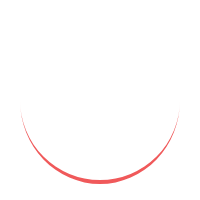
Flux cored arc welding (FCAW) is a versatile welding process that offers various advantages over traditional welding methods. In this article, we will explore the concept of Flux Cored Arc Welders, their applications, benefits, and provide a comprehensive guide on how to use them effectively. Whether you are a professional welder or a DIY enthusiast, understanding FCAW and its applications can open new possibilities in your welding projects.
Introduction to Flux Cored Arc Welding (FCAW)
Flux cored arc welding (FCAW) is a welding technique that utilizes a continuously fed tubular electrode filled with flux. The flux serves multiple purposes, such as protecting the weld from atmospheric contamination, stabilizing the arc, and providing additional alloying elements to the weld metal. FCAW is known for its high deposition rates, deep penetration capabilities, and suitability for both indoor and outdoor welding.
Understanding Flux Cored Arc Welders (FCAW)
A Flux Cored Arc Welder (FCAW) is a type of welding machine specifically designed for the Flux Cored Arc Welding process. It consists of a power source, a wire feeder, and a welding gun. The wire feeder delivers the continuously fed tubular electrode to the welding gun, which then melts the electrode and forms the weld.
Advantages of Flux Cored Arc Welding
FCAW offers several advantages over other welding methods. Firstly, it allows for high welding speeds, making it ideal for projects that require efficiency. Secondly, the process provides deep penetration, ensuring strong and reliable welds. Additionally, FCAW is suitable for welding various materials, including carbon steel, stainless steel, and even some non-ferrous metals.
Types of Flux Cored Arc Welders
There are two main types of Flux Cored Arc Welders: self-shielded and gas-shielded. Self-shielded FCAW does not require an external shielding gas, as the flux within the electrode generates the necessary shielding gases when heated. Gas-shielded FCAW, on the other hand, relies on an external shielding gas, typically a mixture of carbon dioxide and argon, to protect the weld from contamination.
Features to consider when choosing a Flux Cored Arc Welder
When selecting a Flux Cored Arc Welder, it's important to consider certain features that can affect the welding performance. Some key factors to look for include the welder's power output, wire feed speed control, duty cycle, portability, and the ability to handle different wire sizes.
How to Use a Flux Cored Arc Welder
Using a Flux Cored Arc Welder requires proper setup and welding techniques to ensure safe and effective welding. Here are the essential steps:
Safety precautions
Before starting any welding operation, it is crucial to prioritize safety. Make sure to wear appropriate protective gear, including a welding helmet, gloves, and flame-resistant clothing. Additionally, ensure proper ventilation in the workspace and remove any flammable materials from the vicinity.
Setting up the Flux Cored Arc Welder
Start by selecting the correct wire size and type for your project. Refer to the welder's manual or consult with welding professionals for guidance. Next, prepare the welding machine by connecting it to a suitable power source and attaching the ground clamp securely. Adjust the wire feed speed and voltage settings according to the recommended parameters for your welding application.
Welding techniques
To achieve high-quality welds, it is crucial to master the proper welding techniques. Maintain a steady travel speed and a consistent arc length throughout the welding process. Pay attention to the angle and direction of the welding gun, ensuring proper penetration and fusion. Practice these techniques on scrap material before working on your actual project.
Common mistakes to avoid
When using a Flux Cored Arc Welder, it's essential to be aware of common mistakes that can compromise the quality of the weld. Avoid excessive heat input, as it can lead to distortion and weakened welds. Ensure proper joint preparation, including cleaning and removal of any contaminants. Additionally, be mindful of proper wire extension and gun angle to prevent irregular bead formation.
Applications of Flux Cored Arc Welding
Flux Cored Arc Welding finds applications in various industries due to its versatility and efficiency. Some common areas where FCAW is extensively used include:
Construction industry
FCAW is widely employed in the construction industry for welding structural steel, beams, and columns. Its high deposition rates and deep penetration capabilities make it suitable for fast and robust welding in large-scale construction projects.
Automotive industry
Flux Cored Arc Welding plays a vital role in the automotive industry, particularly for welding vehicle frames, exhaust systems, and body panels. The process's ability to weld different materials, such as carbon steel and stainless steel, makes it indispensable in automotive manufacturing and repairs.
