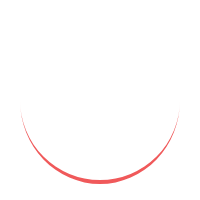
Submerged arc welding (SAW) is a versatile and widely used welding process that offers numerous benefits in various industrial applications. Whether it's shipbuilding, pressure vessel fabrication, or infrastructure projects, SAW provides efficient and high-quality welds. In this article, we will delve into the details of submerged arc welding, its process, advantages, applications, and factors to consider for successful implementation.
Submerged arc welding offers several advantages over other welding techniques, making it a preferred choice for many industries. Its high deposition rates, deep penetration, and ease of automation contribute to its popularity in various applications.
2. Understanding Submerged Arc Welding Process
To perform submerged arc welding, specialized equipment is required. A typical setup includes a power source, welding head, wire feeder, flux delivery system, and a flux recovery unit. The welding head holds the electrode and maintains the desired arc length and position.
During the welding process, a continuous wire electrode is fed into the joint, and a layer of granular flux covers the arc and weld pool. The heat generated by the arc melts both the electrode wire and the workpiece, forming a weld with strong metallurgical bonding. The flux provides shielding and deoxidation, improving the quality of the weld.
3. Benefits of Submerged Arc Welding
Submerged arc welding offers several advantages that make it an attractive option for various applications:
Submerged Arc Welder - High Deposition Rates:
One of the key benefits of submerged arc welding is its ability to achieve high deposition rates. The continuous wire feeding and the use of multiple electrodes allow for efficient and rapid welding. This makes SAW particularly suitable for applications that require high productivity and the joining of thick sections.
Submerged Arc Welder - Deep Penetration and Strong Welds:
Submerged arc welding provides deep penetration, resulting in strong and reliable welds. The process can effectively handle joints with a large gap and is well-suited for welding thick materials. The combination of deep penetration and excellent fusion characteristics contributes to the overall integrity and strength of the weld.
Submerged Arc Welder - Minimal Operator Skill Requirements:
SAW is a highly mechanized process that requires minimal operator skill. The use of automated welding systems and dedicated equipment reduces the dependence on manual labor and ensures consistent weld quality. This makes submerged arc welding an excellent choice for large-scale production and repetitive welding tasks.
4. Applications of Submerged Arc Welding
Submerged arc welding finds extensive applications in various industries due to its unique advantages. Some notable applications include:
Submerged Arc Welder- Shipbuilding and Offshore Structures:
The shipbuilding industry extensively utilizes submerged arc welding for fabricating large structures, such as hulls, decks, and bulkheads. The process's high deposition rates and ability to weld thick plates make it an efficient and cost-effective choice.
Submerged Arc Welder - Pressure Vessel Fabrication:
Submerged arc welding is commonly employed in the fabrication of pressure vessels, such as boilers, reactors, and storage tanks. The deep penetration and high-quality welds achieved by SAW ensure the structural integrity and reliability required for such critical applications.
Submerged Arc Welder - Bridge Construction and Infrastructure Projects:
The construction of bridges, viaducts, and other infrastructure projects often involves the use of submerged arc welding. The process's ability to handle thick sections and its efficient deposition rates make it ideal for joining large structural components.
5. Factors to Consider for Successful Submerged Arc Welding
To achieve optimal results in submerged arc welding, several factors must be taken into account:
Submerged Arc Welder - Proper Joint Preparation:
Thorough joint preparation, including cleaning, beveling, and alignment, is essential for successful submerged arc welding. Proper fit-up and removal of contaminants ensure sound welds and minimize the risk of defects.
Submerged Arc Welder - Control of Welding Parameters:
Precise control of welding parameters, such as current, voltage, and travel speed, is crucial for achieving the desired weld quality. These parameters vary depending on the joint geometry, material thickness, and welding position, and should be optimized for each specific application.
Submerged Arc Welder - Flux Selection and Usage:
The selection and proper use of flux play a significant role in submerged arc welding. Different types of fluxes are available, each designed for specific applications and material combinations. The correct flux selection ensures efficient shielding, slag removal, and desirable weld properties.
