scope of the project. It can range from a few days to several weeks or even months for large-scale installations.
What is the difference between installation and commissioning?
Installation refers to the physical setup and assembly of equipment according to specifications, while commissioning involves the testing, calibration, and verification of the equipment's performance to ensure it meets the required standards.
Are service engineers required to travel frequently?
Service engineers often need to travel to various locations, depending on the nature of their work. They may need to visit client sites for installations, repairs, or maintenance, requiring travel both locally and internationally.