Manufacturing industry
FCAW is extensively used in the manufacturing industry for various applications, including welding of heavy equipment, storage tanks, and machinery components. The process's high welding speeds and excellent penetration allow for efficient production and cost-effective manufacturing.
Benefits of Flux Cored Arc Welding
Flux Cored Arc Welding offers several notable benefits that make it a preferred choice in many welding applications. These benefits include:
Increased welding speed
Compared to other welding processes, FCAW allows for faster welding speeds due to its high deposition rates. This means that more weld metal can be deposited in a shorter period, increasing productivity and reducing project timelines.
Enhanced weld quality
The Flux Cored Arc Welding process provides deep penetration and excellent fusion, resulting in high-quality welds. The use of flux within the electrode helps to clean impurities and provides additional protection, ensuring weld integrity.
Versatility and accessibility
FCAW is a versatile process that can be applied to a wide range of materials and thicknesses. It is accessible to both professional welders and DIY enthusiasts, as it does not require complex equipment or an external shielding gas in the case of self-shielded FCAW.
Cost-effectiveness
Due to its high deposition rates and increased welding speed, FCAW offers cost savings in terms of labor and materials. The efficiency of the process allows for faster project completion, reducing labor costs, while the ability to weld different materials eliminates the need for multiple welding processes.
Comparison between Flux Cored Arc Welding and other welding processes
To understand the advantages of Flux Cored Arc Welding better, let's compare it with two popular welding processes: Shielded Metal Arc Welding (SMAW) and Gas Metal Arc Welding (GMAW).
Flux Cored Arc Welding vs. Shielded Metal Arc Welding (SMAW)
Unlike SMAW, where the welder manually feeds the electrode and creates a slag coating, FCAW utilizes a continuously fed tubular electrode with flux. This results in higher deposition rates and faster welding speeds, making FCAW more efficient for large-scale projects. Additionally, FCAW allows for deeper penetration and better weld quality.
Flux Cored Arc Welding vs. Gas Metal Arc Welding (GMAW)
Both FCAW and GMAW use continuously fed electrodes, but the key difference lies in the shielding gas. GMAW requires an external shielding gas, while FCAW can be either self-shielded or gas-shielded. The choice between the two processes depends on the specific welding requirements, such as the need for portability, welding speed, and the materials being welded.
Maintenance and troubleshooting of Flux Cored Arc Welders
Proper maintenance and troubleshooting of Flux Cored Arc Welders are essential to ensure their longevity and optimal performance. Here are some maintenance tips and common issues you may encounter:
Cleaning and storage
Regularly clean the welding gun, wire feeder, and other components to remove any welding spatter, debris, or flux residue. Inspect and replace consumables, such as contact tips and nozzles, as needed. When storing the welder, ensure it is kept in a dry and protected area to prevent damage from moisture or dust.
Common issues and solutions
Some common issues with Flux Cored Arc Welders include wire feed problems, erratic arc, and insufficient penetration. If you encounter wire feed issues, check for obstructions in the wire feed path and ensure proper tension on the wire spool. For erratic arc or insufficient penetration, review your welding techniques, including travel speed, arc length, and gun angle.
Flux Cored Arc Welder (Semi-Automatic) FAQs
1. Can Flux Cored Arc Welding be used for outdoor welding?
Absolutely! Flux Cored Arc Welding is suitable for both indoor and outdoor welding applications. The flux within the electrode provides the necessary shielding gases, making it resistant to atmospheric contamination.
2. What types of materials can be welded using Flux Cored Arc Welding?
Flux Cored Arc Welding can be used to weld various materials, including carbon steel, stainless steel, low-alloy steel, and even some non-ferrous metals. The specific type of flux and wire electrode will depend on the material being welded.
3. Is Flux Cored Arc Welding suitable for beginners?
Yes, Flux Cored Arc Welding can be a great choice for beginners due to its ease of use and versatility. However, proper training and practice are still essential to ensure safe and effective welding.
4. Can Flux Cored Arc Welders be used for thin materials?
Yes, Flux Cored Arc Welders can be used for welding thin materials. By adjusting the welding parameters and using a suitable wire size, you can achieve precise and controlled welds on thin gauge materials.
5. How often should I perform maintenance on my Flux Cored Arc Welder?
Regular maintenance is crucial to keep your Flux Cored Arc Welder in optimal condition. Perform cleaning and inspections after each use, and follow the manufacturer's guidelines for routine maintenance. It's recommended to have a professional inspection at least once a year to address any potential issues and ensure safe operation.