6. Advancements and Innovations in Submerged Arc Welding
Submerged arc welding has seen continuous advancements and innovations, leading to improved efficiency and quality. Some notable developments include:
- Welding Automation and Robotics:
The integration of automation and robotics has revolutionized submerged arc welding. Automated systems can handle complex welding tasks, ensuring precise control and consistent results. Robotic welding arms offer enhanced flexibility, reaching challenging areas and improving overall productivity.
- Development of New Fluxes and Electrodes:
Extensive research and development efforts have led to the introduction of new fluxes and electrodes for submerged arc welding. These innovative consumables provide enhanced performance, better slag detachability, and improved mechanical properties in the welds.
- Improved Monitoring and Quality Control Systems:
Advanced monitoring and quality control systems have been developed to ensure the integrity of submerged arc welding. Real-time monitoring of welding parameters, weld profiles, and quality indicators allows for immediate adjustments and ensures adherence to specified standards.
7. Common Challenges and Troubleshooting in Submerged Arc Welding
While submerged arc welding offers numerous benefits, certain challenges may arise during the process. Understanding these challenges and troubleshooting them is essential for achieving high-quality welds:
Submerged Arc Welder - Porosity and Slag Inclusions:
Improper flux selection, inadequate cleaning of the joint, or excessive moisture in the flux can lead to porosity and slag inclusions in the weld. Proper flux handling, control of welding parameters, and adherence to pre-welding procedures can help mitigate these issues.
Submerged Arc Welder - Cracking and Distortion:
Large weld sections and high heat input can result in cracking and distortion in submerged arc welding. Proper joint preparation, control of heat input, and the use of appropriate welding techniques, such as preheating or post-weld heat treatment, can minimize these concerns.
Submerged Arc Welder - Weld Metal Hydrogen Content:
Excessive moisture in the flux or inadequate control of welding conditions can lead to increased hydrogen content in the weld metal, resulting in hydrogen-induced cracking. Proper drying of flux, maintaining low humidity in the welding environment, and controlling heat input can prevent this issue.
8. Safety Precautions and Personal Protective Equipment (PPE)
Safety is of utmost importance in submerged arc welding. Several safety precautions should be followed to protect welders and others in the vicinity:
Submerged Arc Welder - Welding Fumes and Ventilation:
Submerged arc welding generates welding fumes that can be hazardous to health. Adequate ventilation, including local exhaust systems and proper respiratory protection, should be employed to minimize exposure to fumes and ensure a safe working environment.
Submerged Arc Welder - Eye and Face Protection:
Welders must wear appropriate eye and face protection to shield themselves from the intense arc light, sparks, and flying debris. Welding helmets or face shields with the correct shade of filter lenses provide the necessary protection.
Submerged Arc Welder - Heat and Fire Hazards:
Submerged arc welding involves high temperatures that can pose fire hazards. Proper fire prevention measures, including fire-resistant clothing, clear work areas, and fire extinguishers, should be in place to mitigate the risk of accidents.
Submerged Arc Welder FAQs (Frequently Asked Questions)
Q1. Can submerged arc welding be used for thin materials?
Yes, submerged arc welding can be used for thin materials. However, careful control of welding parameters, such as current, voltage, and travel speed, is necessary to prevent excessive heat input and distortion.
Q2. Is submerged arc welding suitable for outdoor applications?
Submerged arc welding can be used for outdoor applications. However, the welding area should be protected from environmental factors such as wind, rain, and excessive moisture that can affect the flux and the quality of the weld.
Q3. What types of materials can be welded using submerged arc welding?
Submerged arc welding is suitable for welding a wide range of materials, including carbon steel, low-alloy steel, stainless steel, and some non-ferrous metals.
Q4. Can submerged arc welding be automated?
Yes, submerged arc welding is highly amenable to automation. Automated systems and robotic welding arms can be employed to increase productivity, ensure consistent weld quality, and reduce manual labor.
Q5. How does submerged arc welding compare to other welding processes, such as TIG or MIG?
Submerged arc welding offers higher deposition rates and deeper penetration compared to TIG or MIG welding. It is particularly suitable for joining thick materials and large structural components, while TIG and MIG welding excel in applications that require precise control and fine welding.