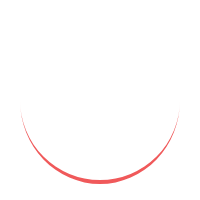
Outline
Introduction
What is X-ray Welding?
The Process of X-ray Welding
Preparation
Equipment and Materials
Procedure
Advantages of X-ray Welding
Quality Control
Non-Destructive Testing
Cost Efficiency
Applications of X-ray Welding
Aerospace Industry
Automotive Industry
Oil and Gas Industry
Challenges and Limitations of X-ray Welding
Safety Considerations
Complexity and Skill Requirement
Cost of Equipment
Future Developments in X-ray Welding Technology
Conclusion
FAQs
Is X-ray welding safe for operators?
Can X-ray welding detect all types of defects?
How long does it take to perform an X-ray welding inspection?
Is X-ray welding widely used in the construction industry?
What are the alternatives to X-ray welding for quality control in welding?
X-ray Welding is a cutting-edge welding technique that offers precise and reliable results in various industries. This article will delve into the process of X-ray welding, its advantages, applications, challenges, and future developments.
Welding is a fundamental process in manufacturing and construction industries, used to join two or more metal pieces together. X-ray welding, also known as radiographic testing, is a non-destructive testing method that utilizes X-ray radiation to assess the integrity of welds. This advanced technique provides a comprehensive analysis of the weld quality by detecting internal defects and ensuring structural soundness.
X-ray welding involves the use of X-ray beams to create images of welds. These X-ray images allow inspectors to examine the internal structure of the weld and identify any defects or inconsistencies. It is an invaluable tool for quality control and ensures the weld meets the required standards.
Preparation
Before conducting an X-ray welding inspection, proper preparation is essential. This includes cleaning the weld surface, removing any contaminants, and ensuring that the area is free from any obstructions that could affect the accuracy of the results.
X-ray welding requires specialized equipment, including an X-ray machine, a film or digital detector, and a source of radiation. The X-ray machine produces the necessary radiation, which passes through the weld and is captured by the detector.
During an X-ray welding inspection, the X-ray machine is positioned on one side of the weld, while the detector is placed on the opposite side. The X-ray radiation passes through the weld, creating an image on the detector. This image is then analyzed by experts to determine the quality of the weld and identify any defects.
Quality Control
X-ray welding provides superior quality control by detecting internal defects that may not be visible to the naked eye. It ensures that the weld is structurally sound, preventing potential failures and enhancing overall safety.
Unlike destructive testing methods that require cutting or damaging the weld, X-ray welding is non-destructive. This means that the weld can be inspected without compromising its integrity, reducing material waste and saving both time and money.
While X-ray welding requires initial investment in equipment and training, it offers long-term cost efficiency. By identifying and rectifying defects early in the welding process, it reduces the likelihood of rework, repairs, and potential failures, saving valuable resources in the long run.
Aerospace Industry
X-ray welding plays a critical role in the aerospace industry, where the integrity of welds is of utmost importance. It ensures the reliability and safety of aircraft structures, engines, and components.
In the automotive industry, X-ray welding is utilized for manufacturing vehicles with high-quality welds. It ensures the structural integrity of critical components such as chassis, frames, and exhaust systems.
Oil and Gas Industry
X-ray welding is extensively employed in the oil and gas industry for welding pipelines, storage tanks, and offshore structures. It guarantees the strength and durability of these vital assets, minimizing the risk of leaks and accidents.
Safety Considerations
X-ray radiation can be hazardous to human health, requiring strict safety measures and proper shielding. Operators must be trained in radiation safety to minimize the risks associated with X-ray welding.
Complexity and Skill Requirement
X-ray welding is a complex technique that demands skilled operators and technicians. Interpreting X-ray images requires expertise to identify and assess various types of defects accurately.
Cost of Equipment
The initial cost of X-ray welding equipment can be significant, making it less accessible for small-scale operations. However, the long-term cost savings and quality assurance justify the investment for industries heavily reliant on welding.
X-ray welding technology is continually evolving, driven by advancements in imaging and radiation detection. Researchers are exploring digital radiography, computed tomography (CT), and automated inspection systems to further enhance the accuracy and efficiency of X-ray welding.
X-ray welding is a powerful technique that enables precise and reliable weld inspections, ensuring structural integrity and quality control. With its non-destructive nature, cost efficiency, and applications in various industries, X-ray welding has become an indispensable tool for welders and manufacturers worldwide.
Is X-ray welding safe for operators?
Yes, X-ray welding can be safe for operators if proper safety measures and shielding are in place. Operators should receive adequate training in radiation safety to minimize any health risks.
Can X-ray welding detect all types of defects?
X-ray welding is effective in detecting a wide range of defects, including cracks, porosity, inclusions, and incomplete fusion. However, it may not detect certain defects such as surface irregularities or minor discontinuities.
How long does it take to perform an X-ray welding inspection?
The duration of an X-ray welding inspection depends on various factors, including the complexity of the weld, the size of the component, and the required level of detail. Generally, it can take anywhere from a few minutes to several hours.
Is X-ray welding widely used in the construction industry?
X-ray welding is commonly used in the construction industry, particularly for critical welds in infrastructure projects, bridges, and buildings. It ensures the structural integrity and safety of these structures.
What are the alternatives to X-ray welding for quality control in welding?
Other non-destructive testing methods, such as ultrasonic testing and magnetic particle inspection, can be used as alternatives to X-ray welding for quality control in welding. The choice of method depends on the specific requirements and the type of defects to be detected.
X-ray Welding is a test welding process that uses a powerful X-ray source to give warm vitality required to weld materials.
The expression "X-ray welding" additionally has a more seasoned, inconsequential utilization in quality control. In this unique situation, a X-Ray welder is a tradesman who reliably welds at such a high capability, that he once in a while brings deserts into the weld pool, and can perceive and address surrenders in the weld pool, during the welding procedure. It is accepted (or trusted) by the Quality Control Department of creation or assembling shop that the welding work performed by an X-ray welder would pass an X-ray examination. For instance, surrenders like porosity, concavities, splits, cold laps, slag and tungsten incorporations, absence of combination and entrance, and so forth., are once in a while found in a radiographic X-beam examination of a weldment performed by an X-ray welder.
With the developing utilization of synchrotron radiation in the welding procedure, the more seasoned use of the expression "X-Ray welding" may cause disarray; yet the two terms are probably not going to be utilized in a similar workplace since synchrotron radiation (X-Ray) welding is a remotely robotized and motorized procedure.
Qualification