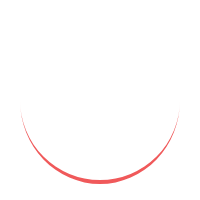
Are you someone who loves to explore and appreciate unique art forms? Do you enjoy admiring the beauty of handmade objects and appreciate the skill and craftsmanship that goes into creating them? If yes, then you must take a closer look at the art of Sieving Artisan (Ceramics).
The Sieving Artisan (Ceramics) Introduction
Sieving Artisan (Ceramics) is a traditional pottery-making technique that has been passed down from generation to generation. This art form originated in Japan and has gained popularity worldwide. The unique aspect of Sieving Artisan (Ceramics) is the use of a special sieve to create intricate patterns on the surface of the ceramic pieces. These patterns not only add an aesthetic appeal to the pieces but also provide a tactile experience to the users.
Sieving Artisan (Ceramics)
Sieving Artisan (Ceramics) involves the use of a sieve, which is a mesh screen that is used to sift and refine materials. In pottery making, the sieve is used to create patterns on the surface of the ceramic piece. The artisan pours the slip (liquid clay) onto the sieve and lets it flow through the mesh screen onto the surface of the piece. The patterns are created as a result of the different size holes on the mesh screen.
The technique requires a lot of skill and patience, as the artisan needs to be able to control the flow of the slip and the movement of the sieve to create the desired pattern. The patterns created can range from simple geometric shapes to intricate designs inspired by nature.
The Sieving Artisan (Ceramics) The Materials Used
Sieving Artisan (Ceramics) requires specific materials to create the patterns. These materials include:
Clay: This is the primary material used in pottery making. The clay used in Sieving Artisan (Ceramics) is typically a blend of different types of clay to achieve the desired properties, such as strength and flexibility.
Slip: This is a liquid clay that is used to coat the surface of the ceramic piece before firing. The slip is poured onto the sieve to create the patterns.
Sieve: This is the mesh screen that is used to create the patterns. The size of the holes on the mesh screen determines the size of the patterns created.
Firing: After the patterns are created, the ceramic piece is fired in a kiln at high temperatures to harden the clay and create a durable piece of pottery.
The Sieving Artisan (Ceramics) The Process
The process of Sieving Artisan (Ceramics) involves several steps. These include:
Preparing the Clay: The clay is prepared by mixing different types of clay to achieve the desired properties.
Creating the Ceramic Piece: The artisan shapes the clay into the desired form, such as a bowl or a vase.
Applying the Slip: The slip is poured onto the sieve, and the artisan uses a brush to coat the surface of the ceramic piece with the slip.
Sieving the Slip: The artisan pours the slip onto the sieve and uses a tool to move the sieve to create the desired pattern.
Firing: The ceramic piece is fired in a kiln at high temperatures to harden the clay and create a durable piece of pottery.
The Beauty of Sieving Artisan (Ceramics)
The beauty of Sieving Artisan (Ceramics) lies in its unique patterns and tactile experience. The patterns created using the sieve are one of a kind and cannot be replicated using any other method. The tactile experience provided by the patterns adds a new dimension to the ceramic piece, making it more than just a visual piece of art.
The patterns created using Sieving Artisan (Ceramics) can be simple or complex, depending on the
The Beauty of Sieving Artisan (Ceramics)
The beauty of Sieving Artisan (Ceramics) lies in its unique patterns and tactile experience. The patterns created using the sieve are one of a kind and cannot be replicated using any other method. The tactile experience provided by the patterns adds a new dimension to the ceramic piece, making it more than just a visual piece of art.
The patterns created using Sieving Artisan (Ceramics) can be simple or complex, depending on the skill level of the artisan. Some patterns are inspired by nature, such as flowers, leaves, and vines, while others are geometric shapes or abstract designs. The patterns can be created using a single color or multiple colors to create a stunning visual effect.
The History of Sieving Artisan (Ceramics)
Sieving Artisan (Ceramics) has a long history that dates back to the Edo period in Japan, which lasted from 1603 to 1868. During this time, the art form was known as Kakiemon, named after the family that popularized the technique. The Kakiemon family was known for creating porcelain pieces with intricate designs using a sieve. The technique was later adapted by other artisans and became popular throughout Japan.
In modern times, Sieving Artisan (Ceramics) has gained popularity worldwide and is considered a unique and valuable art form. Today, there are many artisans who specialize in Sieving Artisan (Ceramics) and continue to explore new patterns and techniques to create stunning pieces of pottery.
The Sieving Artisan (Ceramics) The Importance of Supporting Artisans
As with any art form, supporting artisans who specialize in Sieving Artisan (Ceramics) is important. By purchasing their pieces, you are not only supporting their livelihood but also preserving a traditional art form. Many artisans who specialize in Sieving Artisan (Ceramics) are small business owners who rely on the support of their local communities and customers to sustain their businesses.
By supporting artisans who specialize in Sieving Artisan (Ceramics), you are also helping to keep the art form alive and thriving. The knowledge and techniques passed down from generation to generation are valuable and should be preserved for future generations to enjoy.
The Sieving Artisan (Ceramics) FAQ
Q1. What kind of patterns can be created using Sieving Artisan (Ceramics)?
A1. The patterns created using Sieving Artisan (Ceramics) can range from simple geometric shapes to intricate designs inspired by nature. The patterns can be created using a single color or multiple colors to create a stunning visual effect.
Q2. What materials are used in Sieving Artisan (Ceramics)?
A2. The materials used in Sieving Artisan (Ceramics) include clay, slip, a sieve, and firing equipment.
Q3. How long does it take to create a piece of Sieving Artisan (Ceramics)?
A3. The time it takes to create a piece of Sieving Artisan (Ceramics) depends on the size and complexity of the piece. It can take anywhere from a few hours to several days to create a single piece.
Q4. What is the history of Sieving Artisan (Ceramics)?
A4. Sieving Artisan (Ceramics) has a long history that dates back to the Edo period in Japan, which lasted from 1603 to 1868. During this time, the art form was known as Kakiemon and was popularized by the Kakiemon family.
Q5. Where can I buy pieces of Sieving Artisan (Ceramics)?
A5. You can buy pieces of Sieving Artisan (Cer
Where to Buy Sieving Artisan (Ceramics)
Sieving Artisan (Ceramics) can be found in specialty stores and online marketplaces. It is also possible to purchase pieces directly from the artisans who create them. Many artisans have online shops or participate in local craft fairs and art shows, where they sell their pieces directly to customers.
If you are interested in purchasing Sieving Artisan (Ceramics), it is recommended to do some research to find reputable sellers and artisans. Reading reviews and checking for certifications or awards can help ensure that you are buying high-quality pieces.
How to Care for Sieving Artisan (Ceramics)
Caring for Sieving Artisan (Ceramics) is important to ensure that the pieces last for years to come. To care for your Sieving Artisan (Ceramics), it is recommended to follow these steps:
Avoid exposing the pieces to extreme temperatures or sudden changes in temperature, which can cause cracking or damage.
Use a soft cloth or brush to dust the pieces regularly. Avoid using abrasive cleaners or harsh chemicals.
Handle the pieces carefully to avoid dropping or chipping them. Store the pieces in a secure location when not in use.
If the pieces become stained or dirty, use a mild soap and water to gently clean them. Avoid soaking the pieces in water for extended periods of time.
About Us
This OS unit is about mixing various raw materials, mold making shaping, baking, and coloring toys to make a final ceramic toy product.
Personal Attributes
The individual must have attention to detail, logical thinking, hand-eye coordination, good analytical skills, problem-solving skills, reliability, good decision-making skills, basic mathematical skills and should not have color blindness. The individual should be good at following instructions.